LP12: Plinth change and torque discussions
Moderator: Staff
cartridge torque
>On the other hand, I can't spend hours evaluating one parameter when
>there are hundreds of similar comparisons to follow.
Yes, that's exactly the point. With an increasing number of 'training hours'
decisions need less time for us hobbyists, too.
Now the basic setting is done satisfactorily, the next issue would be
the cartridge torque. What is the best procedure to adjust it? Up to date
I followed the advise to de-install the arm for mounting or
disassembling the cartridge, of course. (The cartridge is
mounted solidly, but not to a specified torque.) If the arm needs to be
removed and installed for each cart torque modification, I wonder how to
come to a conclusion ever. In particluar because all the other adjustments
(e.g. arm bolt torque) are so sensitive that I'm afraid to loose the
setting by a reinstallation.
And is it possible to describe the performance peak? (Steep
peak or somewhat wider plateau? Multiple peaks? (I found it
very helpful to find a description of the antiskating peak that
mentioned that things get continuously better with increasing bias and very
suddenly drop dramatically.))
Regards, Klaus
>there are hundreds of similar comparisons to follow.
Yes, that's exactly the point. With an increasing number of 'training hours'
decisions need less time for us hobbyists, too.
Now the basic setting is done satisfactorily, the next issue would be
the cartridge torque. What is the best procedure to adjust it? Up to date
I followed the advise to de-install the arm for mounting or
disassembling the cartridge, of course. (The cartridge is
mounted solidly, but not to a specified torque.) If the arm needs to be
removed and installed for each cart torque modification, I wonder how to
come to a conclusion ever. In particluar because all the other adjustments
(e.g. arm bolt torque) are so sensitive that I'm afraid to loose the
setting by a reinstallation.
And is it possible to describe the performance peak? (Steep
peak or somewhat wider plateau? Multiple peaks? (I found it
very helpful to find a description of the antiskating peak that
mentioned that things get continuously better with increasing bias and very
suddenly drop dramatically.))
Regards, Klaus
I interprete the silence in the air - I´m obviously the only one who
follows the 'official' guidelines to avoid touching the scews of the
cartridge with the tonearm installed. In fact I always wondered why
the bearings should be that weak not to take this small force. With
this implicit advice work is getting much easier!
Regards, Klaus
follows the 'official' guidelines to avoid touching the scews of the
cartridge with the tonearm installed. In fact I always wondered why
the bearings should be that weak not to take this small force. With
this implicit advice work is getting much easier!
Regards, Klaus
Ha ha! You knew you'd get a reply now, didn't you? Sorry for being late with it, I've just been busy with new circuits.k_numigl wrote:With this implicit advice work is getting much easier!
Always remove the arm! The only exception to this rule is when the cartridge is to be rather loosely tightened, like the Adikt. As the Adikt sounds optimal just over 0.2 Nm, it's completely risk free tightening with that torque with the arm still in place. The force isn't more than what's needed to take the arm out of its rest.
Metallic bodied carts should be done tighter and I would never do that with the arm still in place. I don't know where the exact limit is for arm bearing damage and I don't intend to find out by trial and error.
I'm afraid that you might have been more correct in the interpretation of MY silence. I will state up front that you are safest removing the arm and in most cases I do this when setting up Linn arms. However, I really feel that a lot of this concern comes from the days when Linn tight meant tightened by gorillas. There is no question that in the early days we were taught to tighten cartridges and arms (and many parts of the LP12) so much that we were really over-tightening things and sometimes causing physical damage. When I think back on it I have to shake my head at the forces we used on Ittoks and Troikas or Karmas. Certainly at the forces we used then you could easily damage the bearings tightening the cartridge with the arm mounted.
In these days of more sane setup procedures and torque screwdrivers I believe that these precautions are at least sometimes unnecessary. Fredrik mentions that the Adikt has such a low preferred torque that you don't have to worry about it and I agree (Grado plastic bodied cartridges are similarly low). But what about other cartridges? Well, I have found that the vast majority of other cartridges I have optimized have been best somewhere around 0.4Nm. This includes the Klyde and a number of metal body cartridges, or ones with metal mounts, from Lyra, Sumiko, Benz, Shelter and others. Now 0.4Nm is what the Rega torque wrench is designed to apply to their cartridges and arms and nobody recommends removing their arms for cartridge tightening. Does Linn have wimpier bearings than Rega?
Strictly speaking I have never seen a Linn arm with bearing damage (other than Akito 1s) that wasn't treated with a really heavy hand.
Once again the disclaimer that you do any tightening of cartridges with the arm in place at your own risk. However, if you should wish to do so I would recommend holding the arm behind the headshell with one hand while tightening with the other. This would tend to absorb some (possibly much) of the force that would otherwise transfer directly to the bearings and will also make the headshell a very short lever. That said I would caution extreme care when fastening a cartridge that needs a lot of torque such as the Arkiv and Akiva.
So there Klaus, I haven't quite given you carte blanche. :) I will now duck for cover as I await the flames! :shock:
In these days of more sane setup procedures and torque screwdrivers I believe that these precautions are at least sometimes unnecessary. Fredrik mentions that the Adikt has such a low preferred torque that you don't have to worry about it and I agree (Grado plastic bodied cartridges are similarly low). But what about other cartridges? Well, I have found that the vast majority of other cartridges I have optimized have been best somewhere around 0.4Nm. This includes the Klyde and a number of metal body cartridges, or ones with metal mounts, from Lyra, Sumiko, Benz, Shelter and others. Now 0.4Nm is what the Rega torque wrench is designed to apply to their cartridges and arms and nobody recommends removing their arms for cartridge tightening. Does Linn have wimpier bearings than Rega?
Once again the disclaimer that you do any tightening of cartridges with the arm in place at your own risk. However, if you should wish to do so I would recommend holding the arm behind the headshell with one hand while tightening with the other. This would tend to absorb some (possibly much) of the force that would otherwise transfer directly to the bearings and will also make the headshell a very short lever. That said I would caution extreme care when fastening a cartridge that needs a lot of torque such as the Arkiv and Akiva.
So there Klaus, I haven't quite given you carte blanche. :) I will now duck for cover as I await the flames! :shock:
Last edited by ThomasOK on 2011-01-23 00:07, edited 1 time in total.
Fredrik, this was only half in jest, but you are of course right, the other
half was........
The problem for me remains as described: When I disassemble and
reassemble the arm so many times as I needed for finding the right
torque for the tonearm bolt, I will be simply lost. And if, second, the
modifications need so tiny steps to find the optimum, things are
getting even worse. Thus, it seems not unreasonable to consider methods
how to make adjustments to the cart bolts with the arm installed while
avoiding damage to the bearings. (Cart is an Akiva, but don't you
mean 0.4 Nm for the others, Thomas?)
I did not start to work at those cart bolts, as I liked to discuss it before
acting. This is not urgent, so please don't get distracted from higher
priority work.
My general idea how to proceed is: Mount the cartridge with the arm
off and use a torque tool to tighten it to near what is expected to be
a good value. Then mount the arm. Do not use a torque tool for
further adjustments, but use a standard 2mm hex wrench (preferably
with the short end cut even shorter). Make adjustments with it
observing the _angle_ you turn it as a substitute for torquing. If one
is using not two hands, but the fingers of only one, acting on the
wrench and on the corresponing position at the tonearm, the bearing
should see no force at all.
With this method one should be able to make tiny modifications
which can be found repeatedly with a good precision. The amount
of force the bearings will see depends on the perfection of ones
handling, i.e. how perfect one can balance the force on the wrench
by finger counteraction on the tonearm tube.
Do you consider this as a reasonable approach?
Question 2 remains whether the shape of the maximum can be
described roughly?
Kind regards, Klaus
half was........
The problem for me remains as described: When I disassemble and
reassemble the arm so many times as I needed for finding the right
torque for the tonearm bolt, I will be simply lost. And if, second, the
modifications need so tiny steps to find the optimum, things are
getting even worse. Thus, it seems not unreasonable to consider methods
how to make adjustments to the cart bolts with the arm installed while
avoiding damage to the bearings. (Cart is an Akiva, but don't you
mean 0.4 Nm for the others, Thomas?)
I did not start to work at those cart bolts, as I liked to discuss it before
acting. This is not urgent, so please don't get distracted from higher
priority work.
My general idea how to proceed is: Mount the cartridge with the arm
off and use a torque tool to tighten it to near what is expected to be
a good value. Then mount the arm. Do not use a torque tool for
further adjustments, but use a standard 2mm hex wrench (preferably
with the short end cut even shorter). Make adjustments with it
observing the _angle_ you turn it as a substitute for torquing. If one
is using not two hands, but the fingers of only one, acting on the
wrench and on the corresponing position at the tonearm, the bearing
should see no force at all.
With this method one should be able to make tiny modifications
which can be found repeatedly with a good precision. The amount
of force the bearings will see depends on the perfection of ones
handling, i.e. how perfect one can balance the force on the wrench
by finger counteraction on the tonearm tube.
Do you consider this as a reasonable approach?
Question 2 remains whether the shape of the maximum can be
described roughly?
Kind regards, Klaus
Just a quick reply as its time for me to get out of here. I did indeed mean 0.4Nm and have corrected my post. You would think that I would have caught that since I tend to proofread things at least twice before I post them. :?
As to the method mentioned about how to apply the torque, I don't think it matters whether you use a torque screwdriver or a little Rega hex wrench - .9Nm is .9Nm regardless of how you apply it. Your idea of holding the armtube with one hand negating or reducing the force on the bearings sounds much like what I said if I am reading it correctly. It will be interesting to see what others feel but I think you are certainly opening up a can of worms with the question. :)
As to the method mentioned about how to apply the torque, I don't think it matters whether you use a torque screwdriver or a little Rega hex wrench - .9Nm is .9Nm regardless of how you apply it. Your idea of holding the armtube with one hand negating or reducing the force on the bearings sounds much like what I said if I am reading it correctly. It will be interesting to see what others feel but I think you are certainly opening up a can of worms with the question. :)
ThomasOK wrote: Your idea of holding the armtube with one hand negating or reducing the force on the bearings sounds much like what I said if I am reading it correctly.
Yes, we have the same idea. The only difference is to apply an 'arm to
arm' action or 'finger to finger' action. I thought it is easier to avoid an
unbalanced action by using the fingers of one hand only. The screw head
always 'sees' 0.9 Nm, of course.
I think what suppliers are really (and rightly) afraid of is that peopleThomasOK wrote: It will be interesting to see what others feel but I think you are certainly opening up a can of worms with the question. :)
act on the tonearm head using the tonearm rest as a pivot point. This being
5 cm from the bearings and 10 cm from the head, forces into the bearings
get multiplied. I understand fully that they do not trust fine motor skills
of the average consumer. On the other hand they allow that people
grab the tonearm head and force it into the rest - instead of pushing
the tube into the rest by a 2-finger counteraction tube against rest clamp.
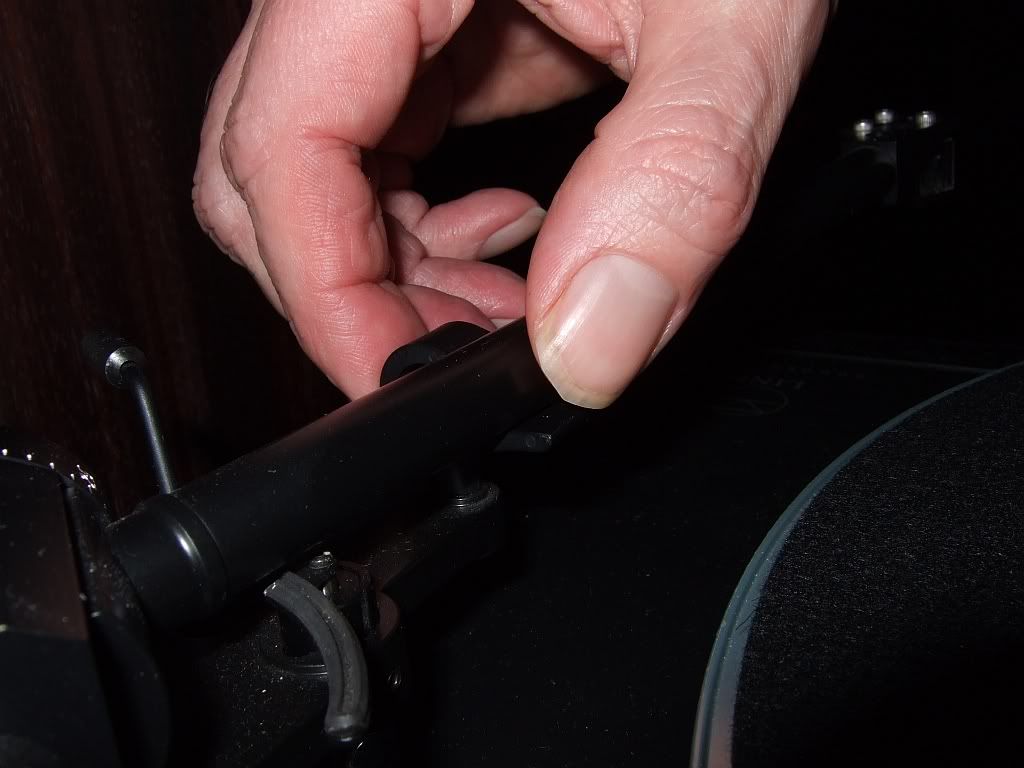
Regards, Klaus
Springology
Please excuse this somewhat lengthy post – but I could not find much information about the issue of springs in the LP12, how they behave and how to cope with them (except not to loose patience when adjusting the deck). So I thought they need some very basic consideration.
After having contemplated a while about the ‘springology’, I arrived at the following ideas, perhaps evident to experts since long, perhaps not. The conclusion is that it is necessary to use a preselected matched triplet of springs to achieve the best result. How to do so remains open.
I kept clear of this part of the LP12 according to the ‘mystery’ of a good set up, but with the new plinth there was no other choice than to get into it. The first basic observation is: The springs vary in shape (they are more or less concentric/excentric – certainly an important property) and also in compliance (presumably less important). The degree of excentricity is indeed quite variable. To check for this, an improvised ‘spring selektor’ did a good job:
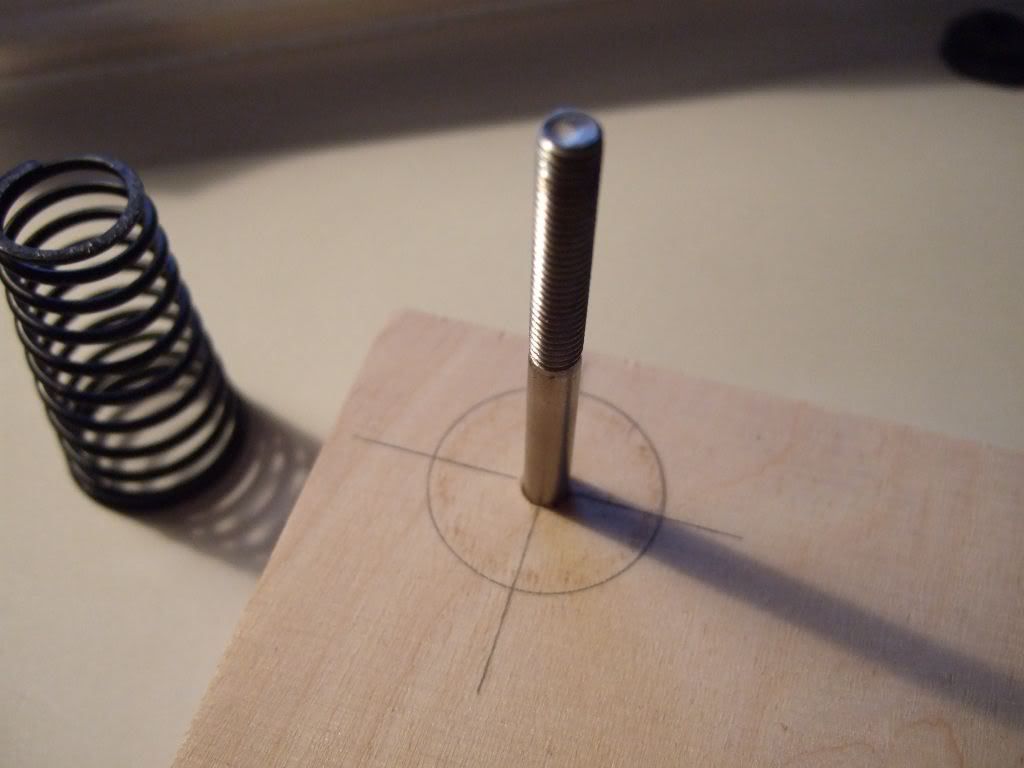
The unloaded springs look typically like this:
1. category ‘good’
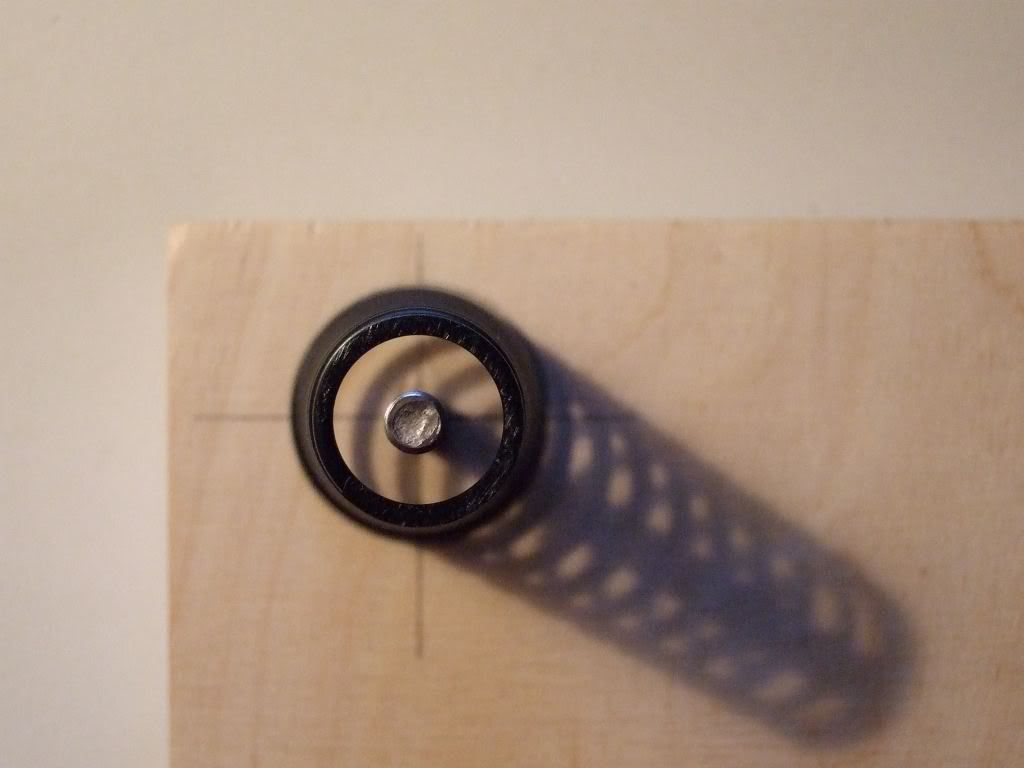
2. category ‘medium’
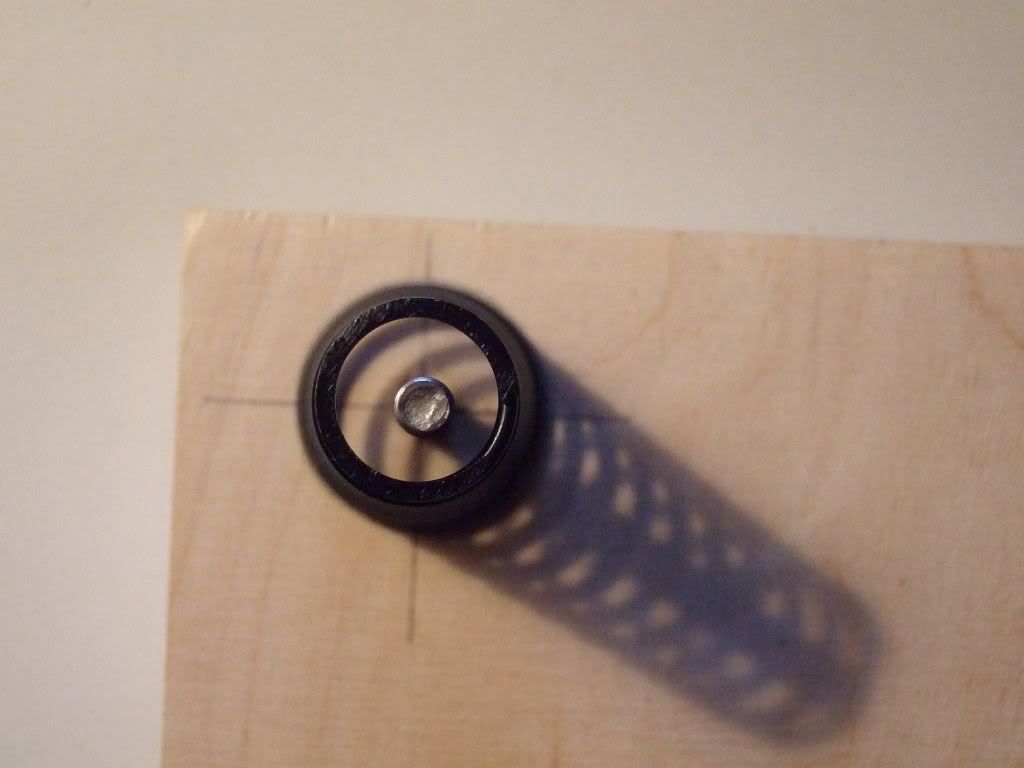
3. category ‘poor’
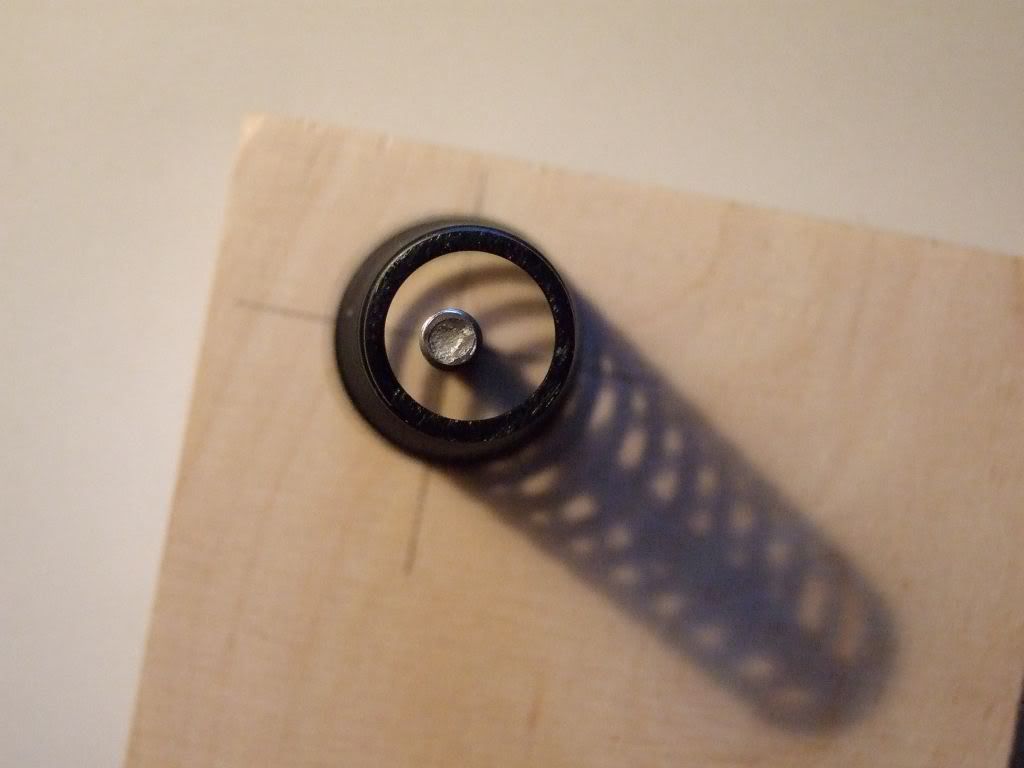
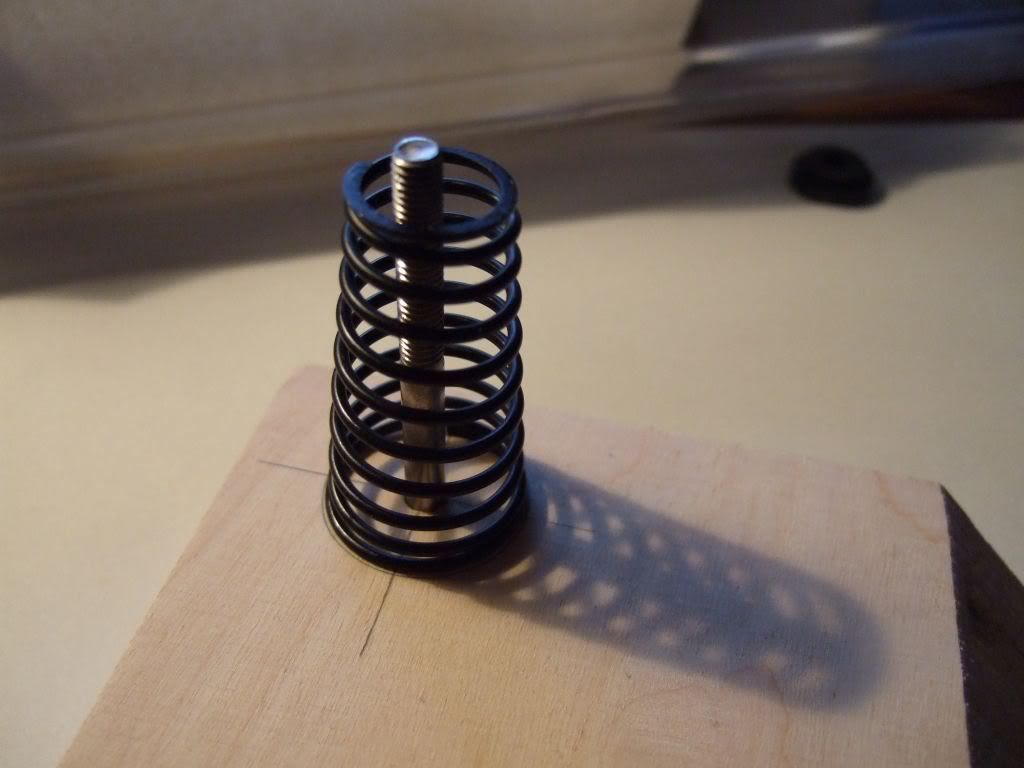
Out of a set of 20 springs, 9 were poor, 5 were good, the rest was medium. (I don’t talk of those that do not have a flat base and can thus rock on the grommet (= 1).) I discarded the 9 classified as poor.
As far as I understand, a main goal of the spring set up is, not to introduce lateral forces into the system. An arbitrary spring triplett is very likely to fail in this respect, as simple geometric considerations show:
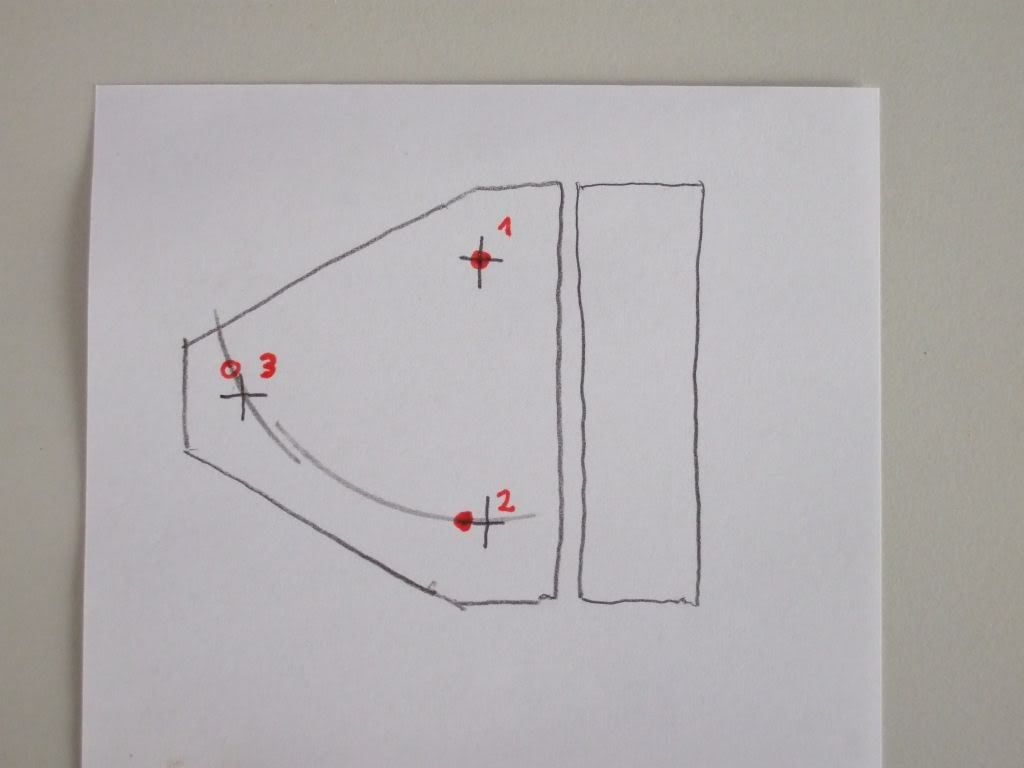
Here, crosses represent the bolt heads (= top plate) and also bolt ‘feet’ (small grommet) when the bolts are aligned well. The red dots indicate the position of the upper spring end, i.e. the centre of the large grommets. The distances between the centres of the subchassis holes which accept the large grommets resemble those of the top plate. If the springs are excentric, as shown in the sketch, a misalignment between subchassis and plinth results (being unimportant as stated many times). But it is important, that after having chosen 2 springs (say number 1 and 2), the excentricity that the third should have is exactly determined. If the spring chosen for position 3 shows a different excentricity, lateral forces cannot be avoided. Perhaps it is possible to compensate for them by bravely turning the springs until a more or less pistonic subchassis movement results – but it is not the optimum.
The simplest solution would obviously be, to take a triplett of the most concentric springs, build it into the deck, and voila – perfect set up in no time. Of course I tried this, and failed. Unluckily, the springs which are concentric when unloaded, might get excentric when loaded. I was surprised to see the armboard moving laterally when screwing the nuts in.
This makes the easily observable property of the not loaded spings kind
of obsolete, perhaps except that might be good to discard the half set marked ‘poor’. The only solution is to observe excentricity of the loaded springs. I could not see any easy method for this…..
I finally chose two from the unloaded ‘medium’ category and used one of the previously ‘good’ ones. If there would be a truly concentric one at point 1 (you see why my geometry sketch looks like it does), the distances from the turning point 1 to point 2 and 3 are proportional to the excentricities (roughly the same, as distances are 18.4 cm and 23.5 cm).
I found it useful to pre-orient the selected springs and to mark them (e.g. at their shortes half axis) to check orientation when turning them. But at the final end was turning springs as everybody else does, too….
Marked spring with a piece of glue paper
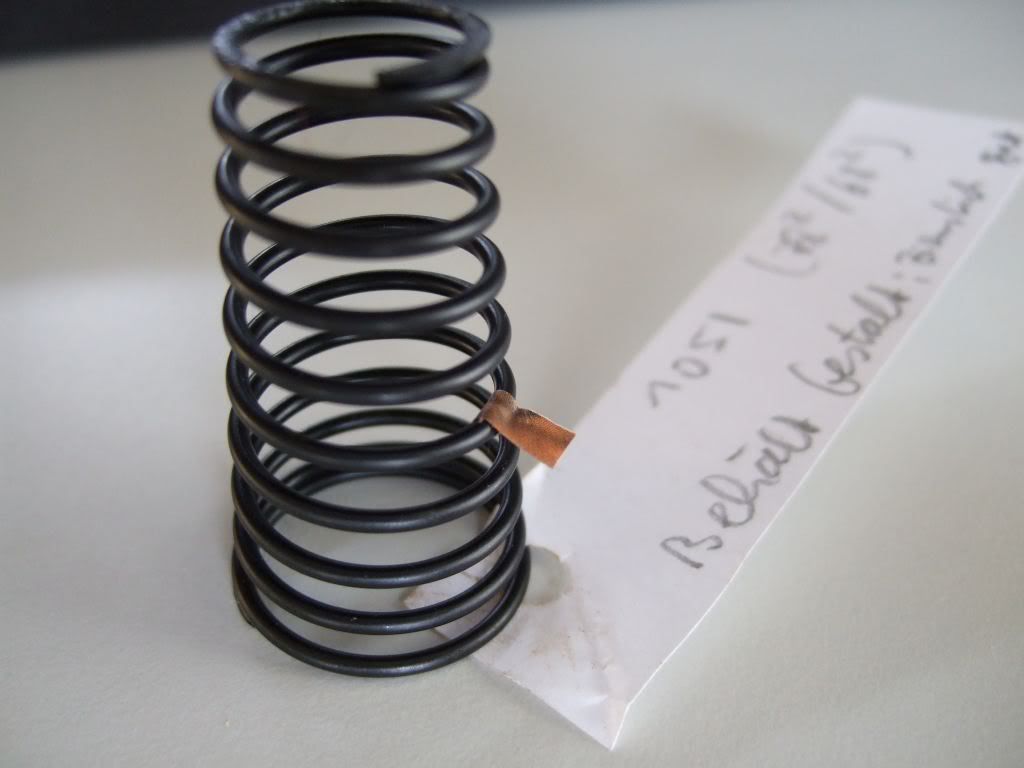
How does compliance vary? Again, a very improvised experiment must suffice (kitchen scale and vertical gauge):
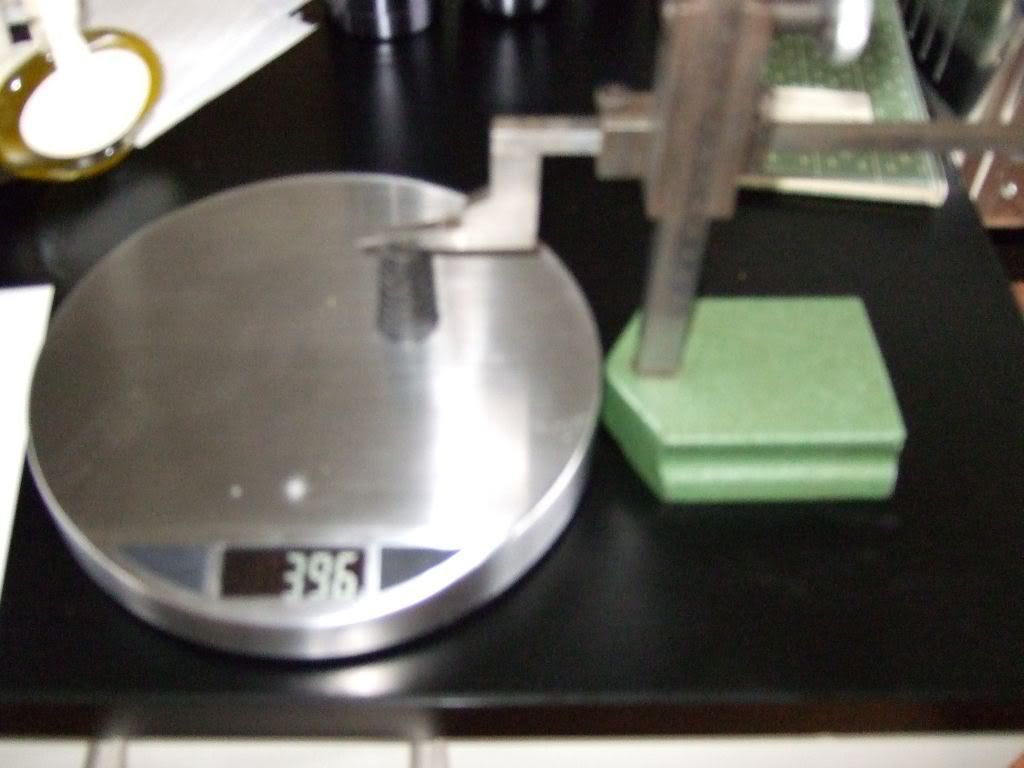
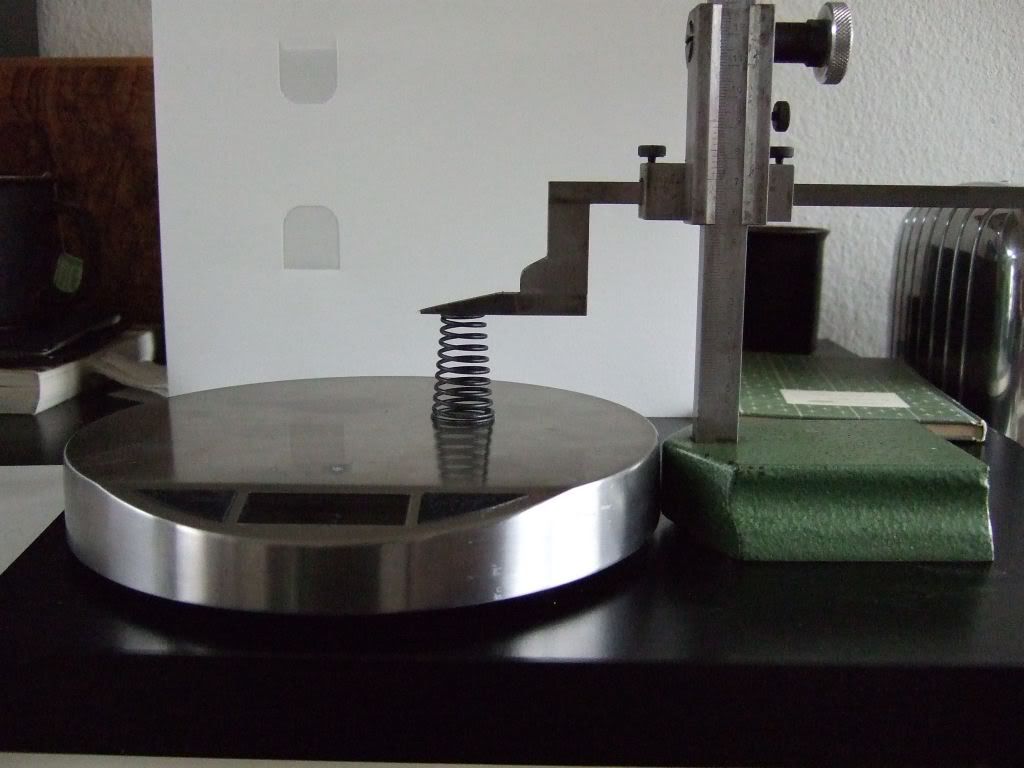
I checked the force resulting from a compression of 10mm. The vertical gauge has a Nonius, but with approx. 1000g/10mm the results are certainly no more precise than 10-20g (please excuse the use of g for force – but isn’t that what the scale shows me???). Results were
1064, 1050, 1067, 1068, 1034, 996, 1049, 1052, 1067, 1036, 1070, 1056, 1049, 1051, 1015, 998, 1001
I did not measure all of the 20, but included also some older ones.
The springs weigh 10g. Unloaded lengths varied very little between 77.8 and 78.3 mm minus the height of the kitchen scale (not determined). I don’t think this variability is of any adverse consequence.
Finally, a short consideration about their coating. The springs were quite greasy out of the bag. I think, the grease will not only become increasingly solid and sticky with time, but will presumably also degrade the grommet material. Consequently I washed them thoroughly in a hot soap solution (let them suck for some time! – even the fresh grease is very sticky – but not too long, i.e. more than half an hour, as rust is developing quickly) and wiped them out with alcohol where they touch the grommets.
Rust developing while soaking the springs for too long
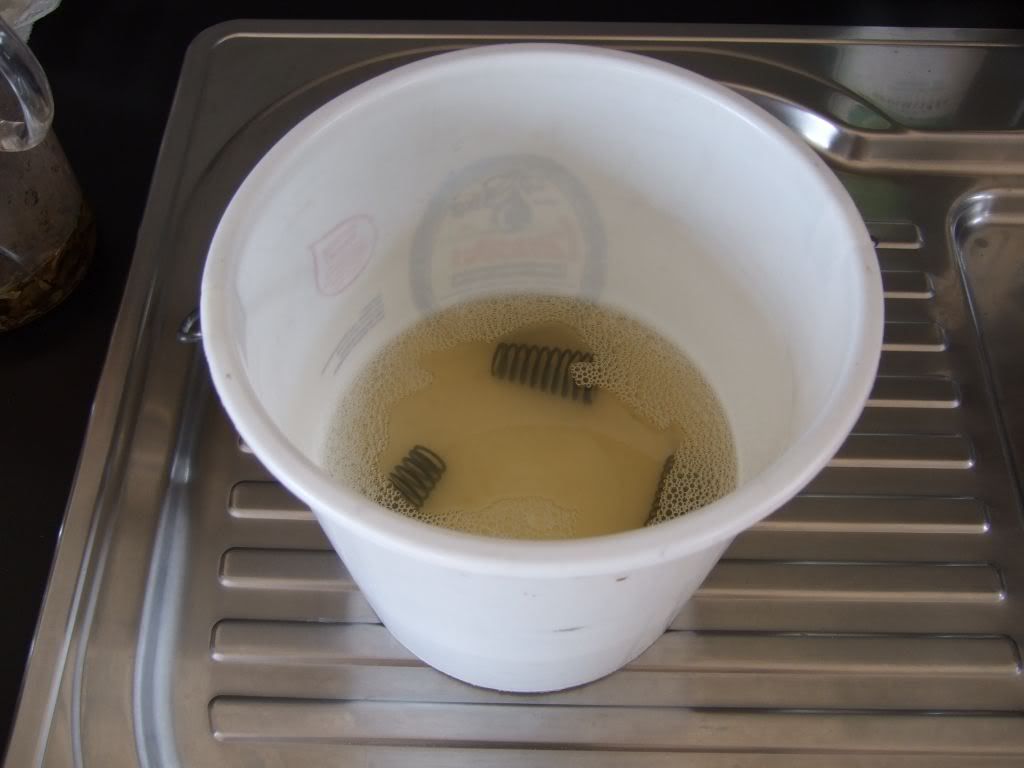
Needless to say, after the consideration above, my armboard is not well aligned to the plinth. The question is, who cares? It seems much more urgent to find a method to select springs from their compressed state and to determine the amount of their excentricity in order to arrive at ‘voila -perfect setup in no time’.
After having contemplated a while about the ‘springology’, I arrived at the following ideas, perhaps evident to experts since long, perhaps not. The conclusion is that it is necessary to use a preselected matched triplet of springs to achieve the best result. How to do so remains open.
I kept clear of this part of the LP12 according to the ‘mystery’ of a good set up, but with the new plinth there was no other choice than to get into it. The first basic observation is: The springs vary in shape (they are more or less concentric/excentric – certainly an important property) and also in compliance (presumably less important). The degree of excentricity is indeed quite variable. To check for this, an improvised ‘spring selektor’ did a good job:
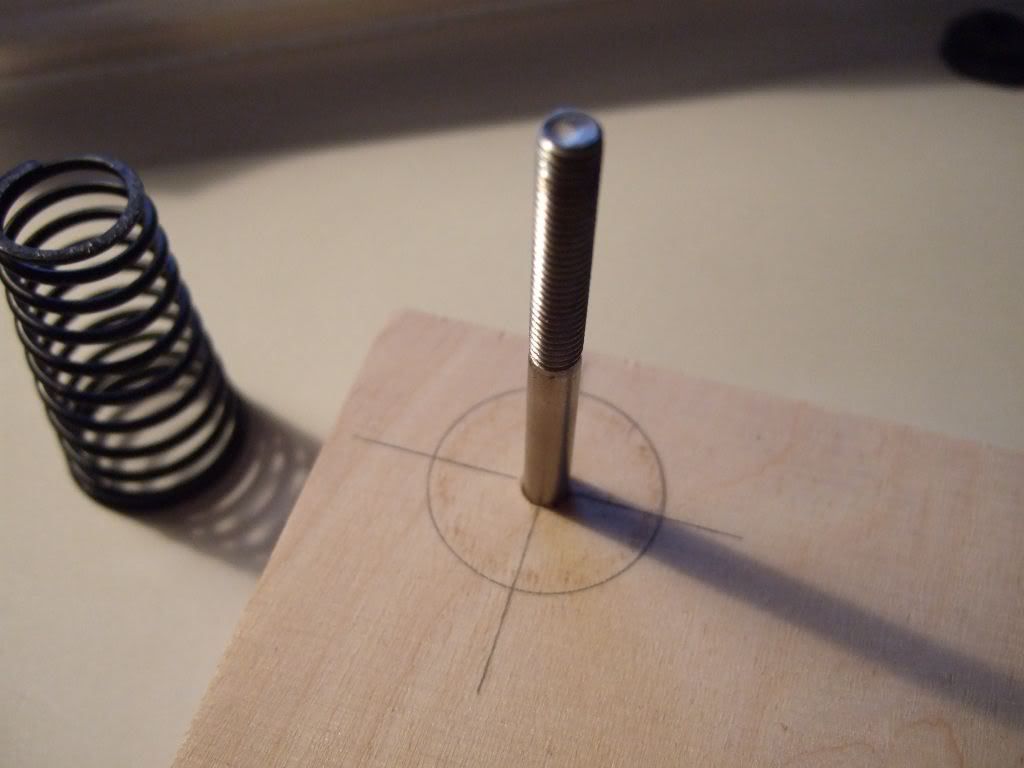
The unloaded springs look typically like this:
1. category ‘good’
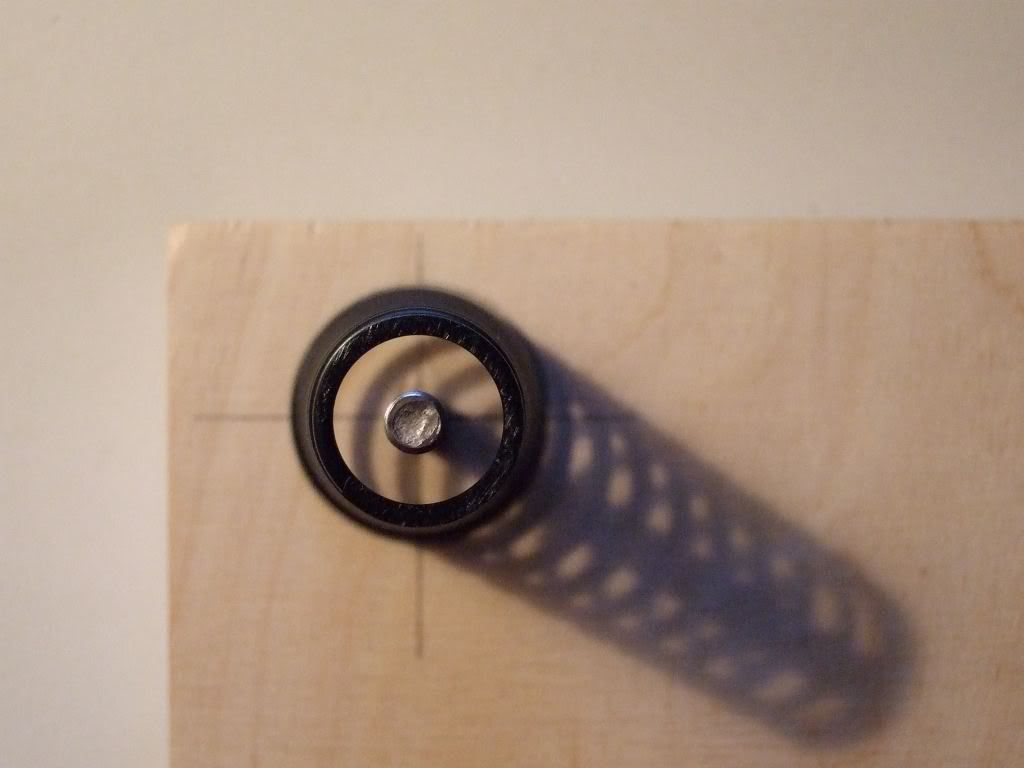
2. category ‘medium’
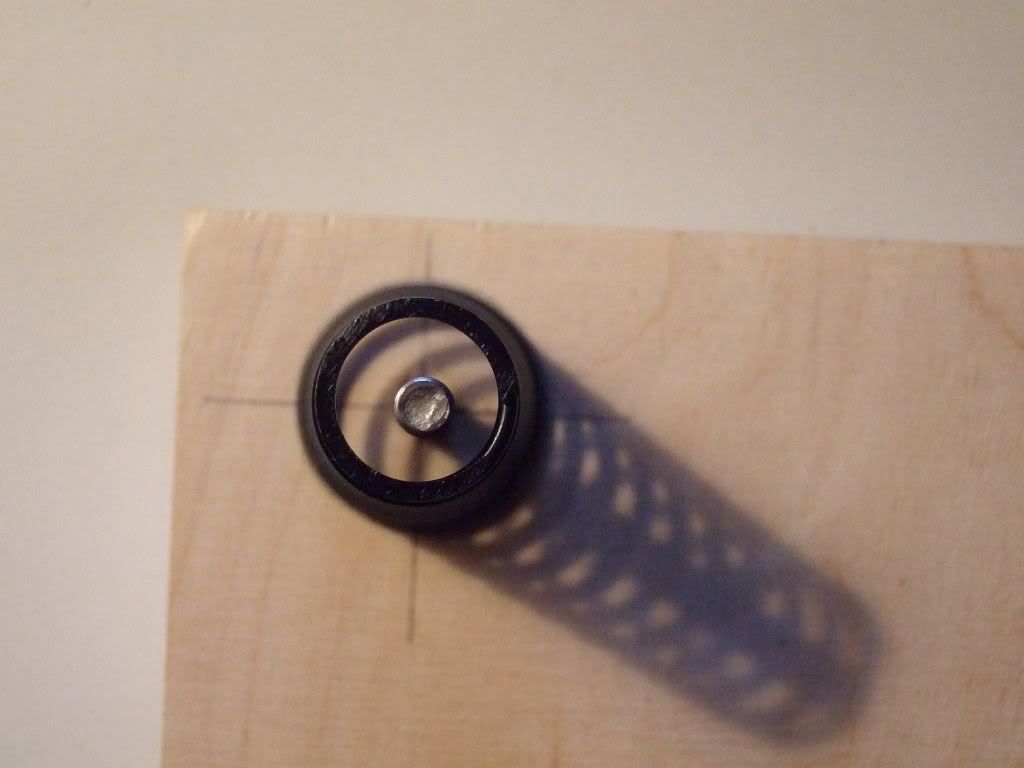
3. category ‘poor’
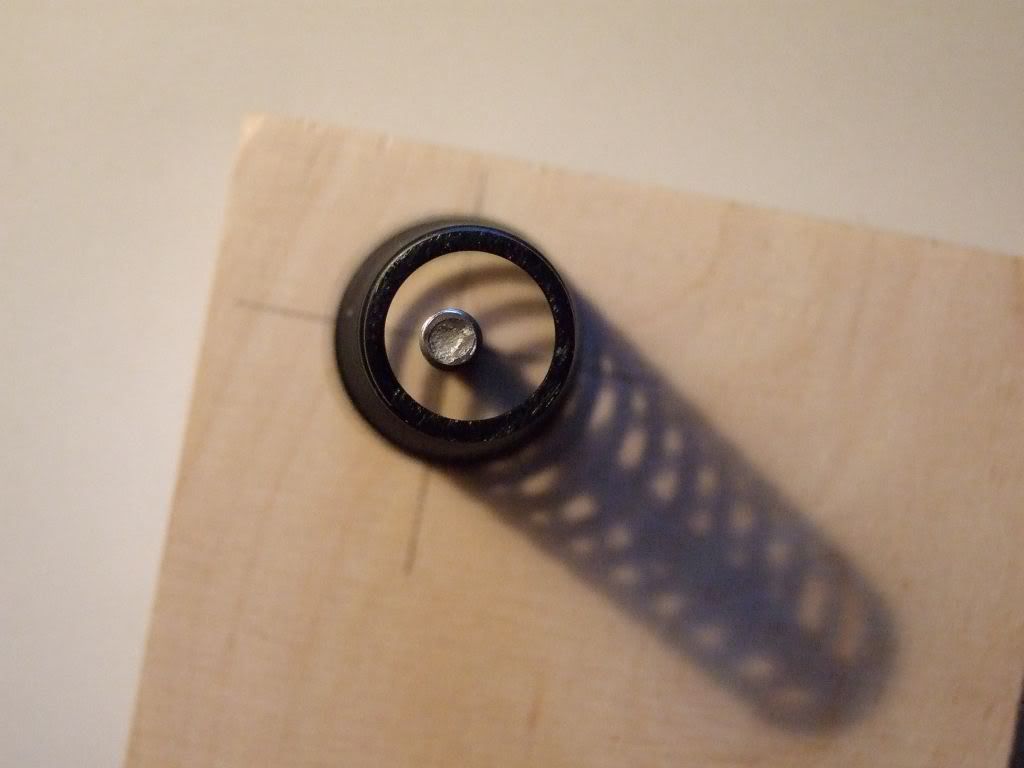
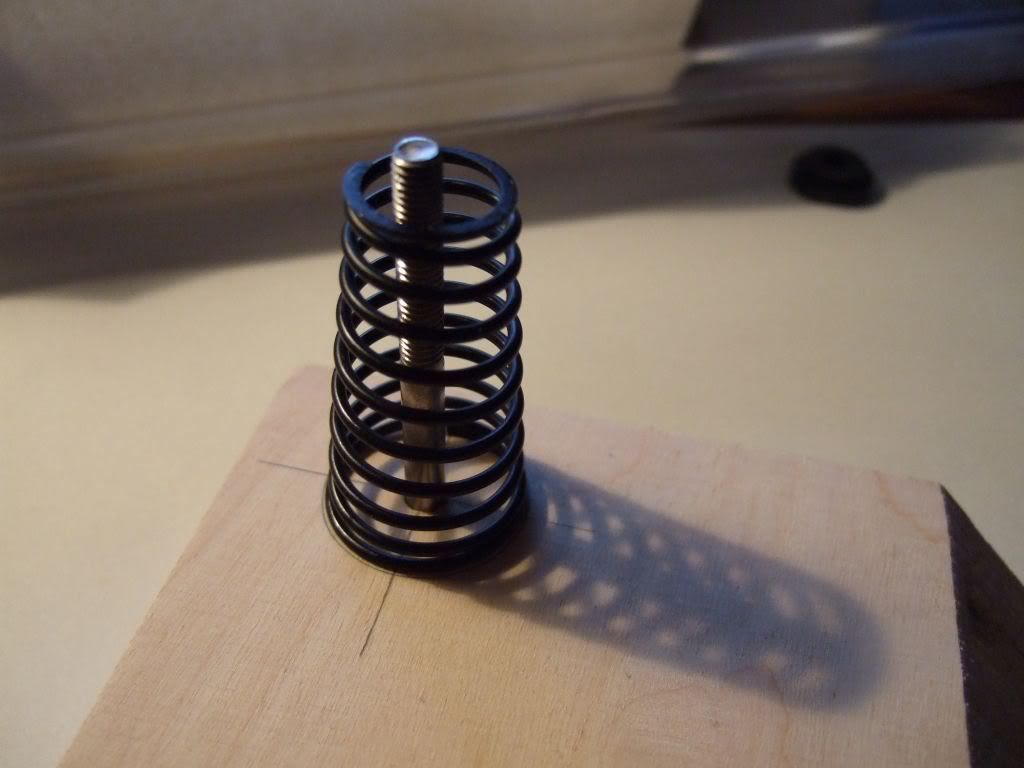
Out of a set of 20 springs, 9 were poor, 5 were good, the rest was medium. (I don’t talk of those that do not have a flat base and can thus rock on the grommet (= 1).) I discarded the 9 classified as poor.
As far as I understand, a main goal of the spring set up is, not to introduce lateral forces into the system. An arbitrary spring triplett is very likely to fail in this respect, as simple geometric considerations show:
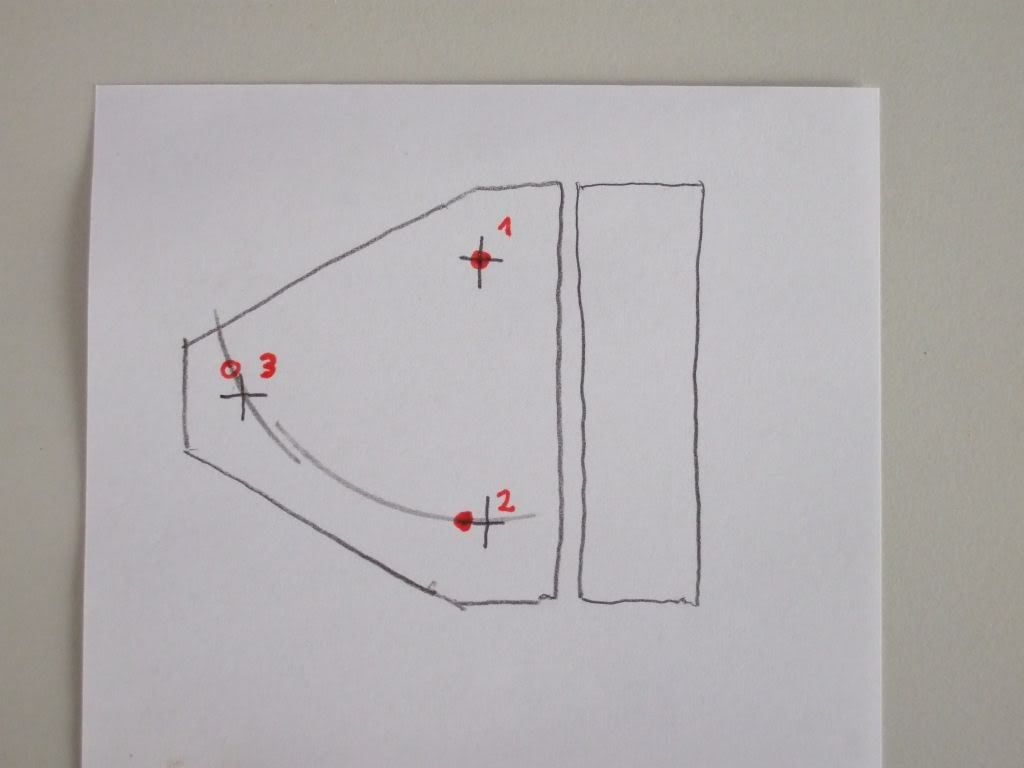
Here, crosses represent the bolt heads (= top plate) and also bolt ‘feet’ (small grommet) when the bolts are aligned well. The red dots indicate the position of the upper spring end, i.e. the centre of the large grommets. The distances between the centres of the subchassis holes which accept the large grommets resemble those of the top plate. If the springs are excentric, as shown in the sketch, a misalignment between subchassis and plinth results (being unimportant as stated many times). But it is important, that after having chosen 2 springs (say number 1 and 2), the excentricity that the third should have is exactly determined. If the spring chosen for position 3 shows a different excentricity, lateral forces cannot be avoided. Perhaps it is possible to compensate for them by bravely turning the springs until a more or less pistonic subchassis movement results – but it is not the optimum.
The simplest solution would obviously be, to take a triplett of the most concentric springs, build it into the deck, and voila – perfect set up in no time. Of course I tried this, and failed. Unluckily, the springs which are concentric when unloaded, might get excentric when loaded. I was surprised to see the armboard moving laterally when screwing the nuts in.
This makes the easily observable property of the not loaded spings kind
of obsolete, perhaps except that might be good to discard the half set marked ‘poor’. The only solution is to observe excentricity of the loaded springs. I could not see any easy method for this…..
I finally chose two from the unloaded ‘medium’ category and used one of the previously ‘good’ ones. If there would be a truly concentric one at point 1 (you see why my geometry sketch looks like it does), the distances from the turning point 1 to point 2 and 3 are proportional to the excentricities (roughly the same, as distances are 18.4 cm and 23.5 cm).
I found it useful to pre-orient the selected springs and to mark them (e.g. at their shortes half axis) to check orientation when turning them. But at the final end was turning springs as everybody else does, too….
Marked spring with a piece of glue paper
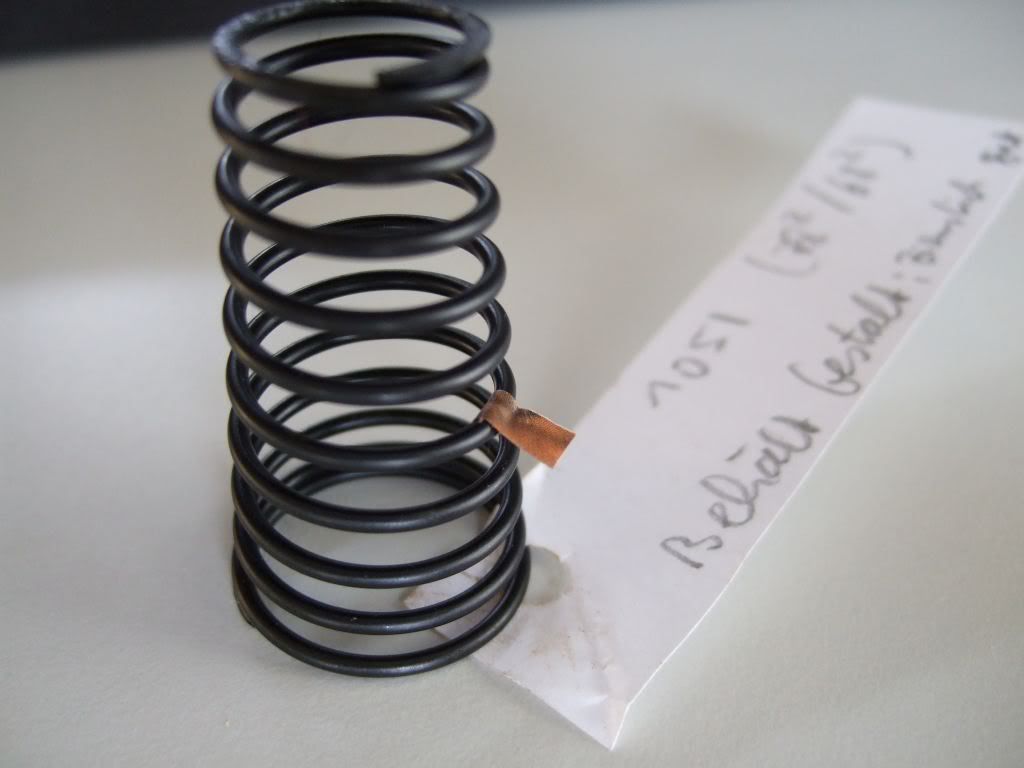
How does compliance vary? Again, a very improvised experiment must suffice (kitchen scale and vertical gauge):
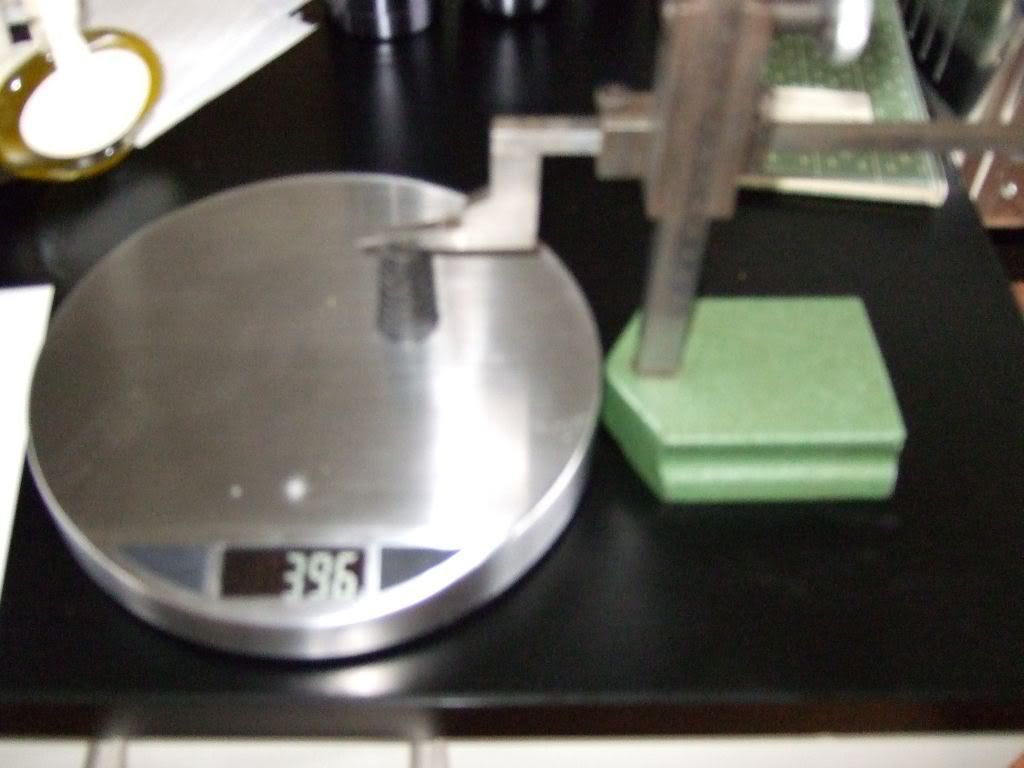
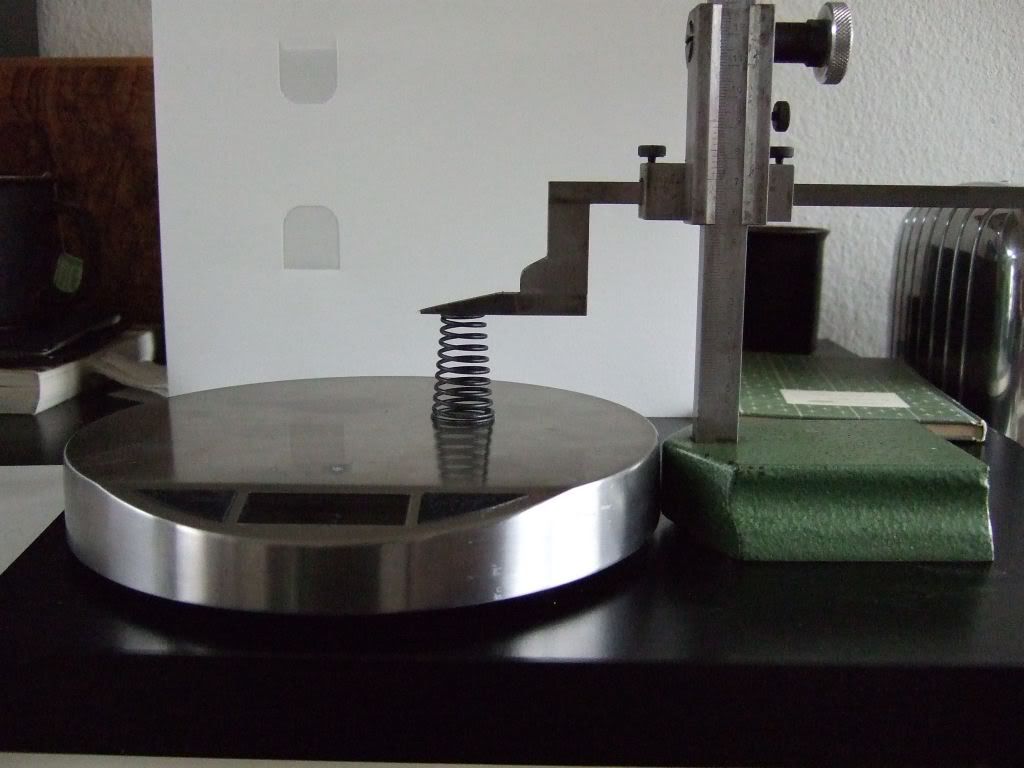
I checked the force resulting from a compression of 10mm. The vertical gauge has a Nonius, but with approx. 1000g/10mm the results are certainly no more precise than 10-20g (please excuse the use of g for force – but isn’t that what the scale shows me???). Results were
1064, 1050, 1067, 1068, 1034, 996, 1049, 1052, 1067, 1036, 1070, 1056, 1049, 1051, 1015, 998, 1001
I did not measure all of the 20, but included also some older ones.
The springs weigh 10g. Unloaded lengths varied very little between 77.8 and 78.3 mm minus the height of the kitchen scale (not determined). I don’t think this variability is of any adverse consequence.
Finally, a short consideration about their coating. The springs were quite greasy out of the bag. I think, the grease will not only become increasingly solid and sticky with time, but will presumably also degrade the grommet material. Consequently I washed them thoroughly in a hot soap solution (let them suck for some time! – even the fresh grease is very sticky – but not too long, i.e. more than half an hour, as rust is developing quickly) and wiped them out with alcohol where they touch the grommets.
Rust developing while soaking the springs for too long
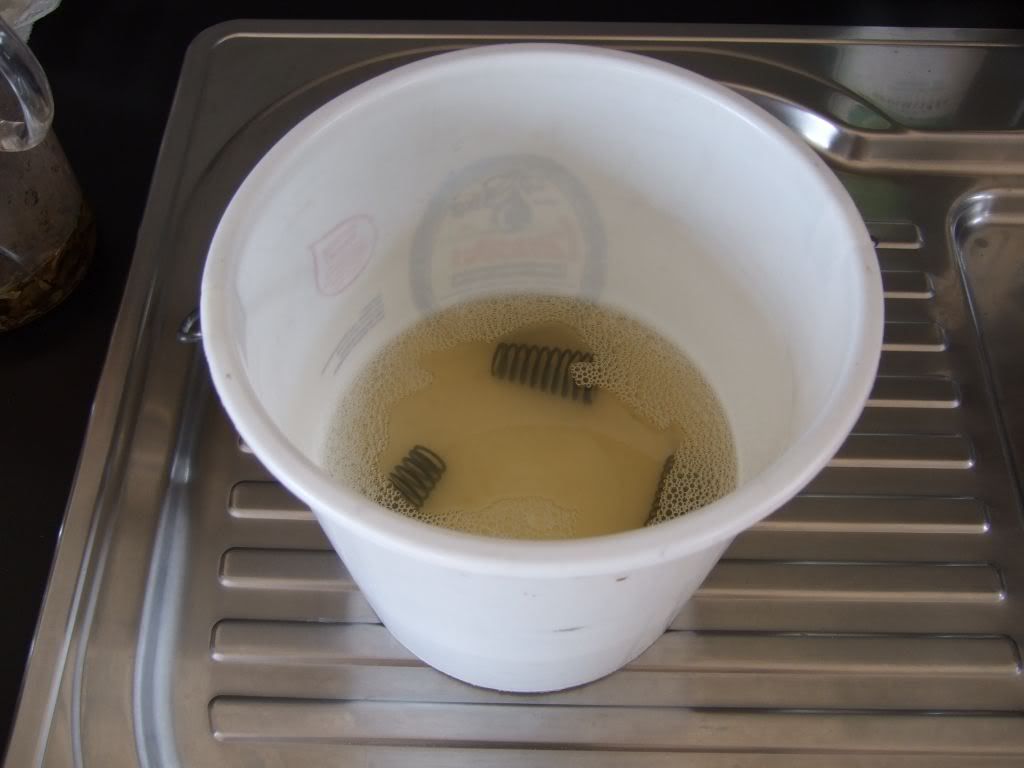
Needless to say, after the consideration above, my armboard is not well aligned to the plinth. The question is, who cares? It seems much more urgent to find a method to select springs from their compressed state and to determine the amount of their excentricity in order to arrive at ‘voila -perfect setup in no time’.
Very interesting experiments there, Klaus. Sorry to hear that you didn't find the magic (I actually had to think about how to spell that - I've been selling Linn stuff too long :) ) method to find ideal springs - although it obviously isn't for lack of trying. What complicates your investigations further is that each spring receives a different load inside the LP12 so the question is how linear is the behavior of the spring with the amount of compression it will receive in the position on the subchassis where it is placed? One could certainly go crazy trying to optimize all the possible variables! I wonder how much it would cost for Linn to have perfect springs made and if we will ever see that day? Certainly the most recent springs do tend to work better as a whole than those in the past have.
There is another variable you can check visually that is likely to have a bearing on this as well. I have found that when the springs are set on a table with the small side up the top surface is not level on all the springs - some are at a very noticeable angle. This would also tend to throw the forces off just like not being concentric, although once again the question of how correct they are under load rears its ugly head.
Anyway, good luck and keep up the good work.
There is another variable you can check visually that is likely to have a bearing on this as well. I have found that when the springs are set on a table with the small side up the top surface is not level on all the springs - some are at a very noticeable angle. This would also tend to throw the forces off just like not being concentric, although once again the question of how correct they are under load rears its ugly head.
Anyway, good luck and keep up the good work.
Just to confirm: springs were of the latest production.
Th, your comment about linearity issues brought the idea to me, that
what most do almost automatically (including myself, of course) might
be wrong: namely to put the strongest spring to position 1 (next to
tonearm). Compressing the spring introduces a tendency to more
stiffness (higher g/cm (or lower cm/g)), so in order to arrive at
similar values at all three springs, one should use the _softest_ spring
there. Hmm????
Th, your comment about linearity issues brought the idea to me, that
what most do almost automatically (including myself, of course) might
be wrong: namely to put the strongest spring to position 1 (next to
tonearm). Compressing the spring introduces a tendency to more
stiffness (higher g/cm (or lower cm/g)), so in order to arrive at
similar values at all three springs, one should use the _softest_ spring
there. Hmm????
Progress report:
I exchanged the springs and built in the best I coud find in my set.
The compressed springs can be examined by taking the centre bolt OFF the spring selektor. If the plank is thick enough (about 1 inch or more), it is easy enough to centre one’s eye without the bolt. Marks are now added at 5 mm and 7 mm from the centre point. The pic shows the best spring I found. The acrylic used is to compress the spring.
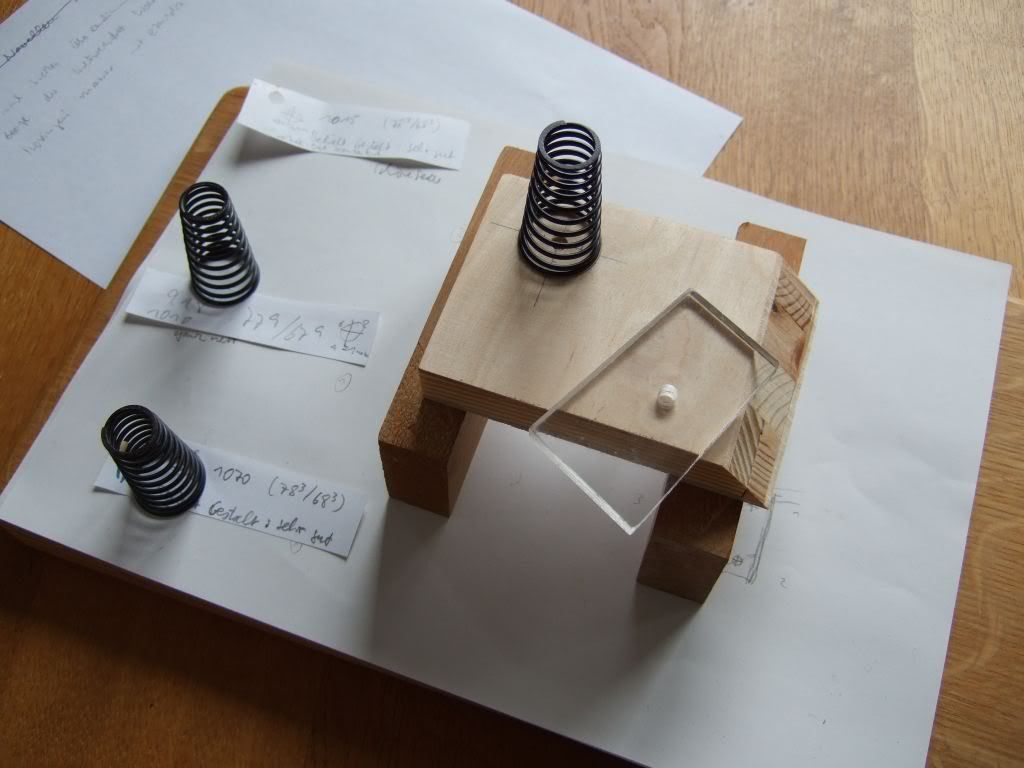
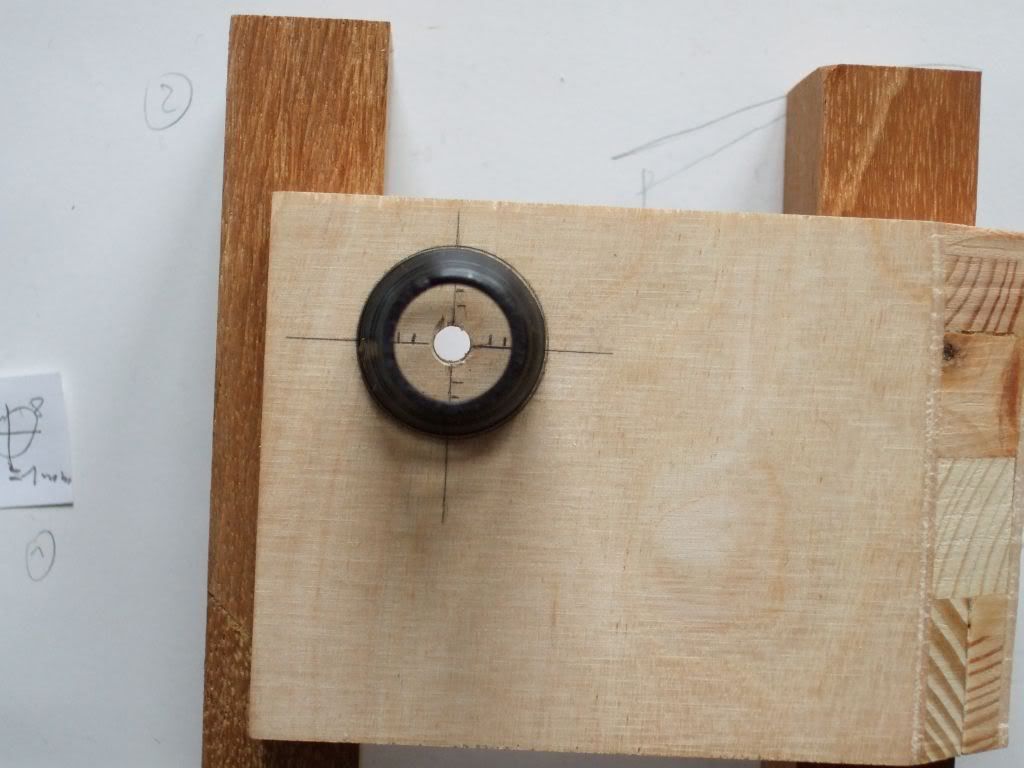
I can’t make a pic and hold the compressed spring simultaneously, sorry. If you compress them completely, there is little play due to sideward forces you may apply, so you get a good estimate. According to my previous idea, I installed the softest spring at the tonearm position. Smallest radius is marked now by a golden Edding line instead of paper bits.
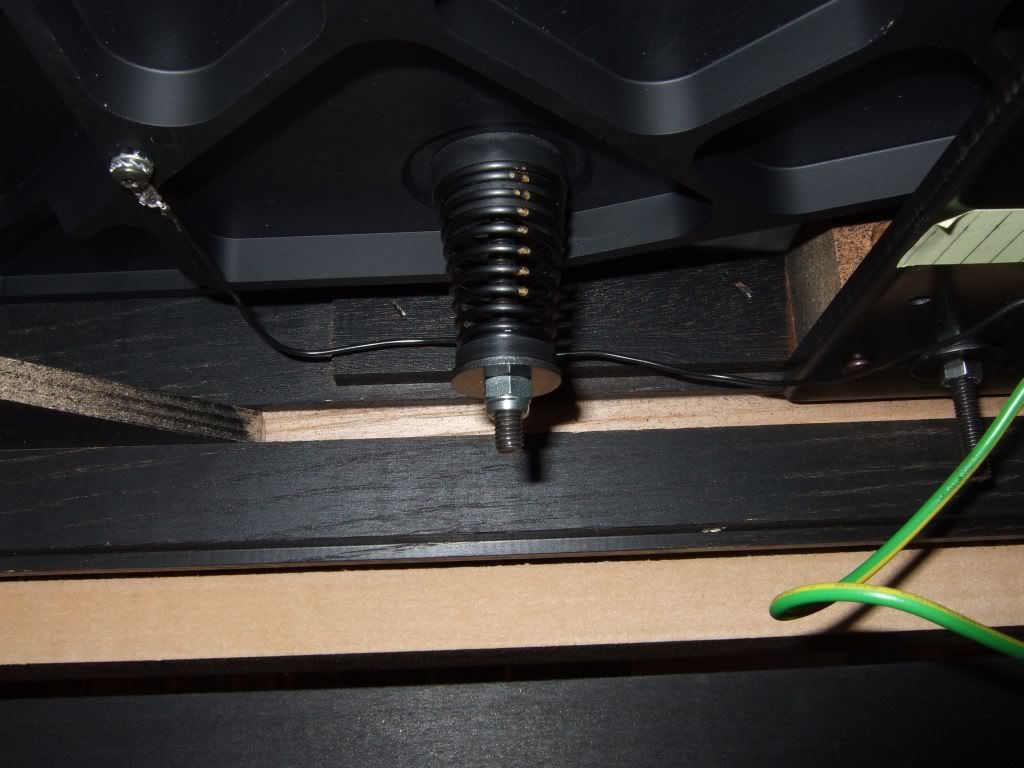
Springs at pos. 1 and 3 are about 1 mm off-centre (compressed), pos. 2 is almost concentric. Right part of the sketch is how installation was planned, left part is the outcome (indicators show the shortest radius’ position, so the subchassis moves in the opposite direction). It is clear that the tonearm board is moved to the right a bit.
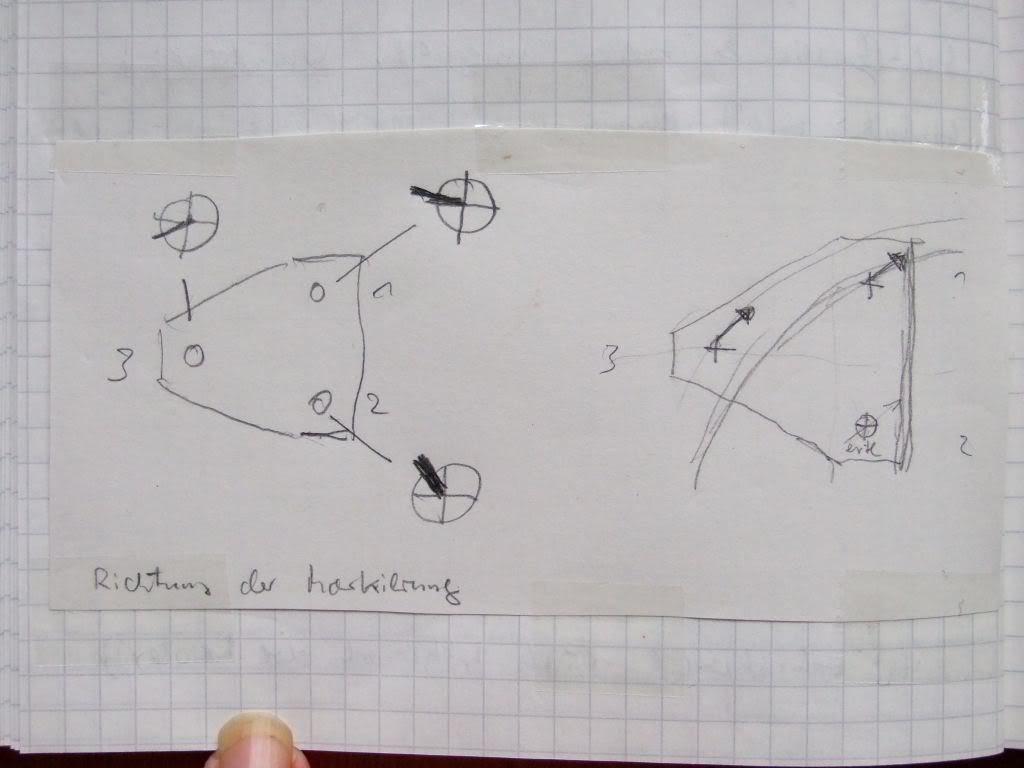
The pre-orientation of spring 1 and 3 ensures that they do not work against each other. With their similar excentricity lateral forces are minimized. Final adjustment is nevertheless done by rotating the spring/grommet assembly. The sound is now as delicate as not before.
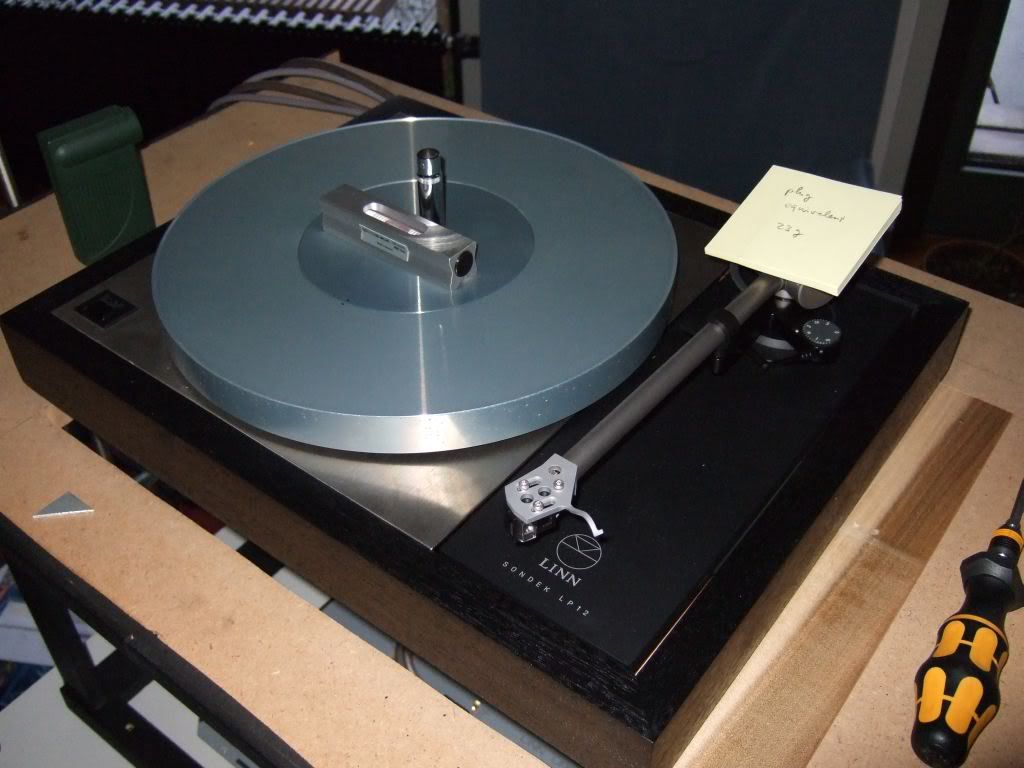
Spring adjustment and levelling of subchassis/inner platter
But overall, I’m left kind of speechless what kind of mediocre stuff is built into this multi-thousand-Dollar-deck by Linn. I’m in favor to put the money to where it really counts, so it is OK to finish the bearings etc. to the highest possible standards. But these springs are also at the heart of the deck and determine the musical result to a considerable extent, too. To rely simply on the installer is not such a good idea imho, and as mentioned, if two springs are chosen, the third must fit exactly geometrically to get the optimum set up.
I exchanged the springs and built in the best I coud find in my set.
The compressed springs can be examined by taking the centre bolt OFF the spring selektor. If the plank is thick enough (about 1 inch or more), it is easy enough to centre one’s eye without the bolt. Marks are now added at 5 mm and 7 mm from the centre point. The pic shows the best spring I found. The acrylic used is to compress the spring.
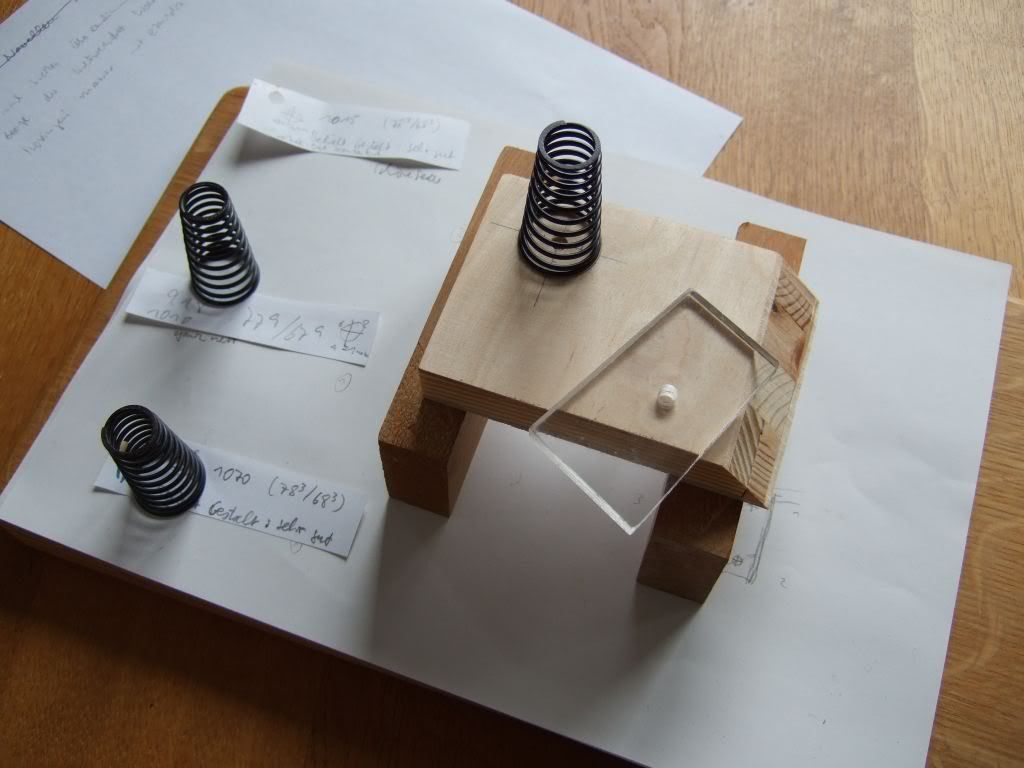
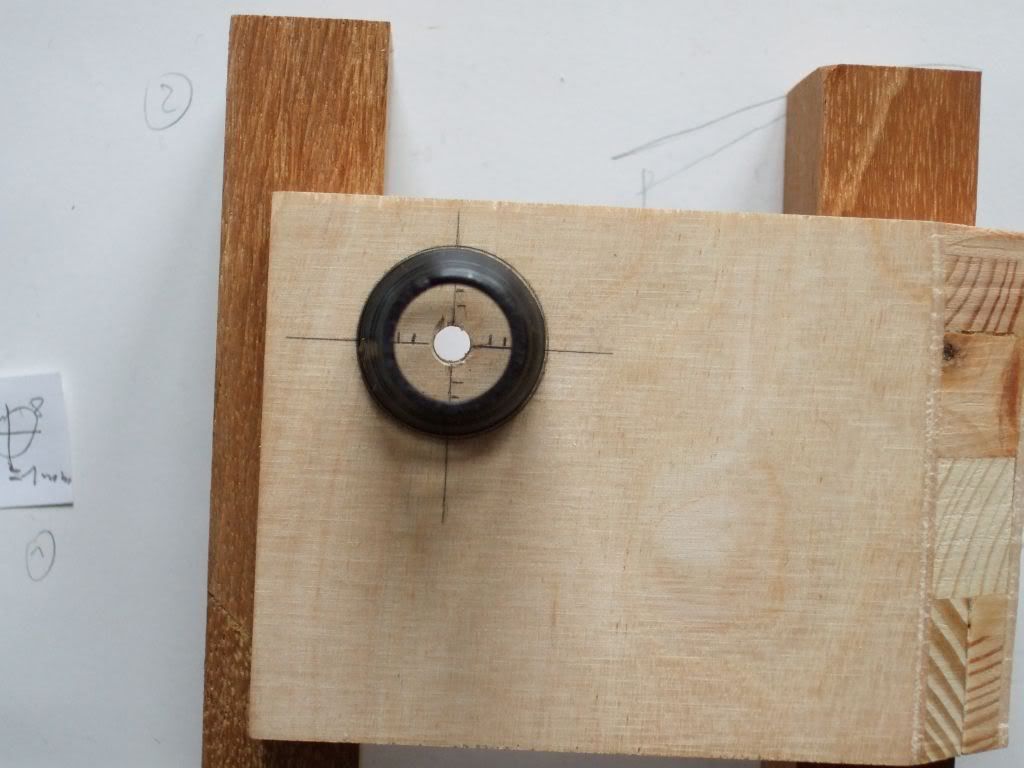
I can’t make a pic and hold the compressed spring simultaneously, sorry. If you compress them completely, there is little play due to sideward forces you may apply, so you get a good estimate. According to my previous idea, I installed the softest spring at the tonearm position. Smallest radius is marked now by a golden Edding line instead of paper bits.
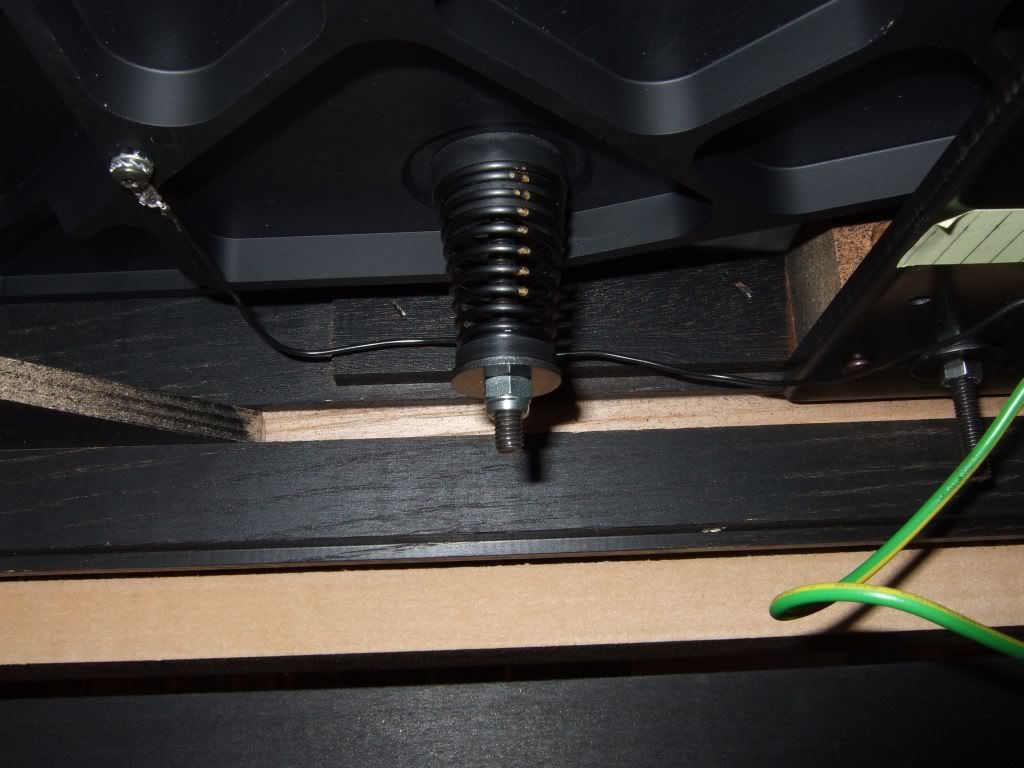
Springs at pos. 1 and 3 are about 1 mm off-centre (compressed), pos. 2 is almost concentric. Right part of the sketch is how installation was planned, left part is the outcome (indicators show the shortest radius’ position, so the subchassis moves in the opposite direction). It is clear that the tonearm board is moved to the right a bit.
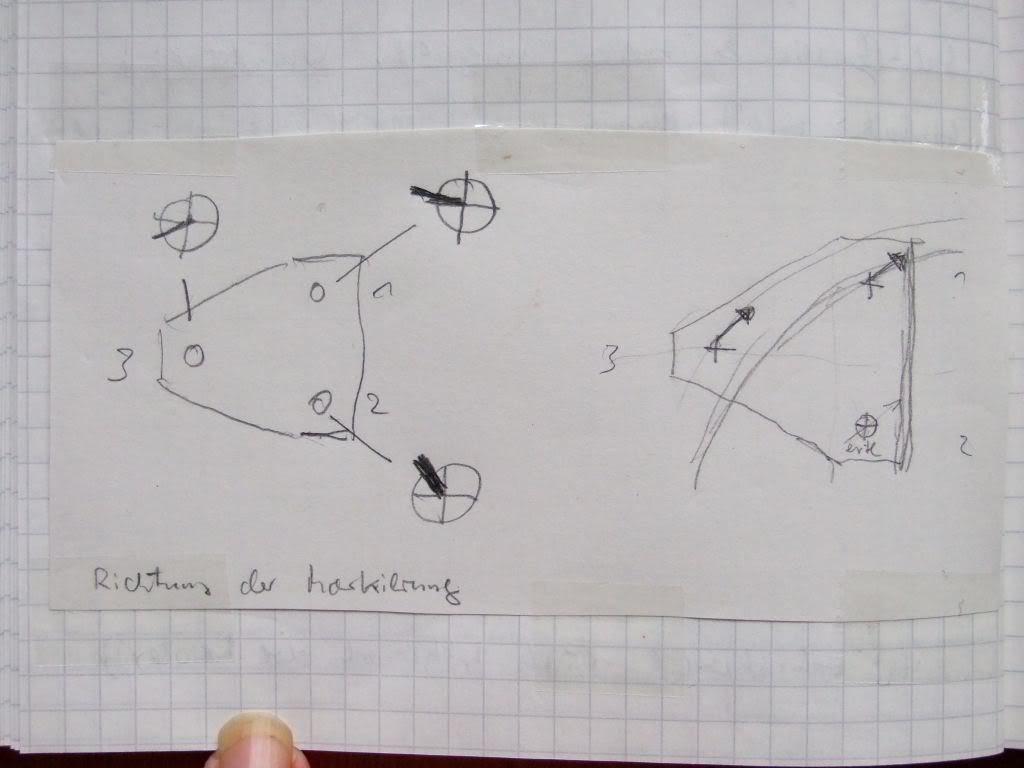
The pre-orientation of spring 1 and 3 ensures that they do not work against each other. With their similar excentricity lateral forces are minimized. Final adjustment is nevertheless done by rotating the spring/grommet assembly. The sound is now as delicate as not before.
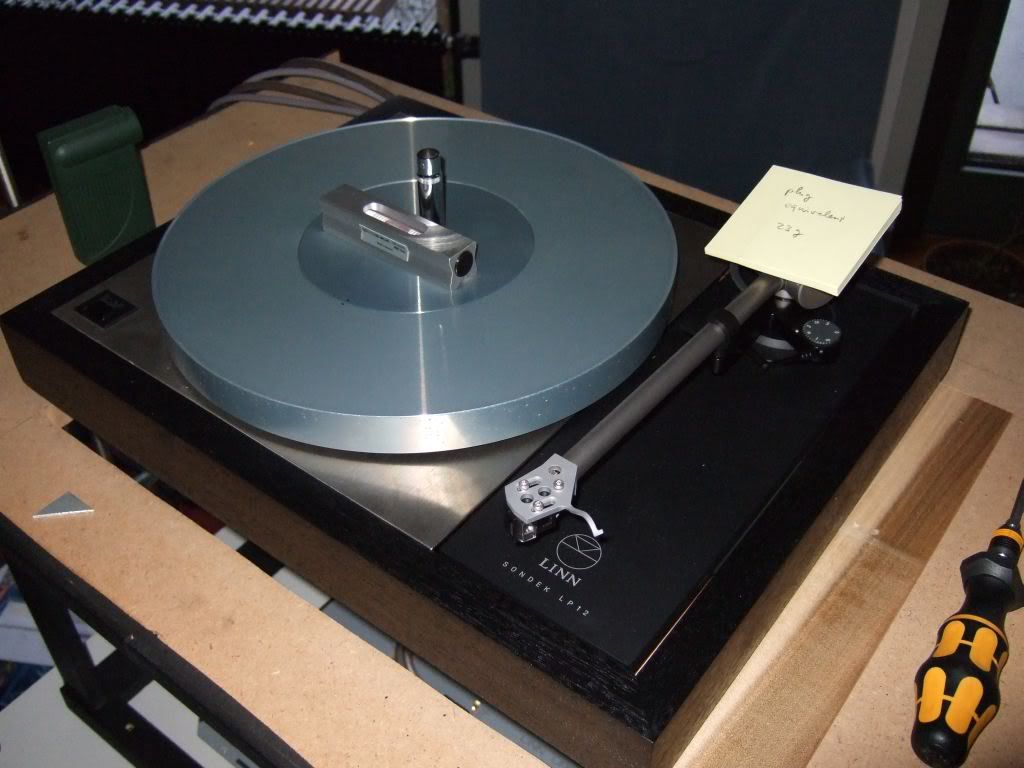
Spring adjustment and levelling of subchassis/inner platter
But overall, I’m left kind of speechless what kind of mediocre stuff is built into this multi-thousand-Dollar-deck by Linn. I’m in favor to put the money to where it really counts, so it is OK to finish the bearings etc. to the highest possible standards. But these springs are also at the heart of the deck and determine the musical result to a considerable extent, too. To rely simply on the installer is not such a good idea imho, and as mentioned, if two springs are chosen, the third must fit exactly geometrically to get the optimum set up.
- Tony Tune-age
- Very active member
- Posts: 1589
- Joined: 2009-12-19 19:07
- Location: United States
Sorry, sorry, but I was not able to leave the springs topic as it was. This time
it is springs forced downward by 1500 g:
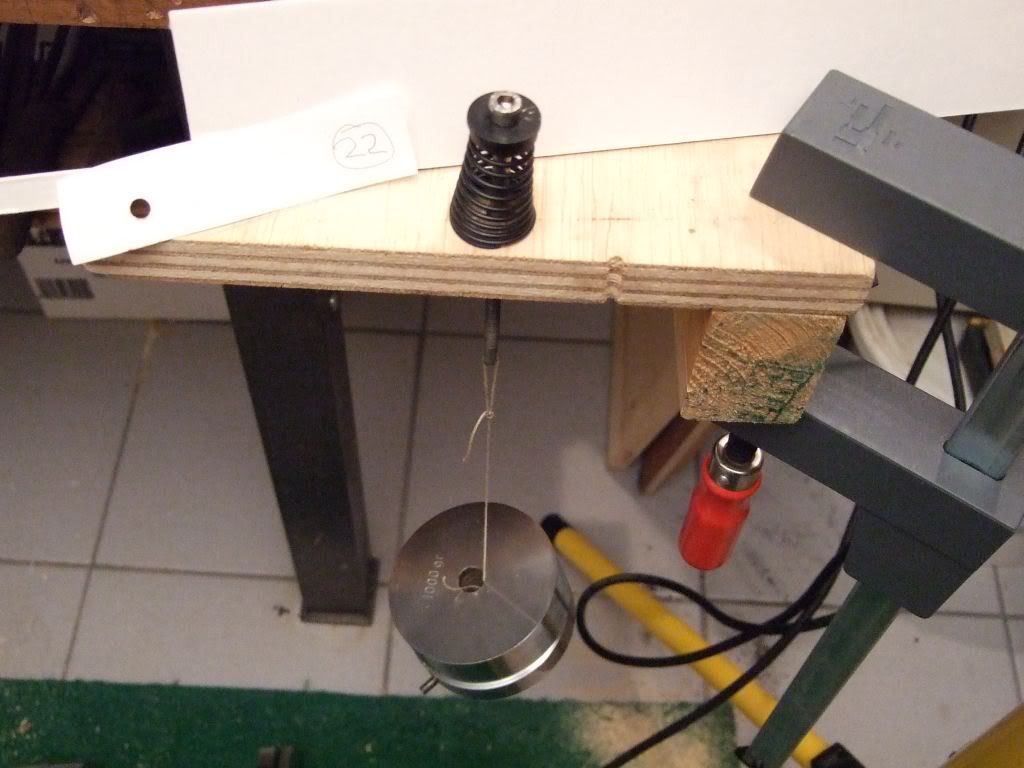
22 have been checked:
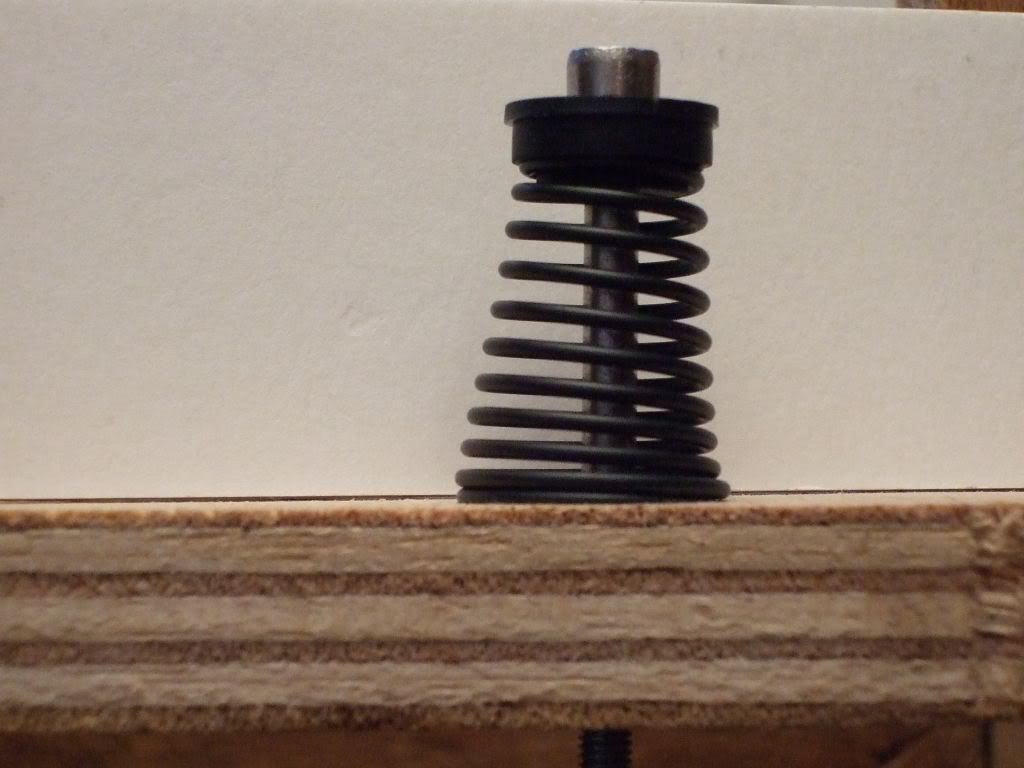
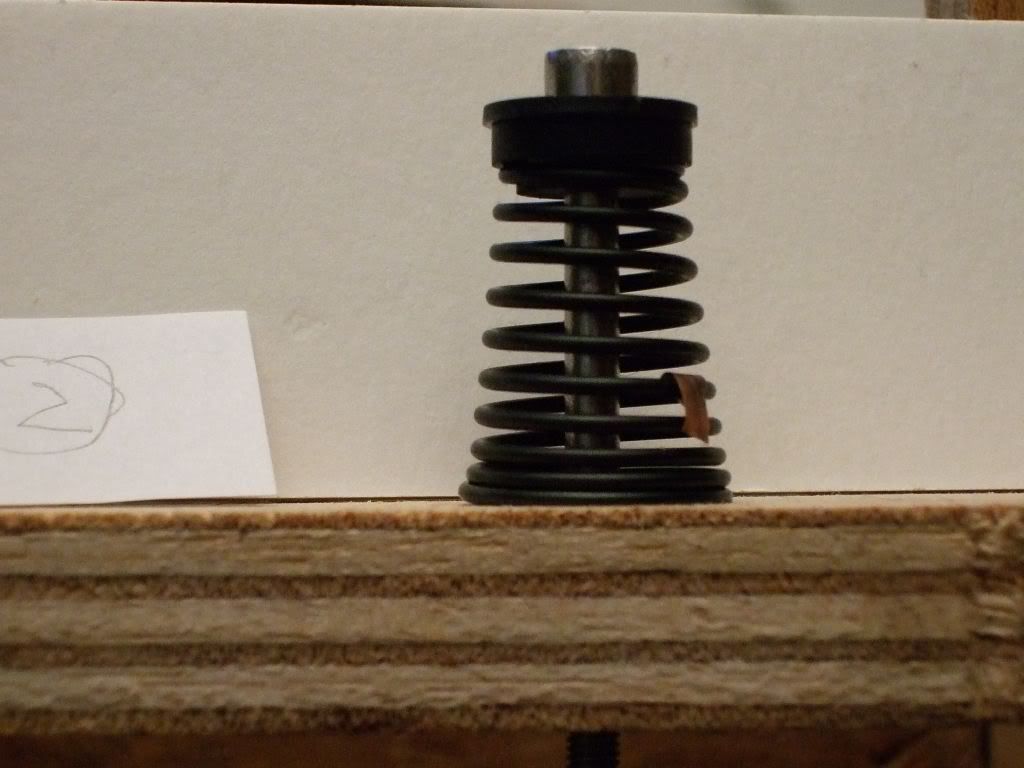
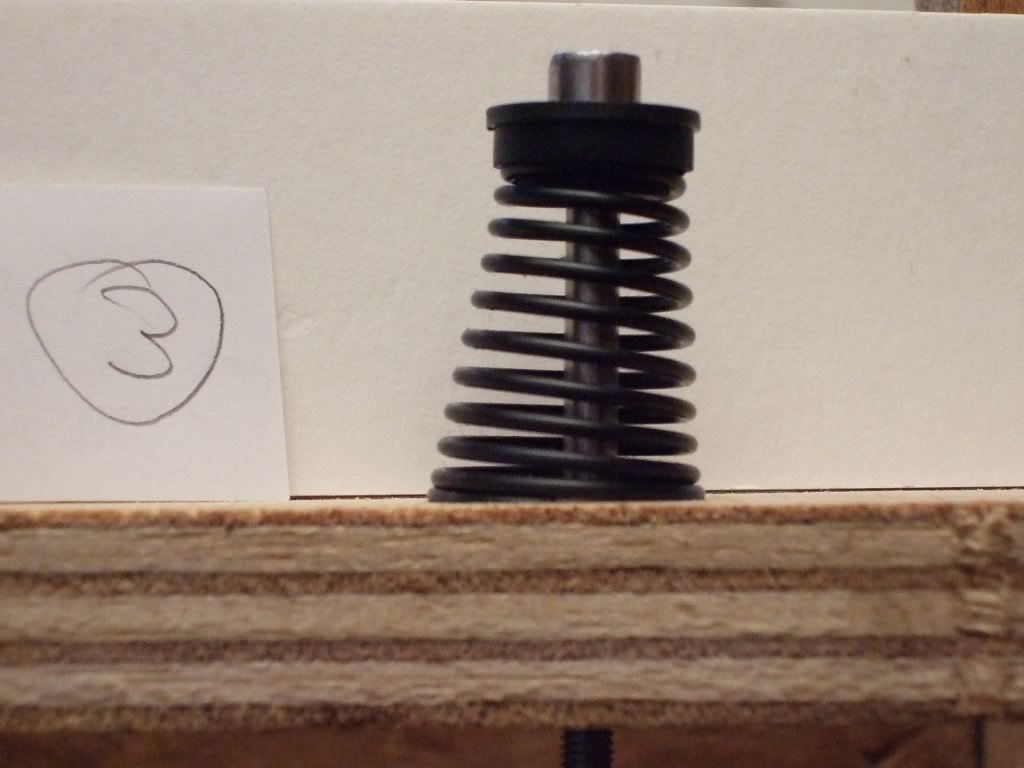
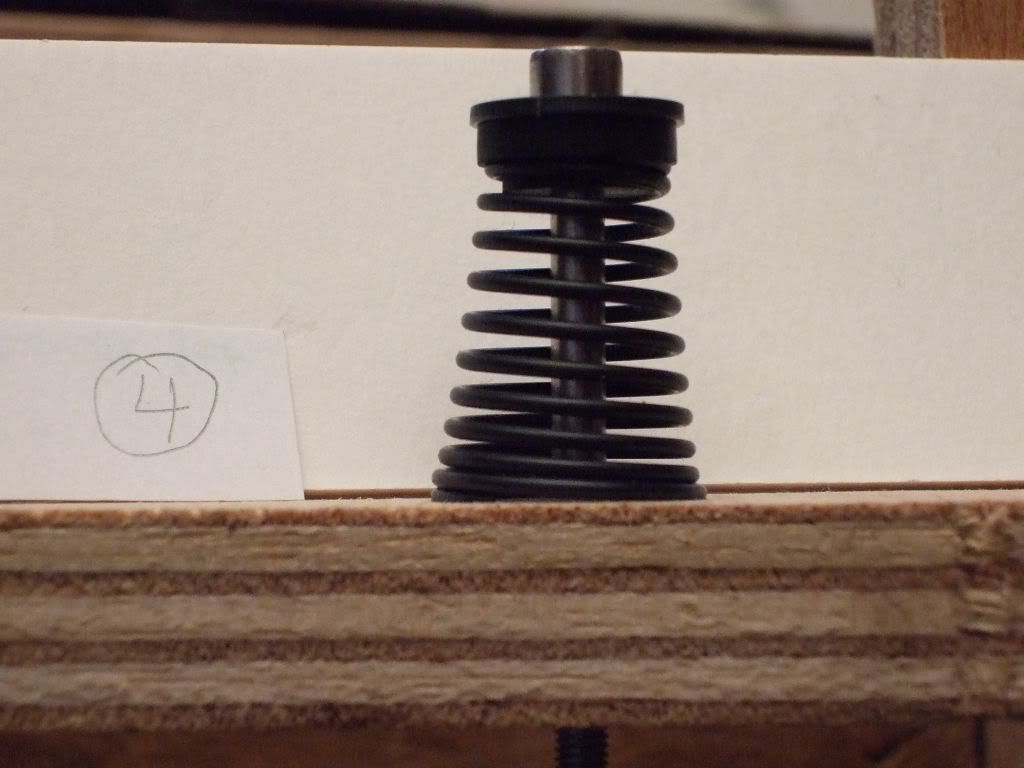
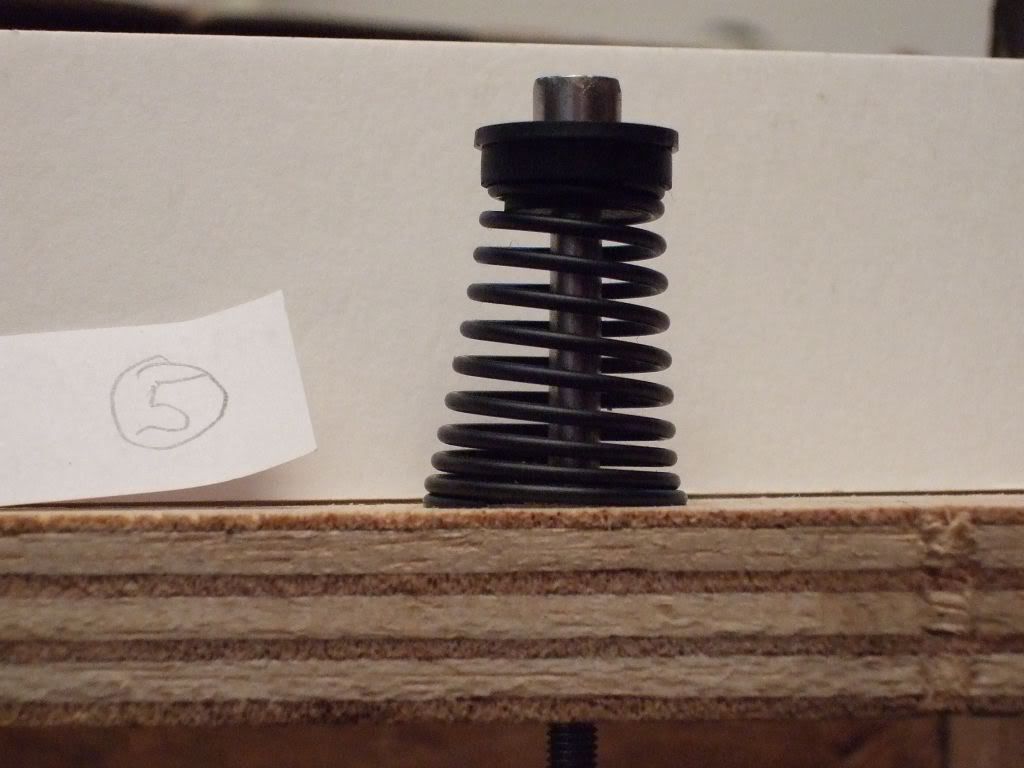
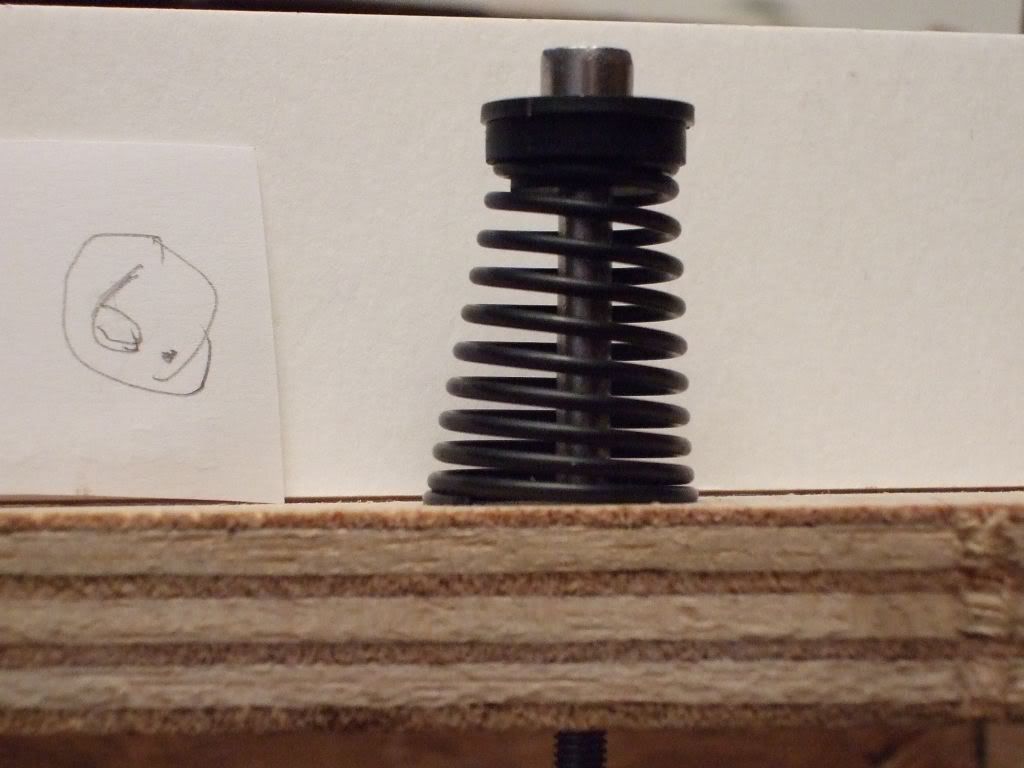
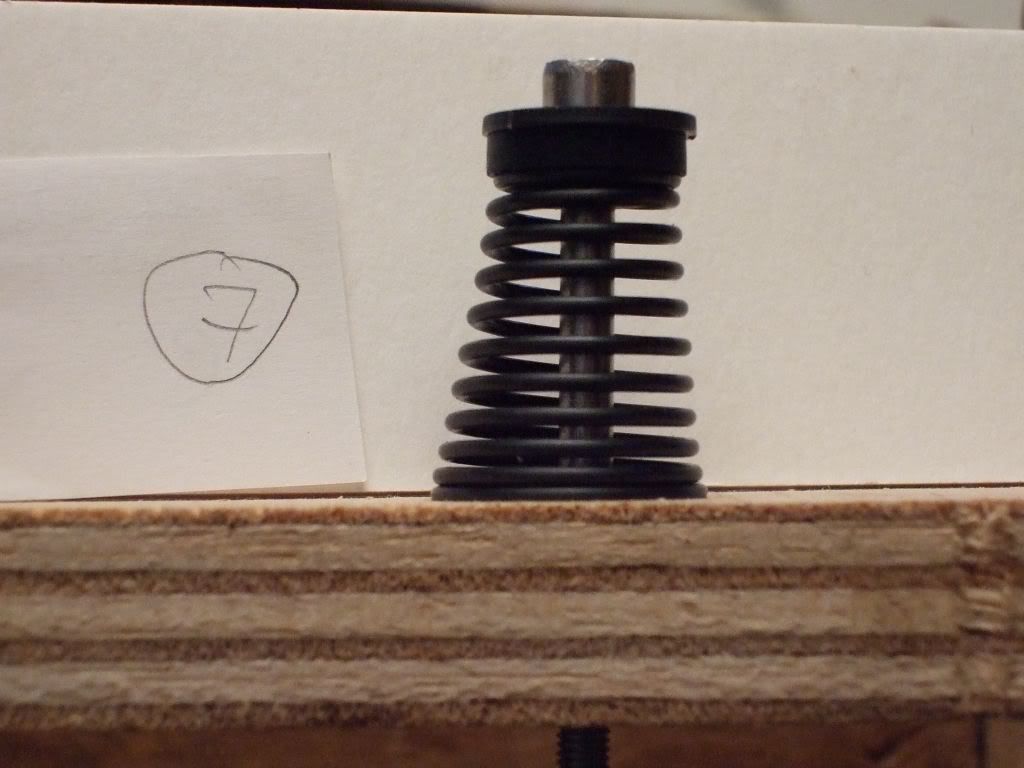
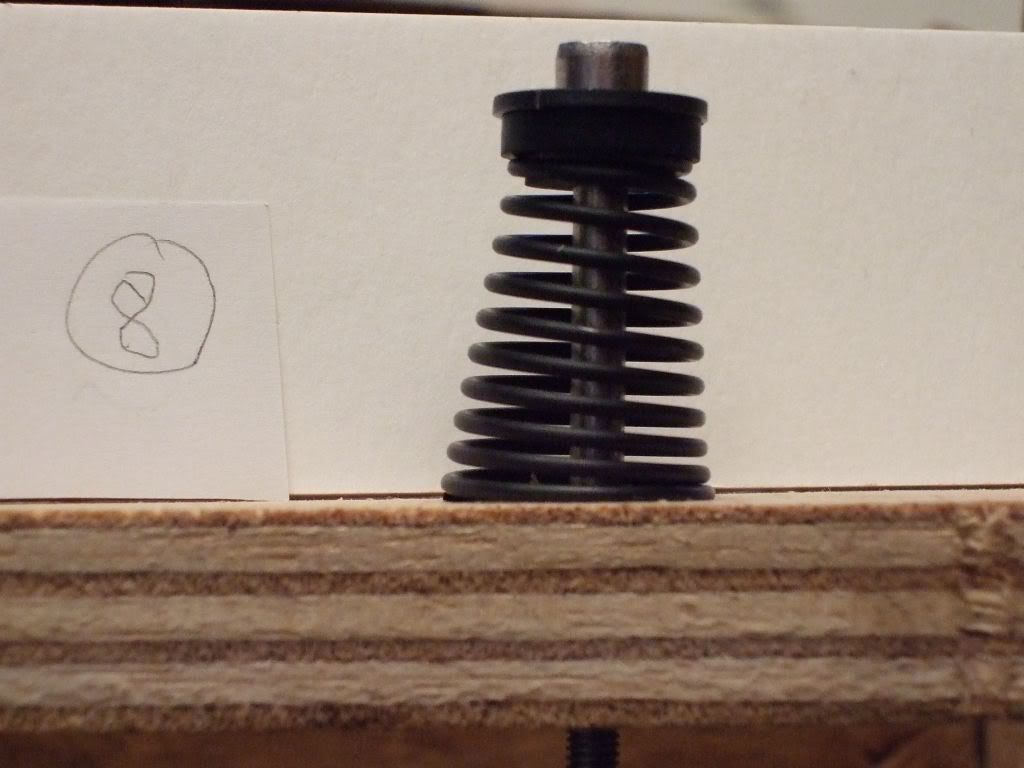
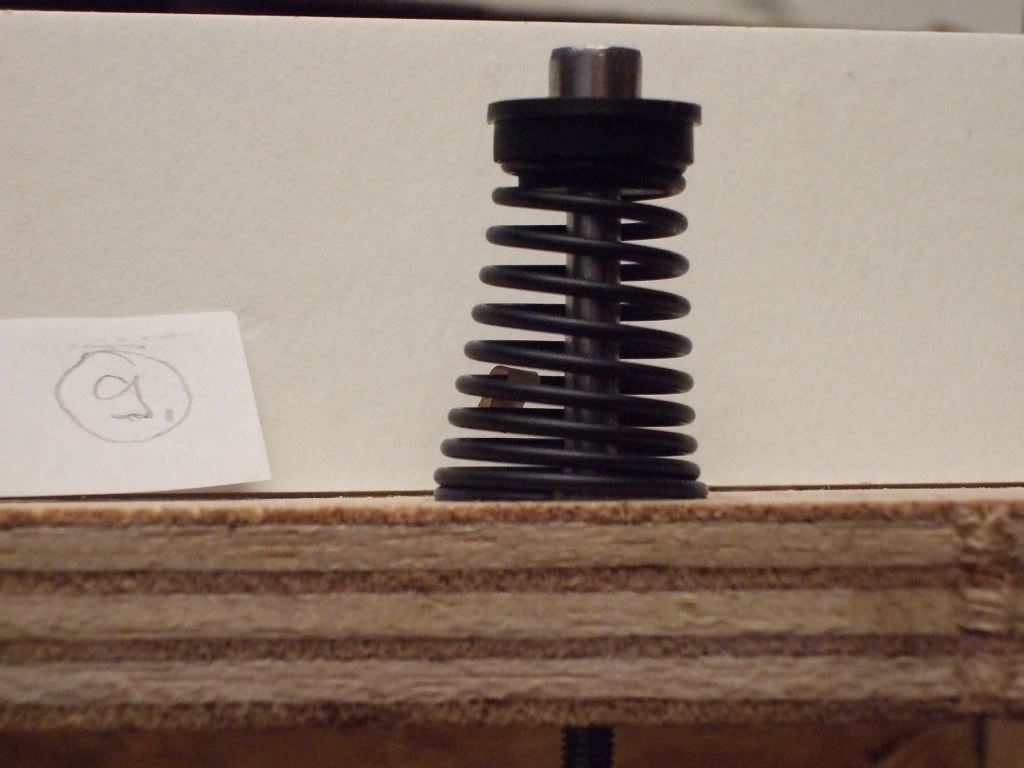
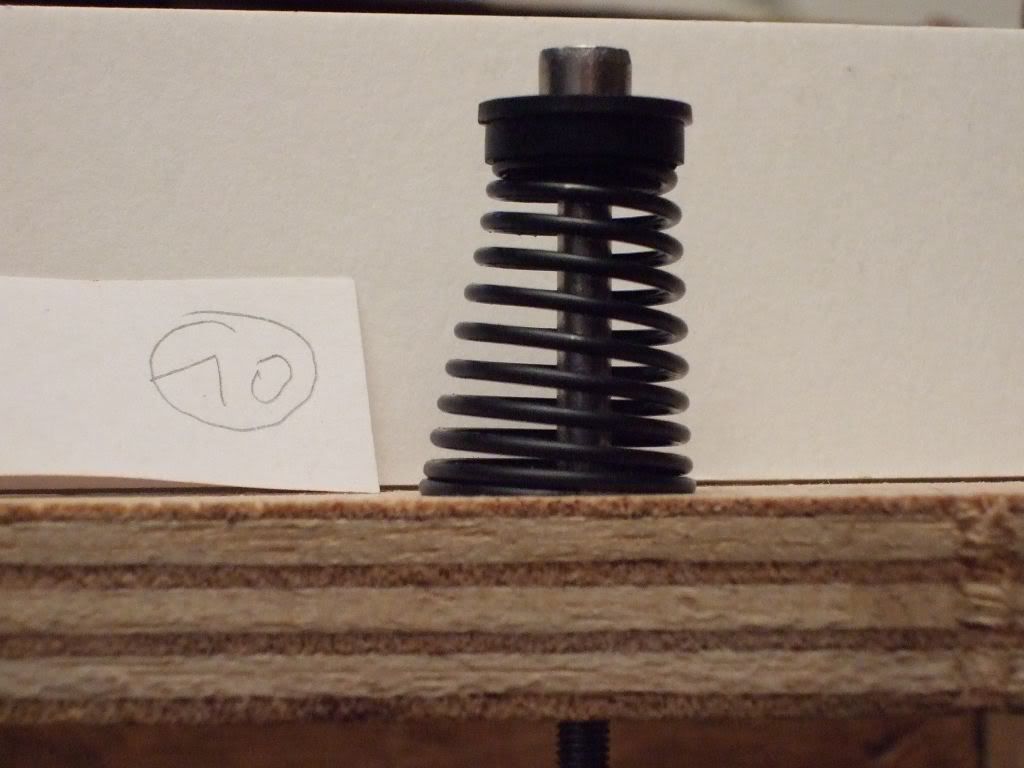
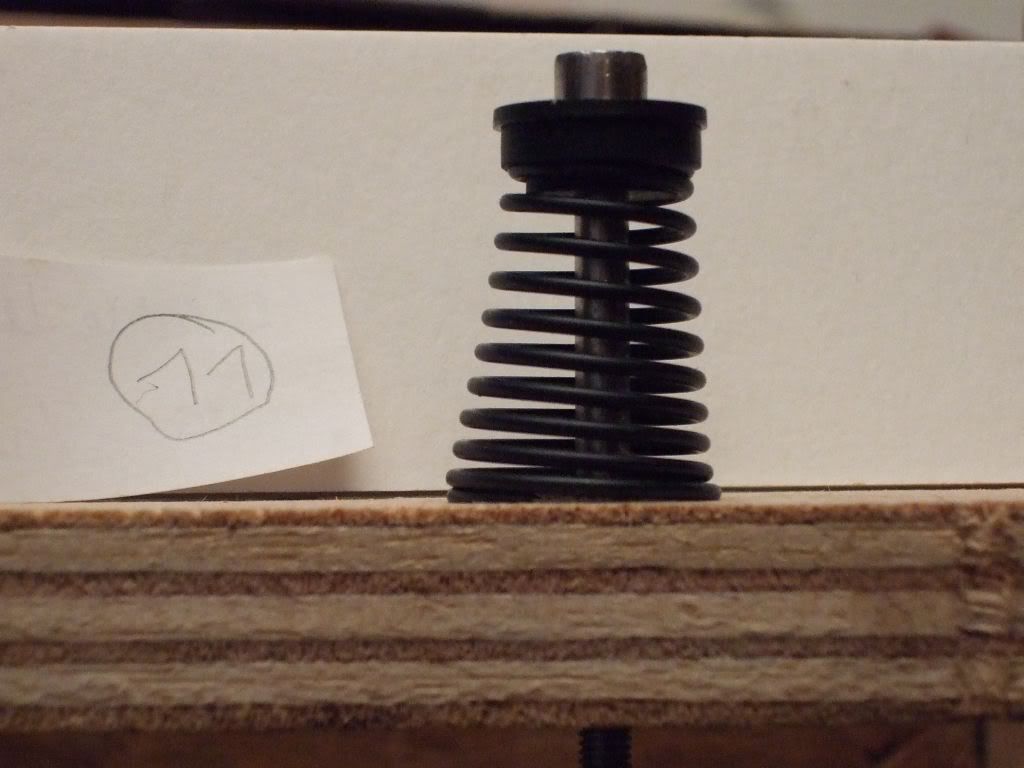
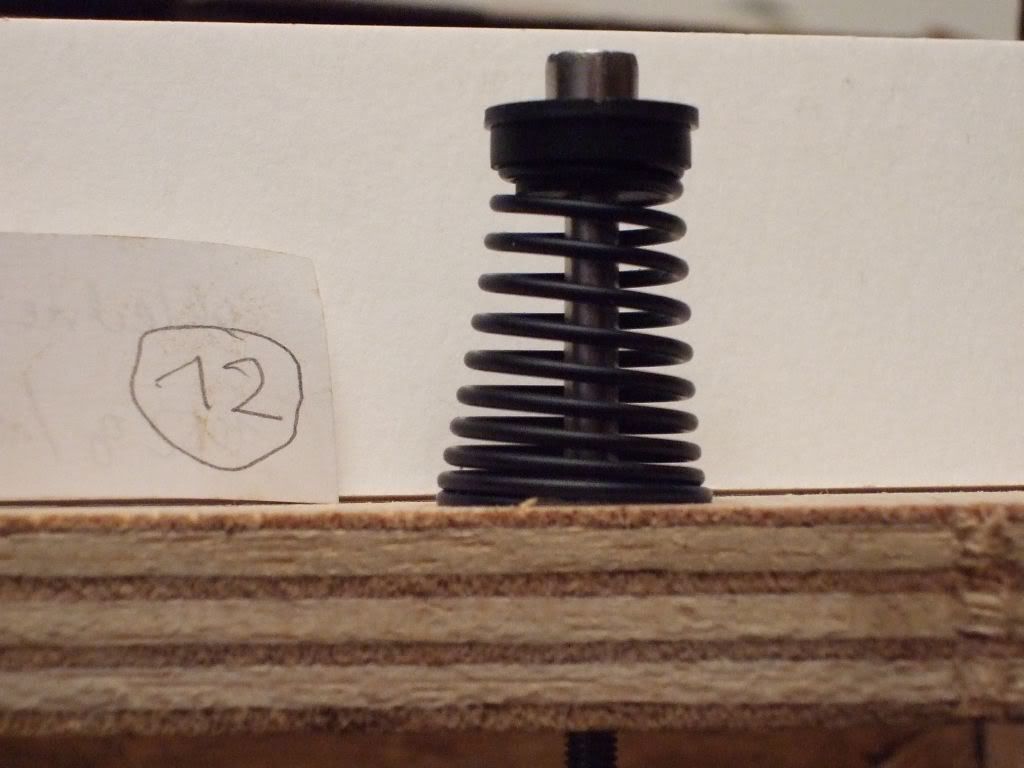
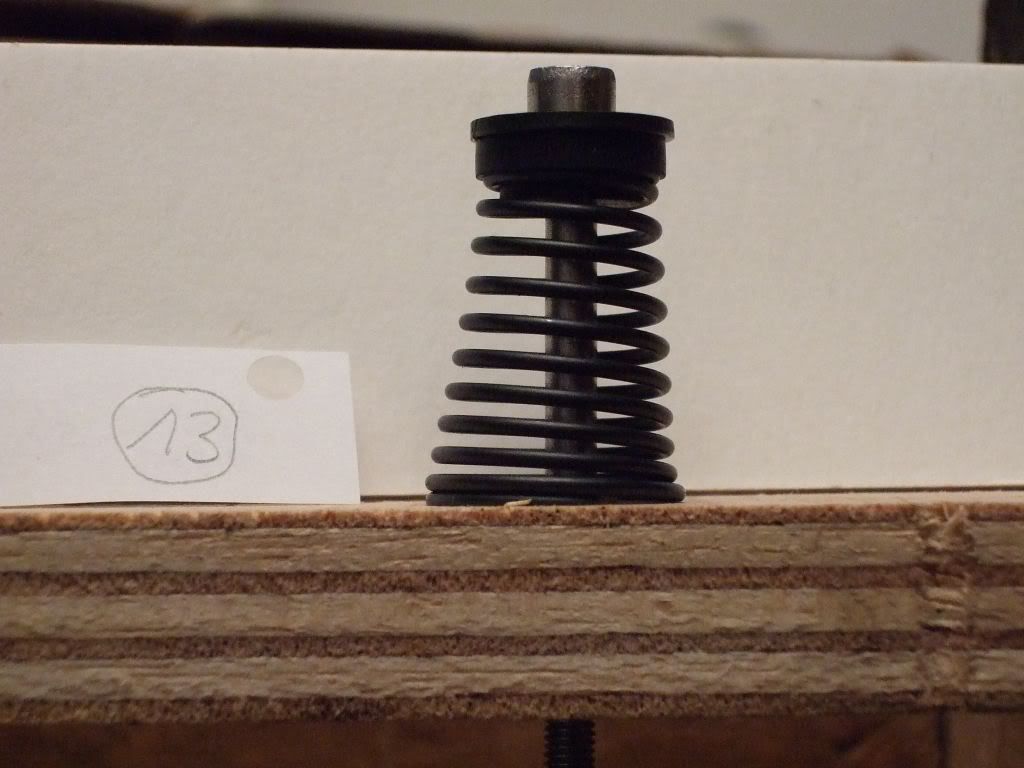
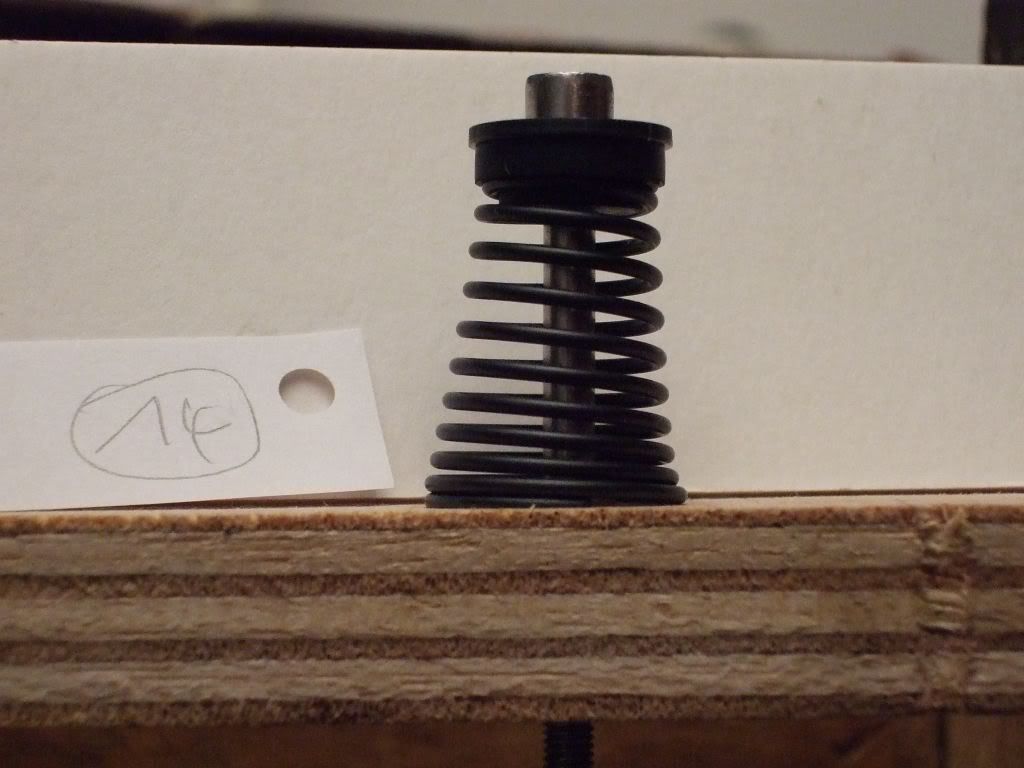
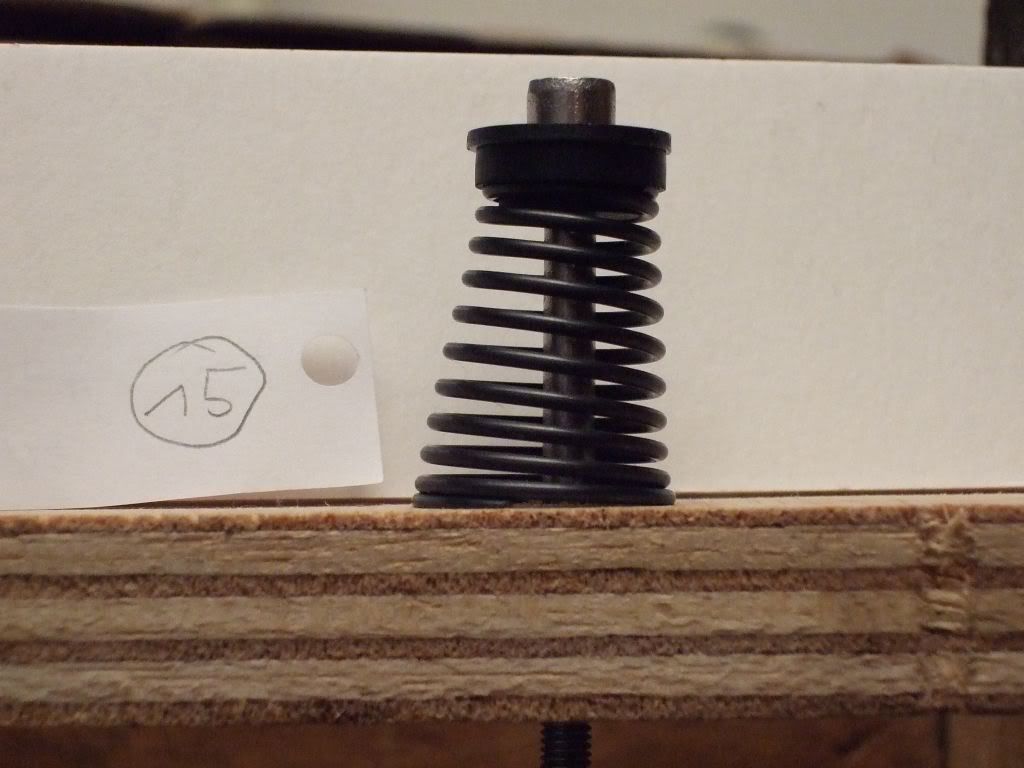
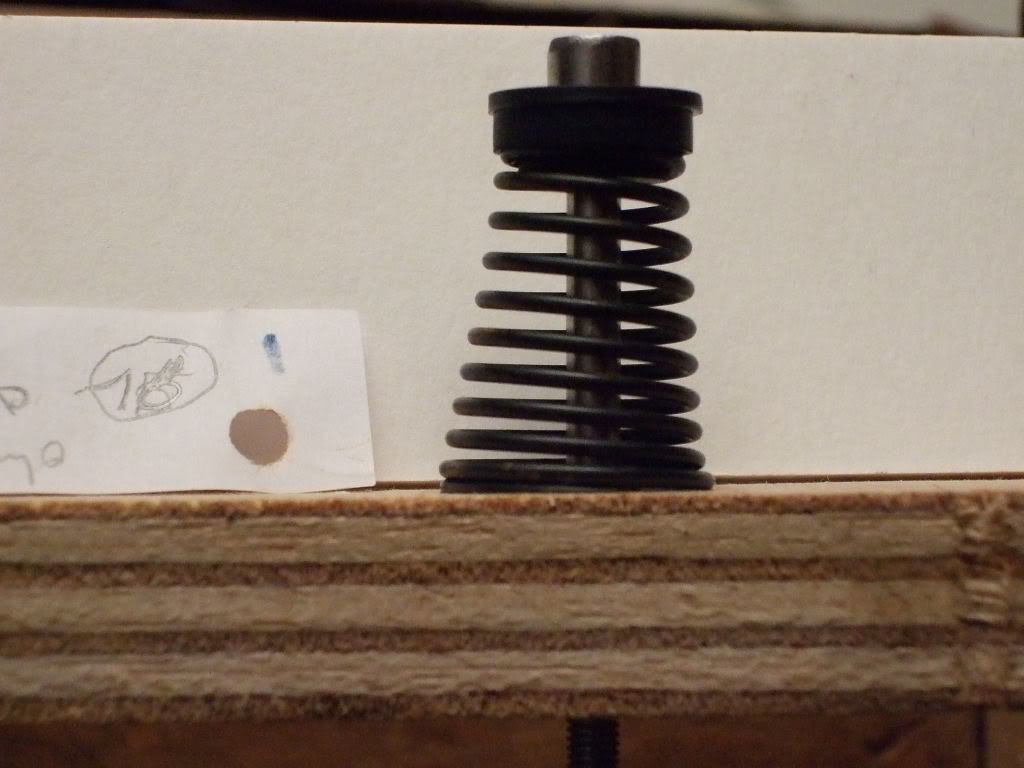
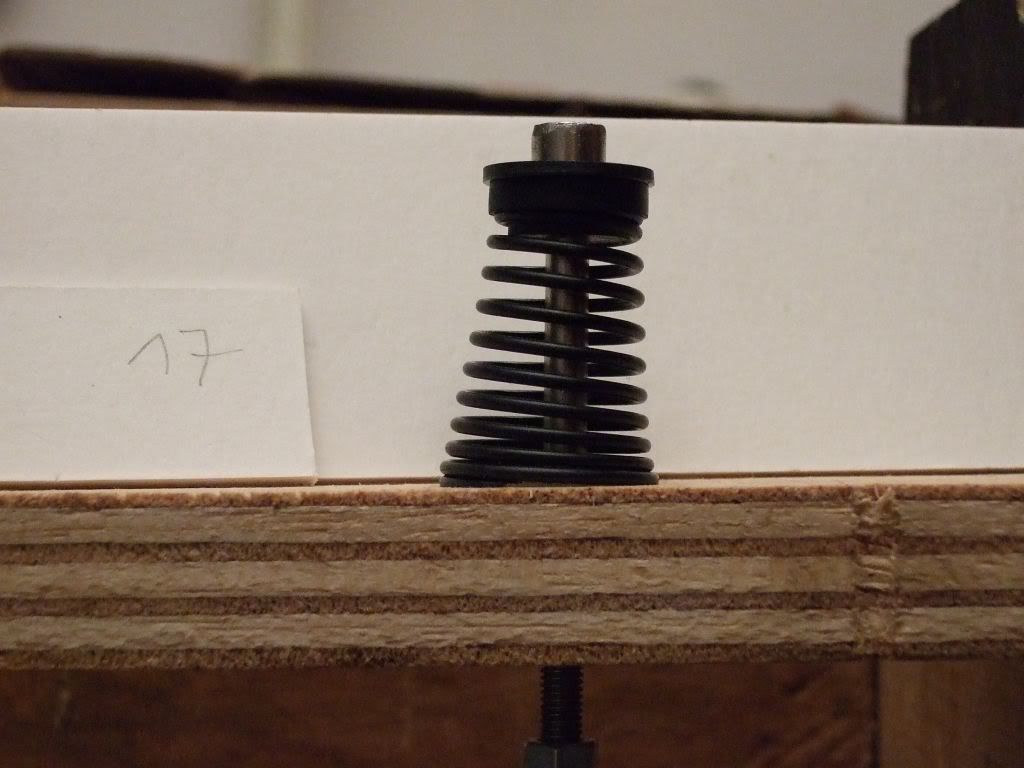
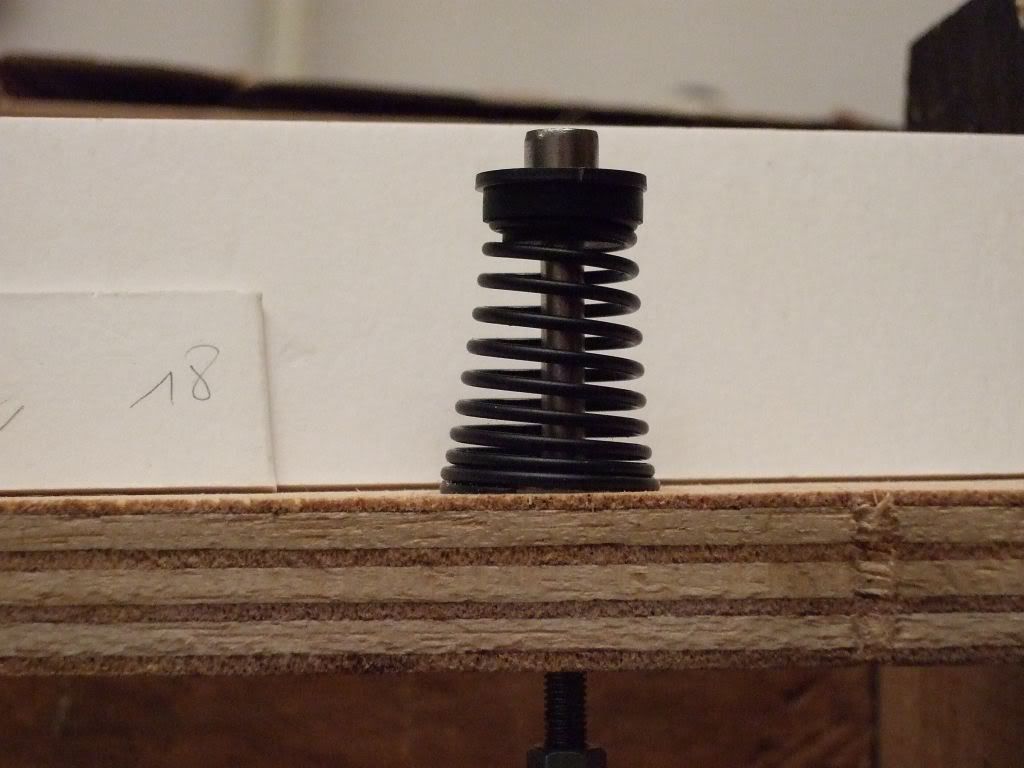
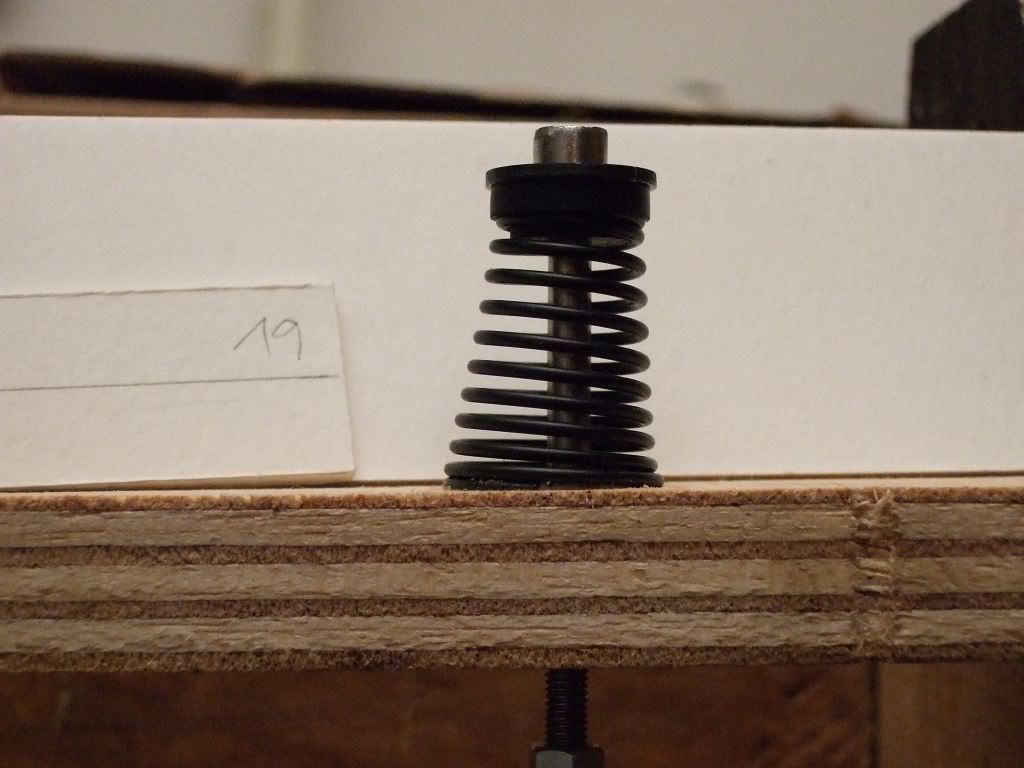
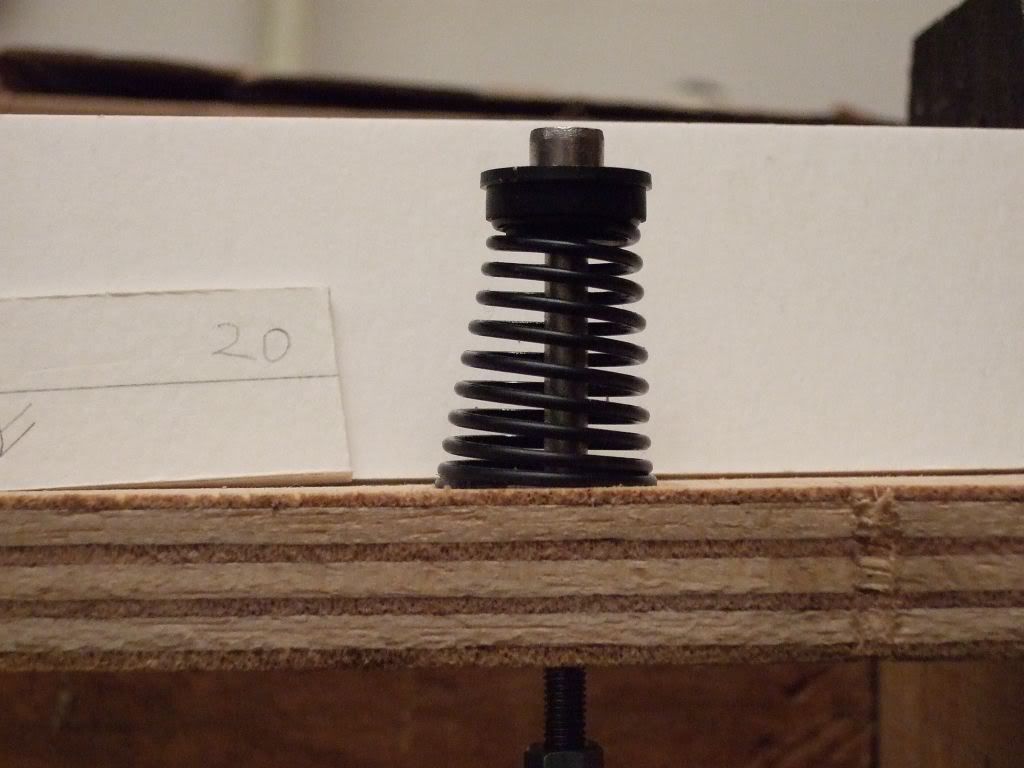
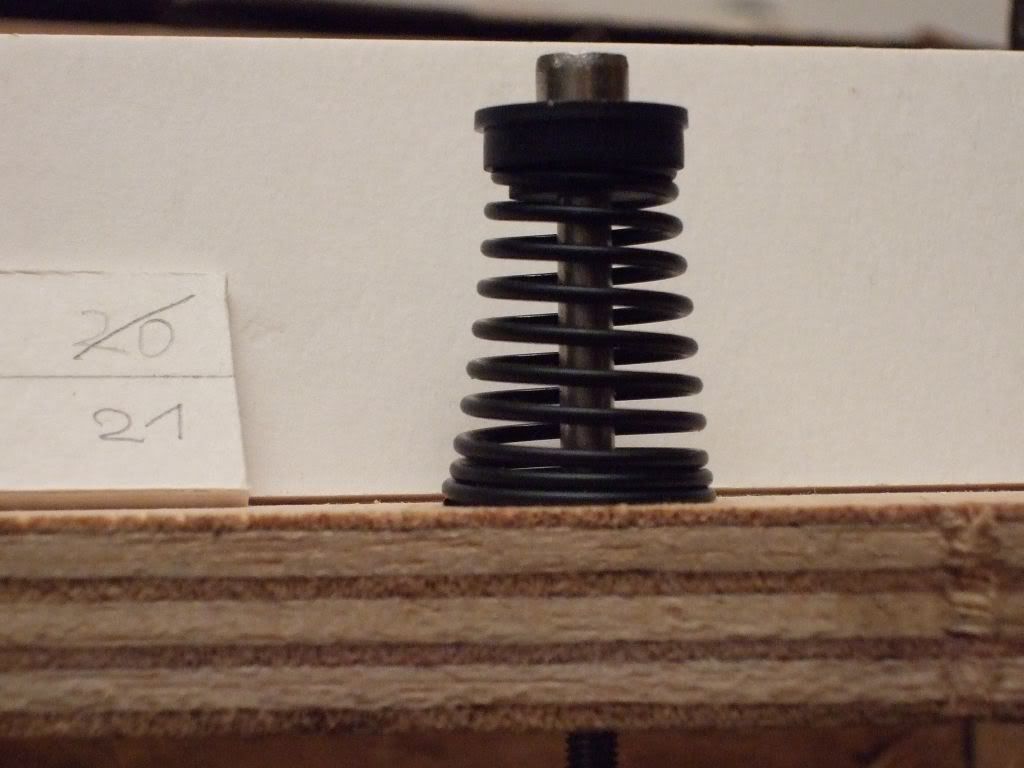
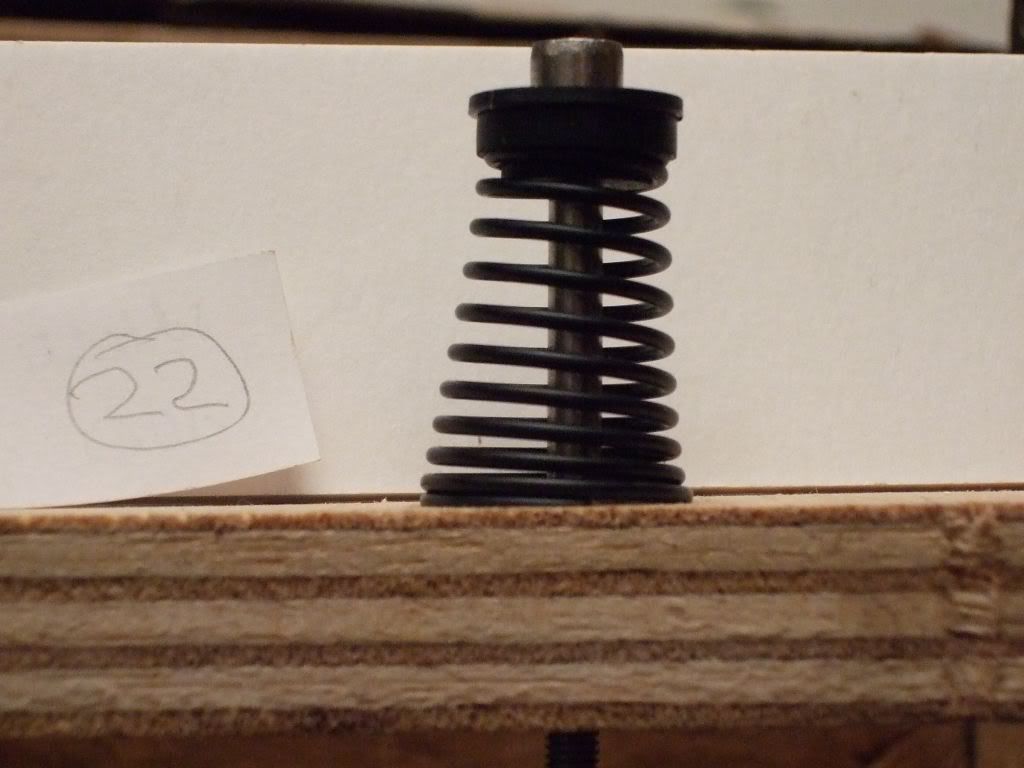
It seems as if they have a systematic tendency to a certain
excentricity, presumably due to the production process. Most of
them look quite similar. Regards, Klaus
it is springs forced downward by 1500 g:
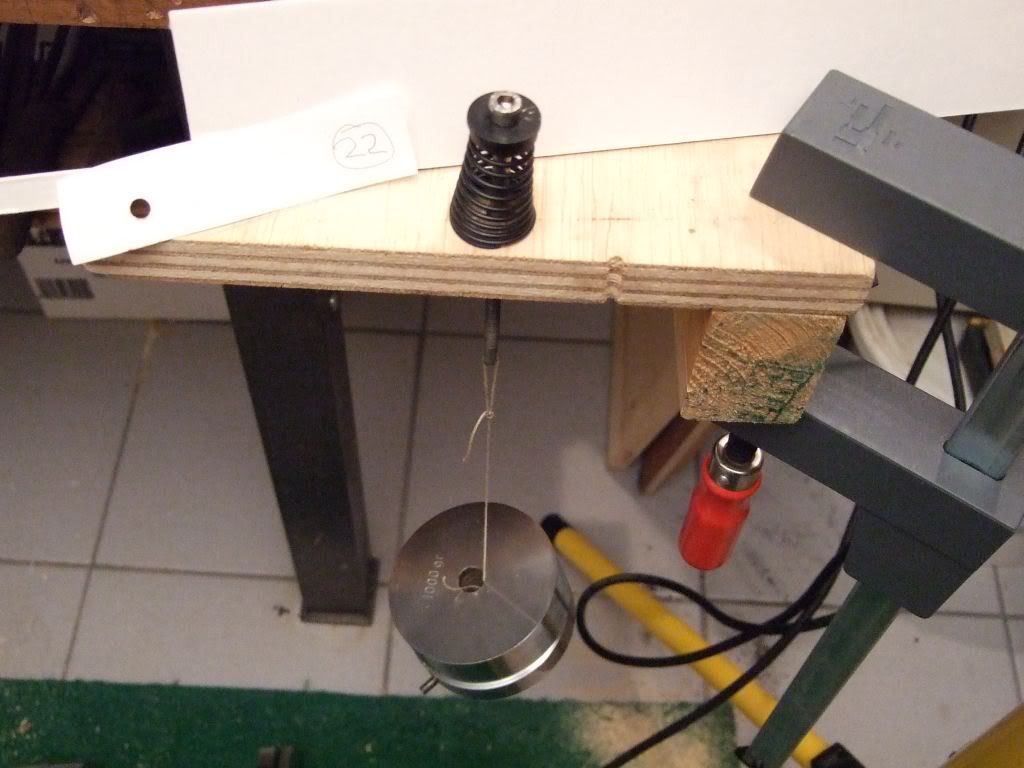
22 have been checked:
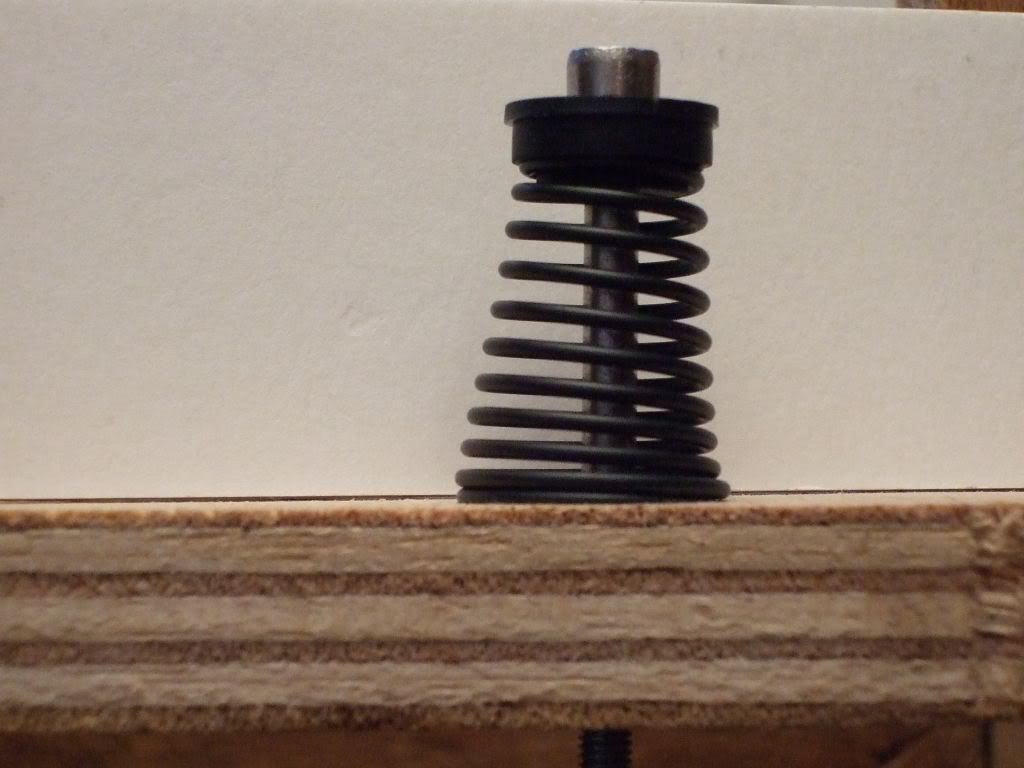
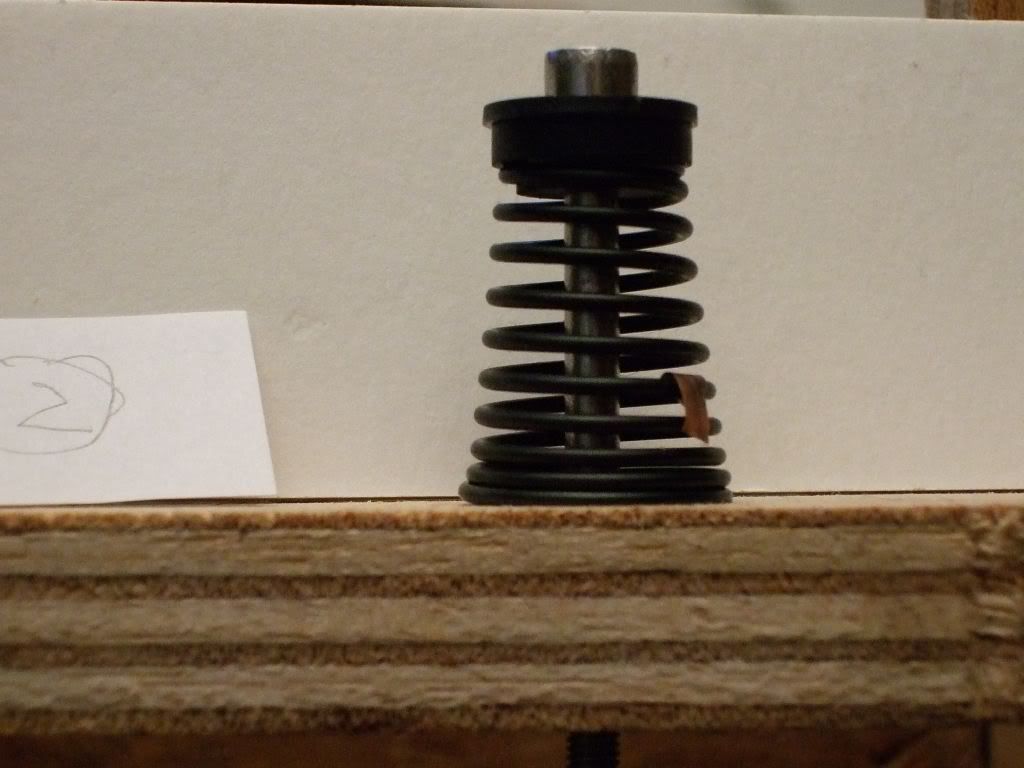
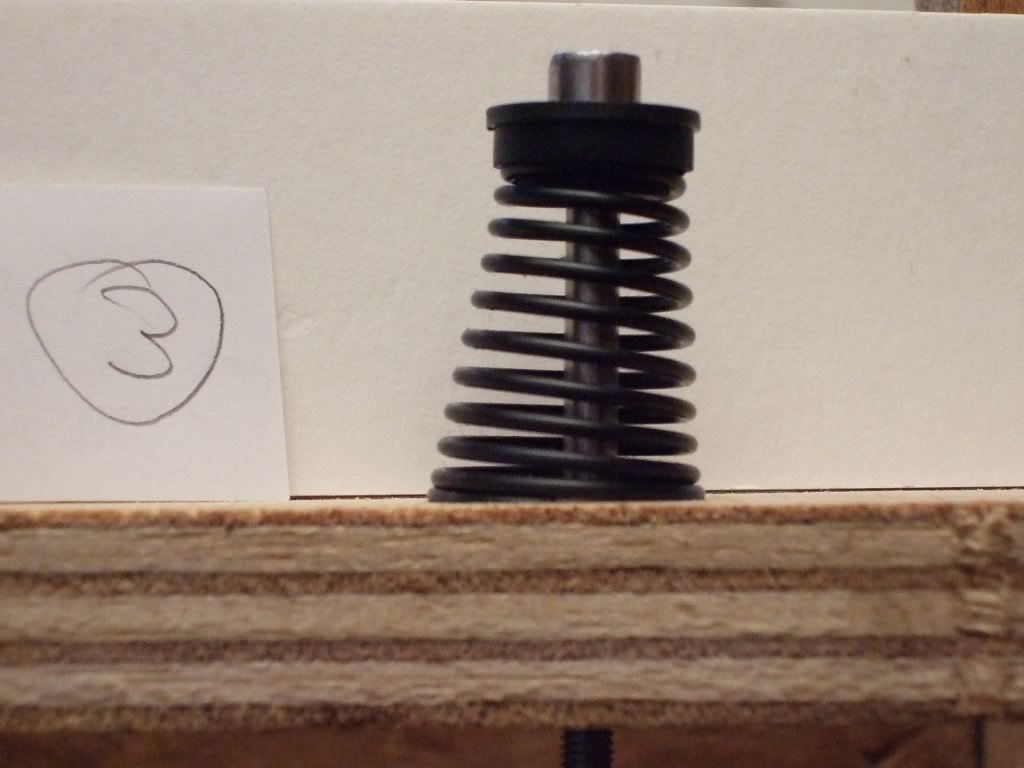
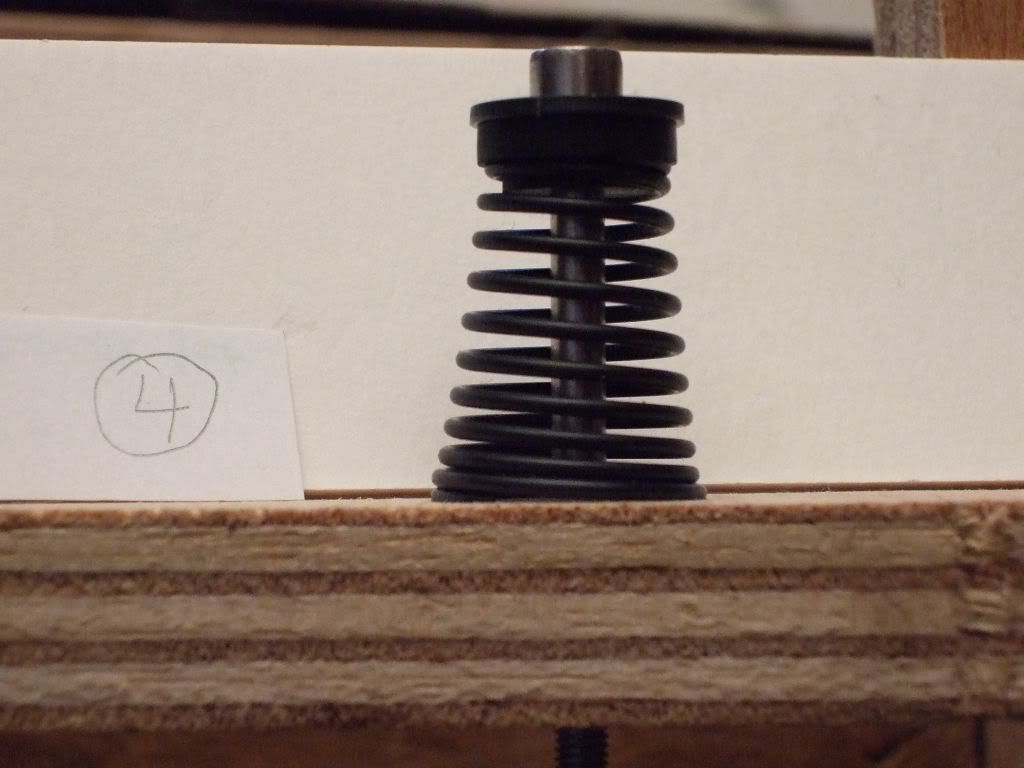
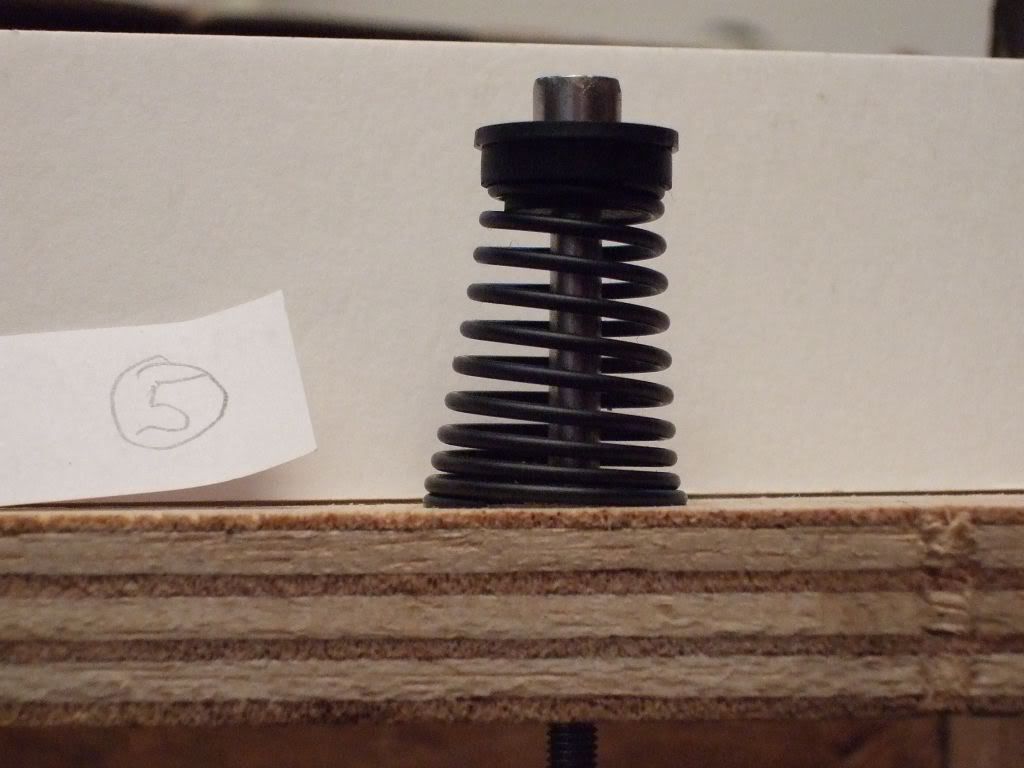
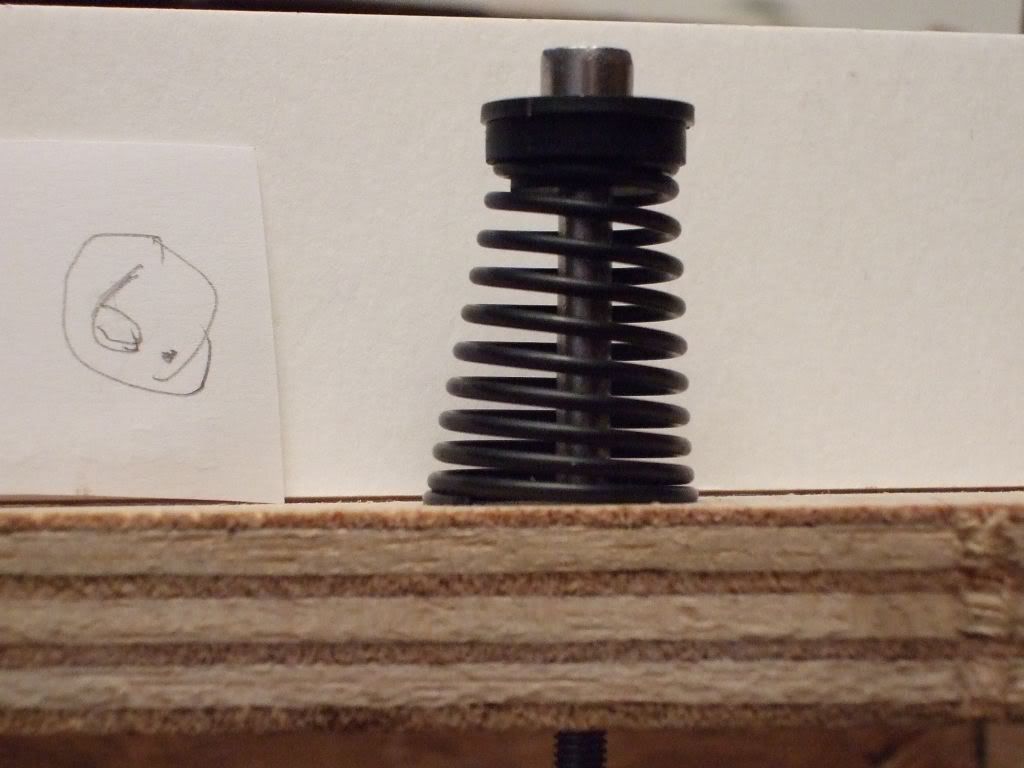
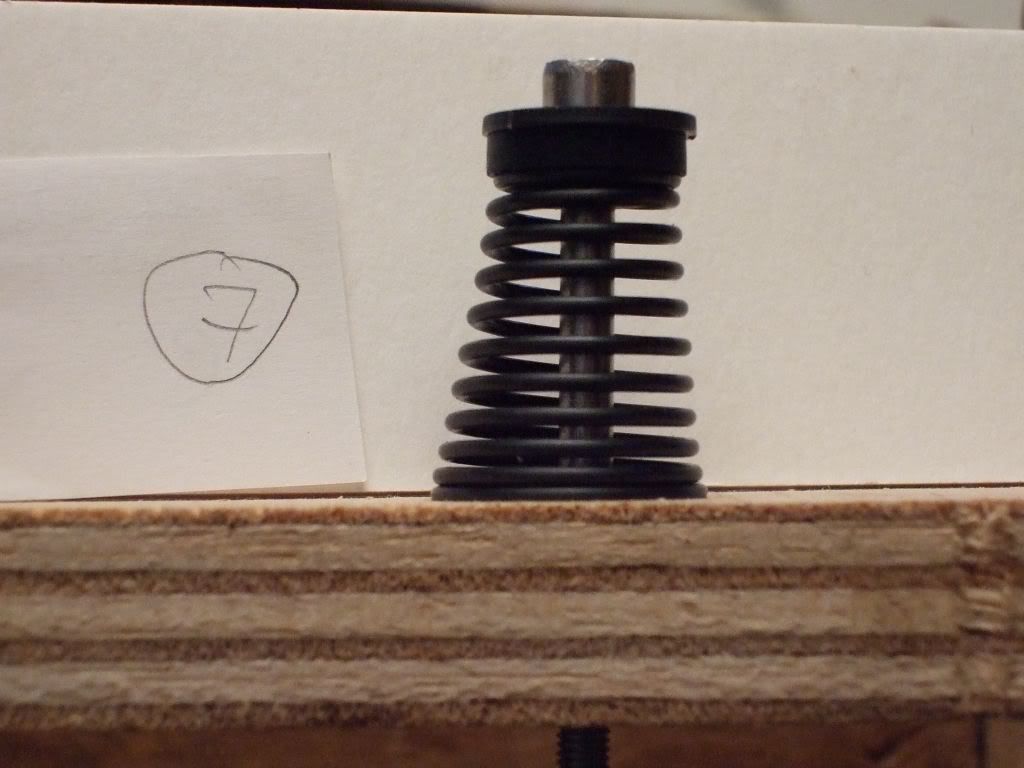
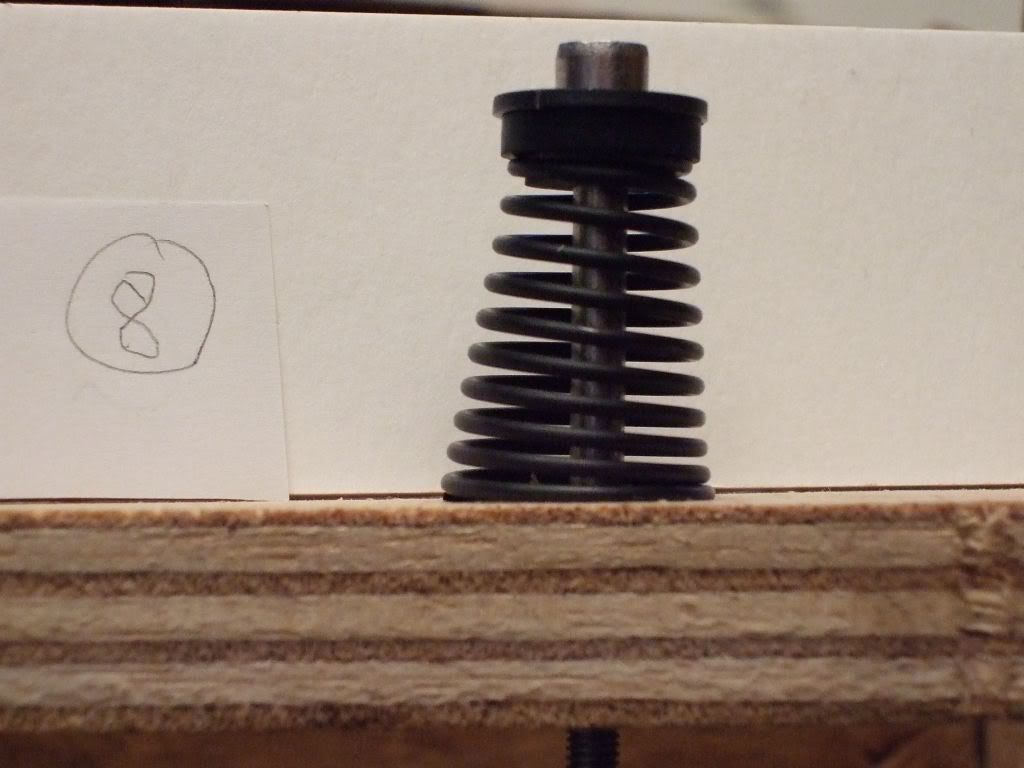
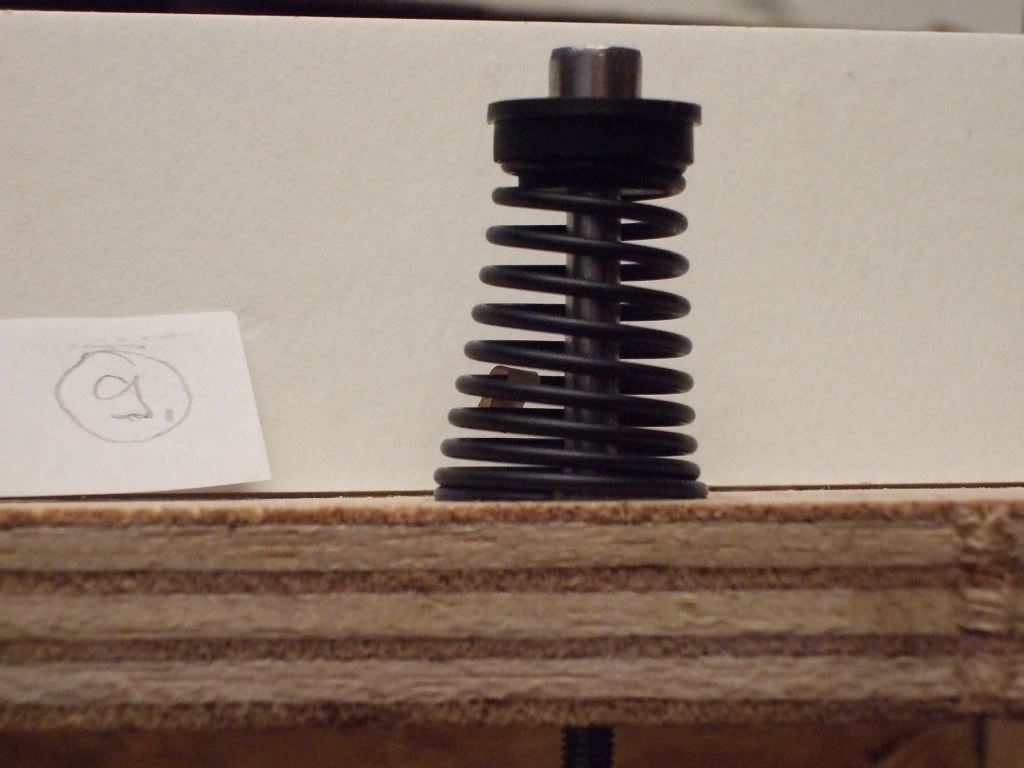
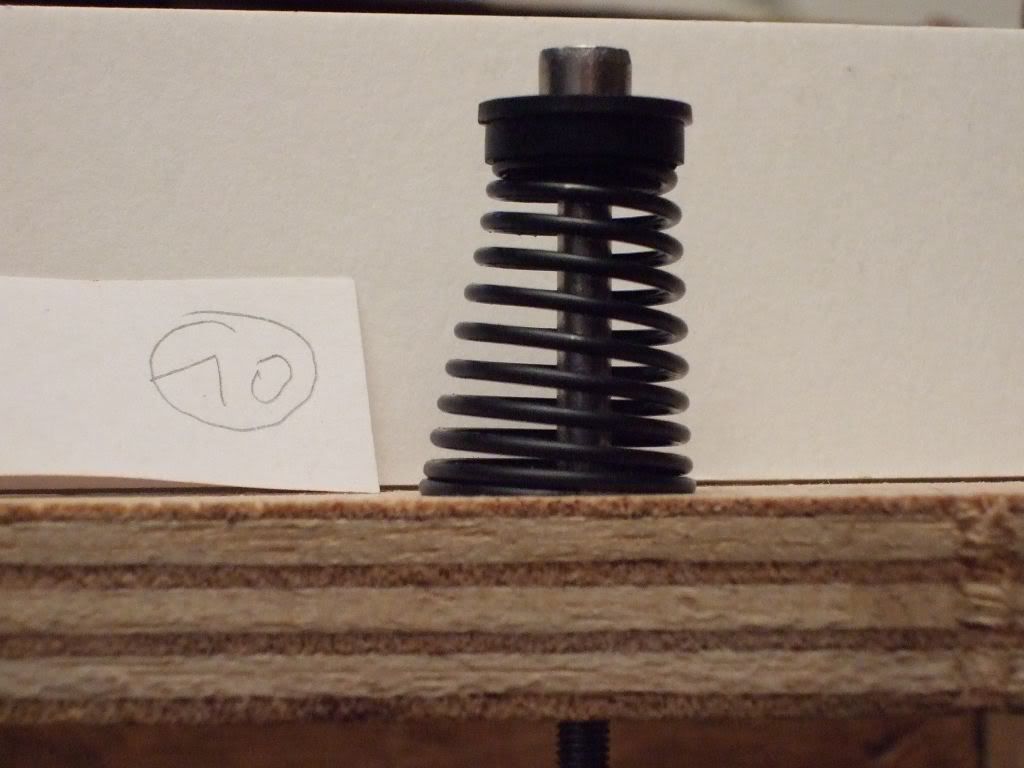
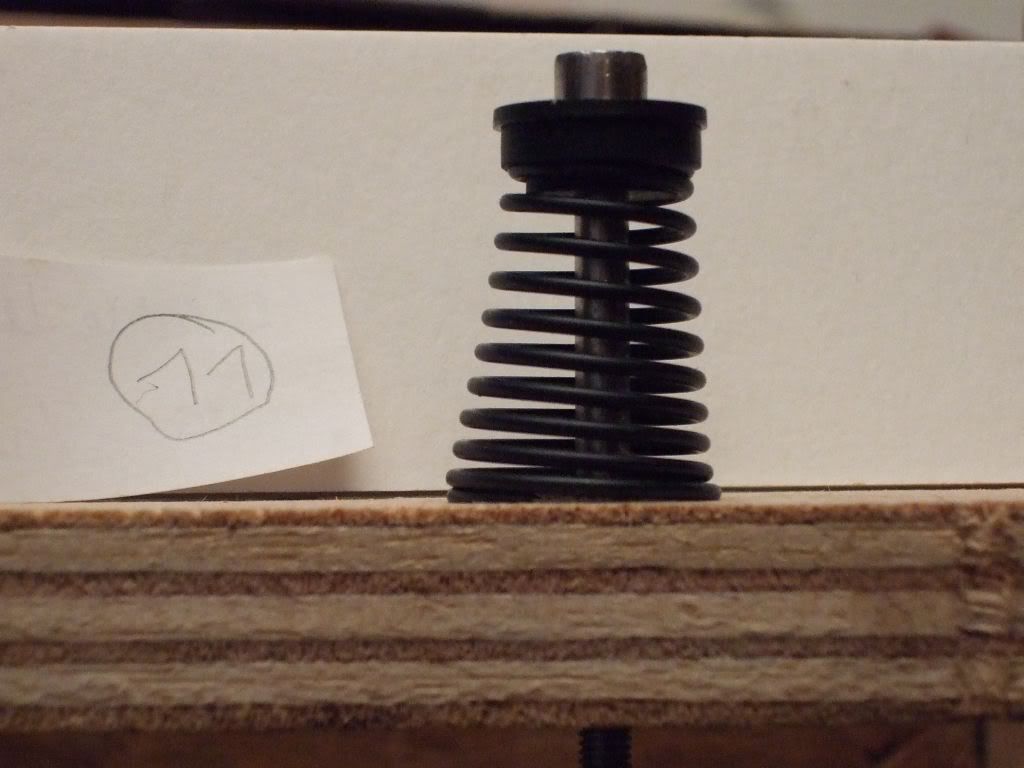
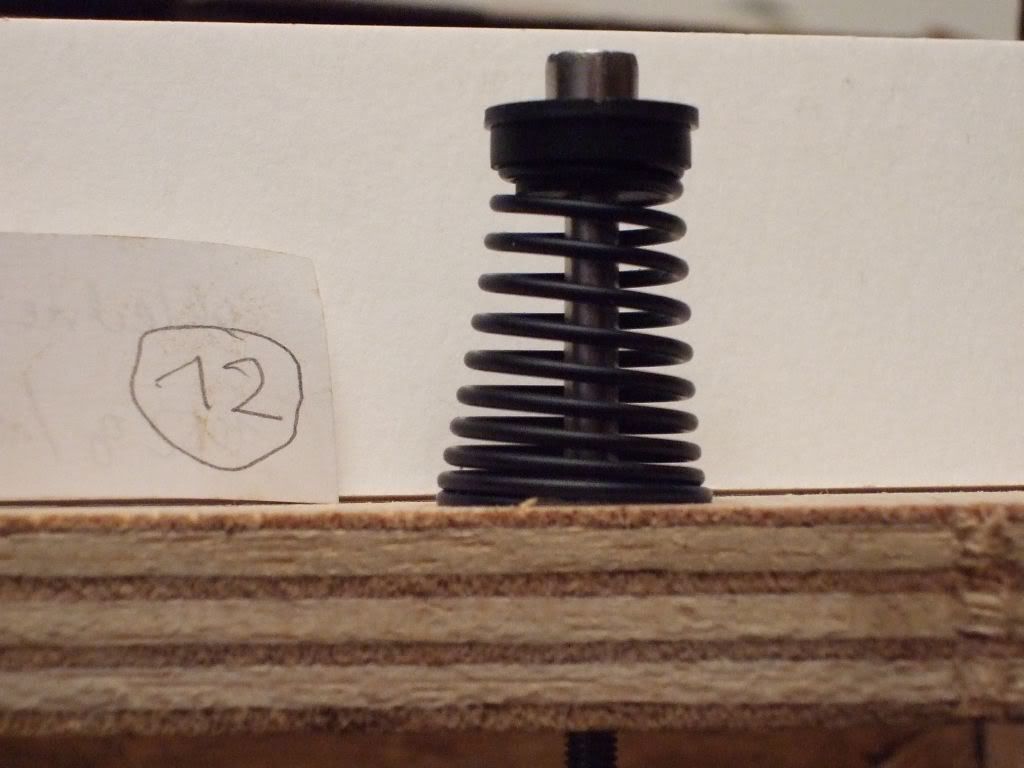
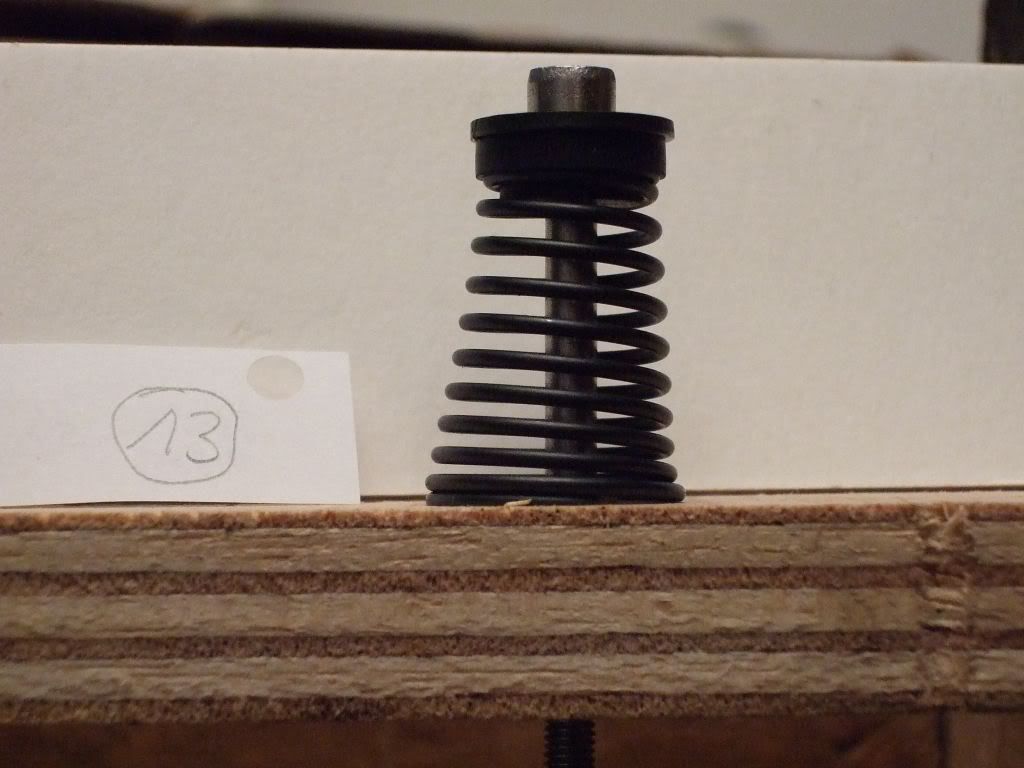
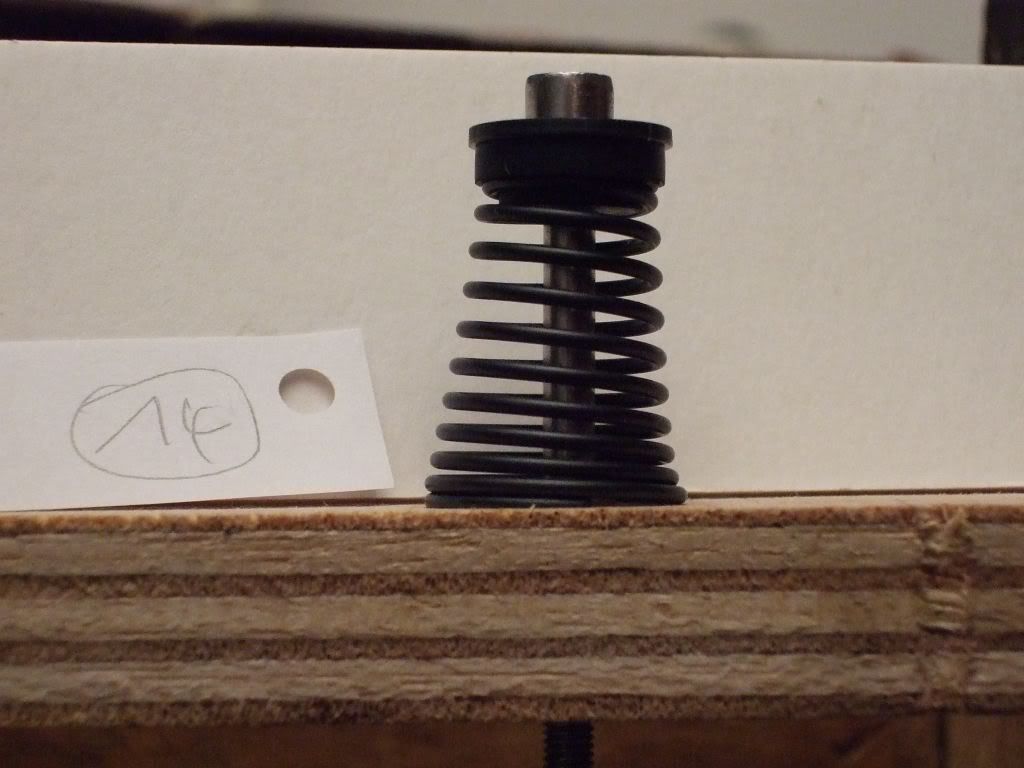
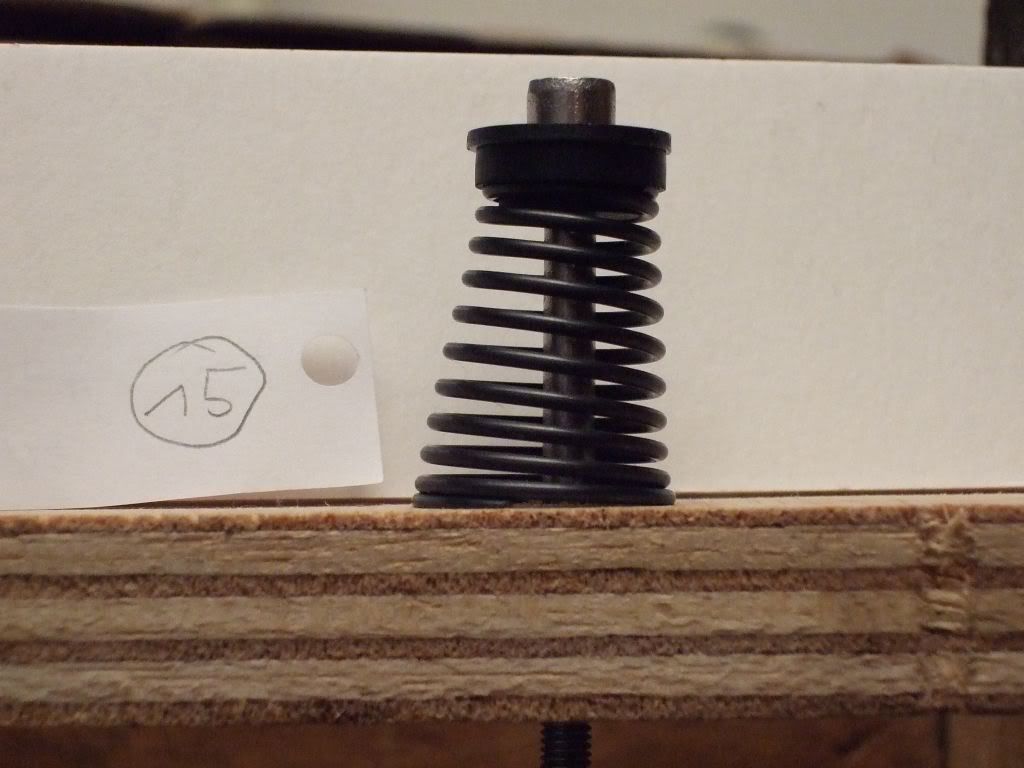
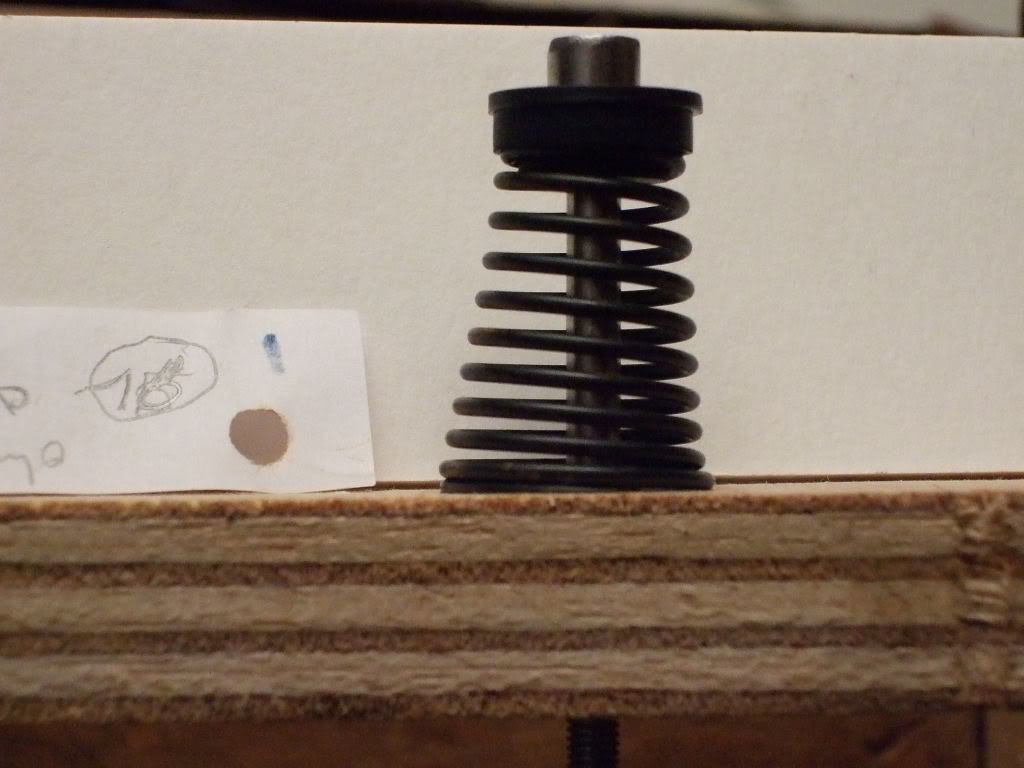
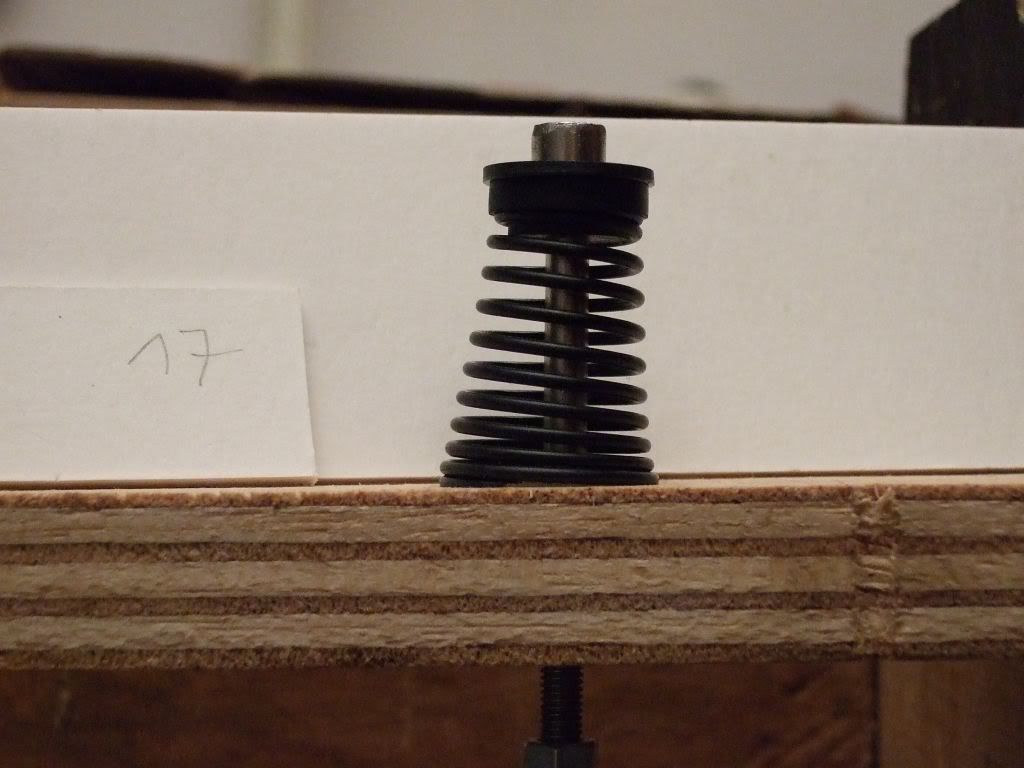
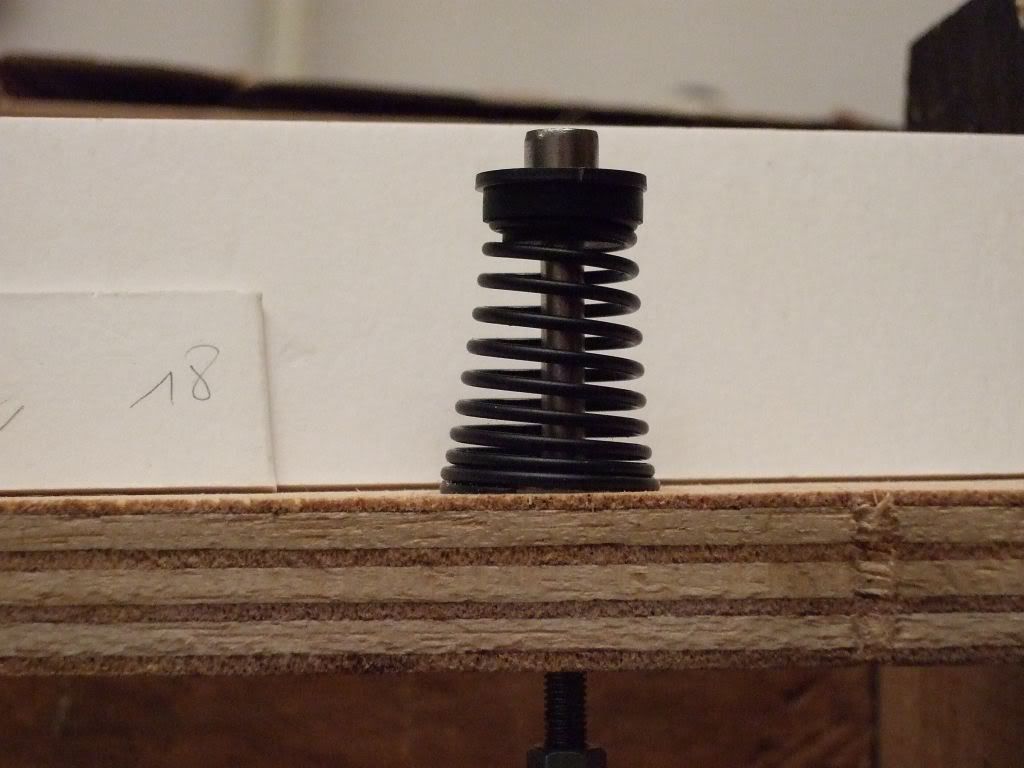
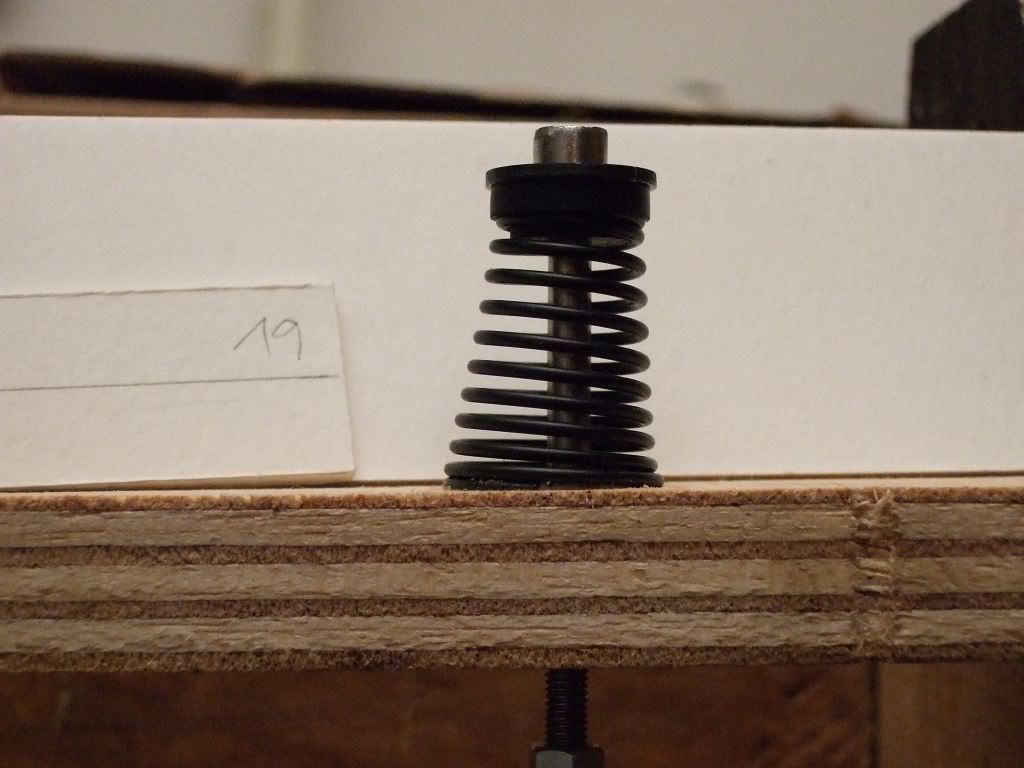
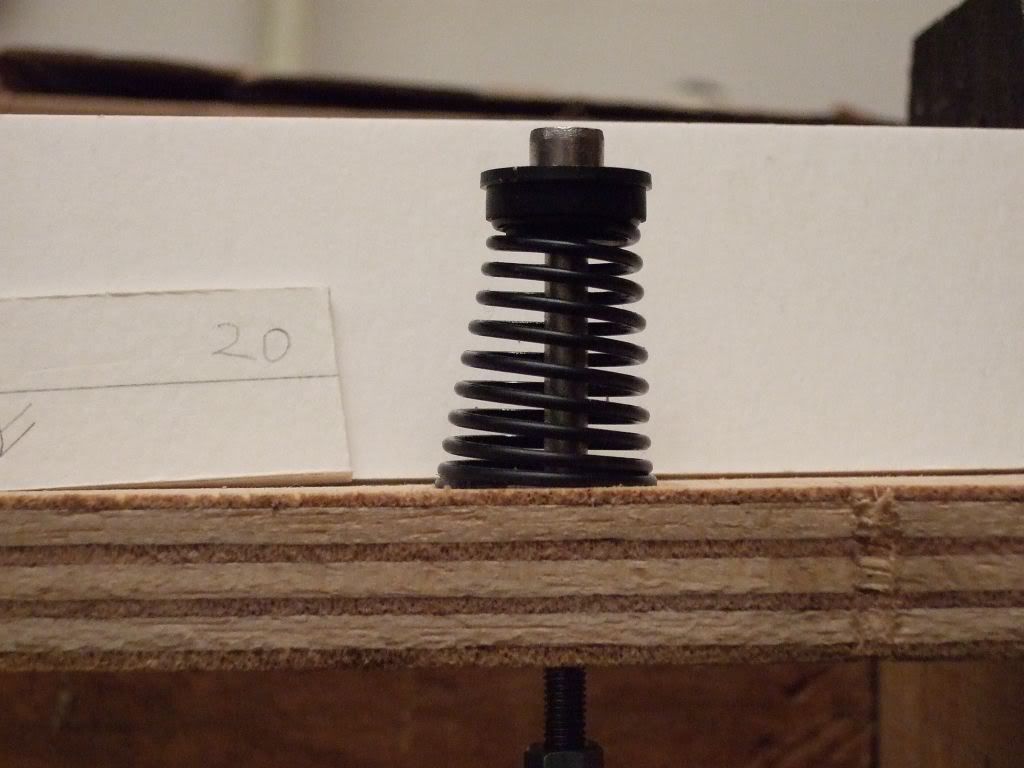
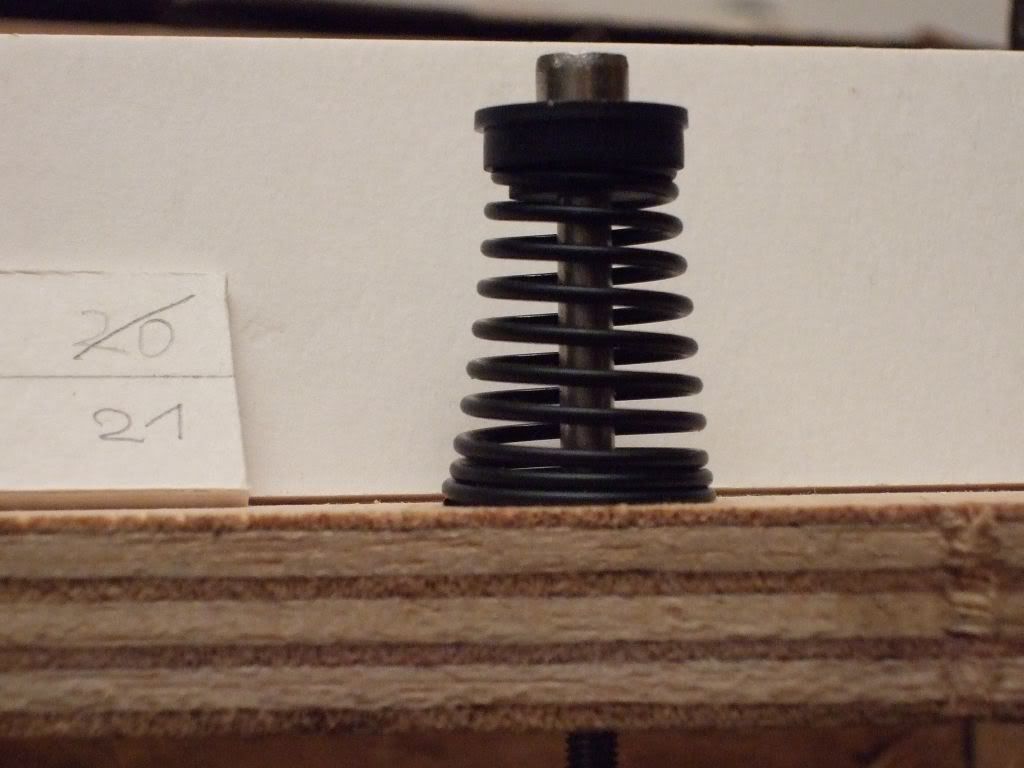
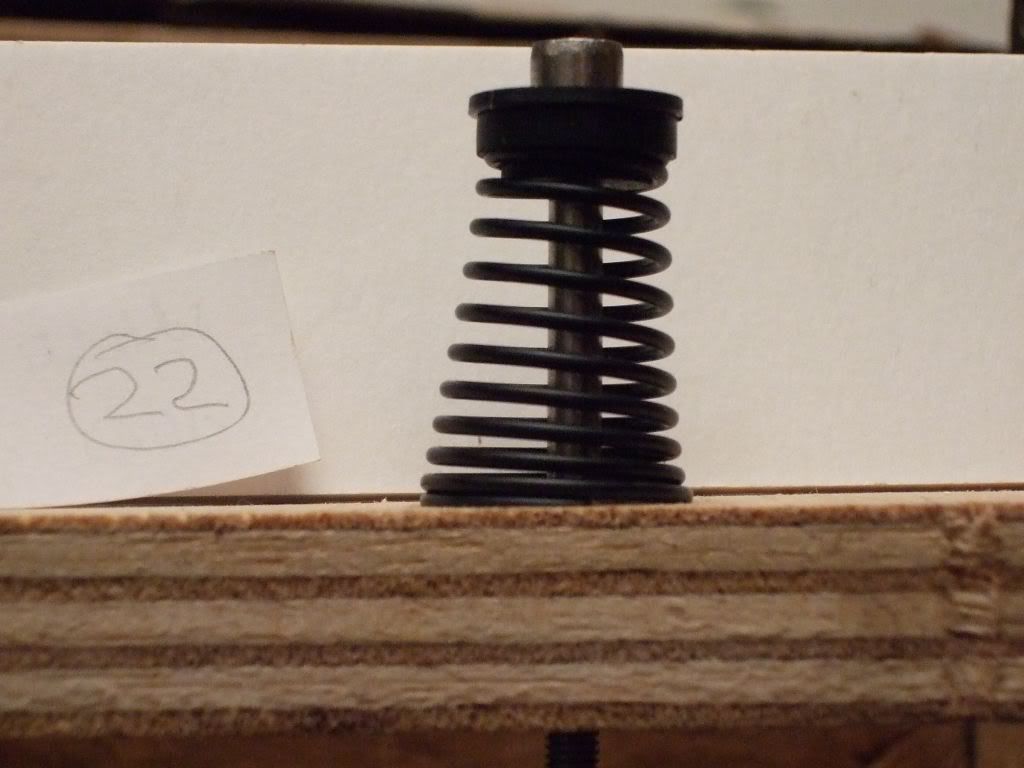
It seems as if they have a systematic tendency to a certain
excentricity, presumably due to the production process. Most of
them look quite similar. Regards, Klaus
Yes, they do stand out in terms of shape on these pics. BUT with a
load of 1500 g only..... They share with the others the imho desastrous
property that the bolt wanders laterally as the load varies. This means
that the oscillation line is simply not plumb when the bolts are.
Look how the bolt wanders from left to right with a load of 1500g, 500g, and zero:
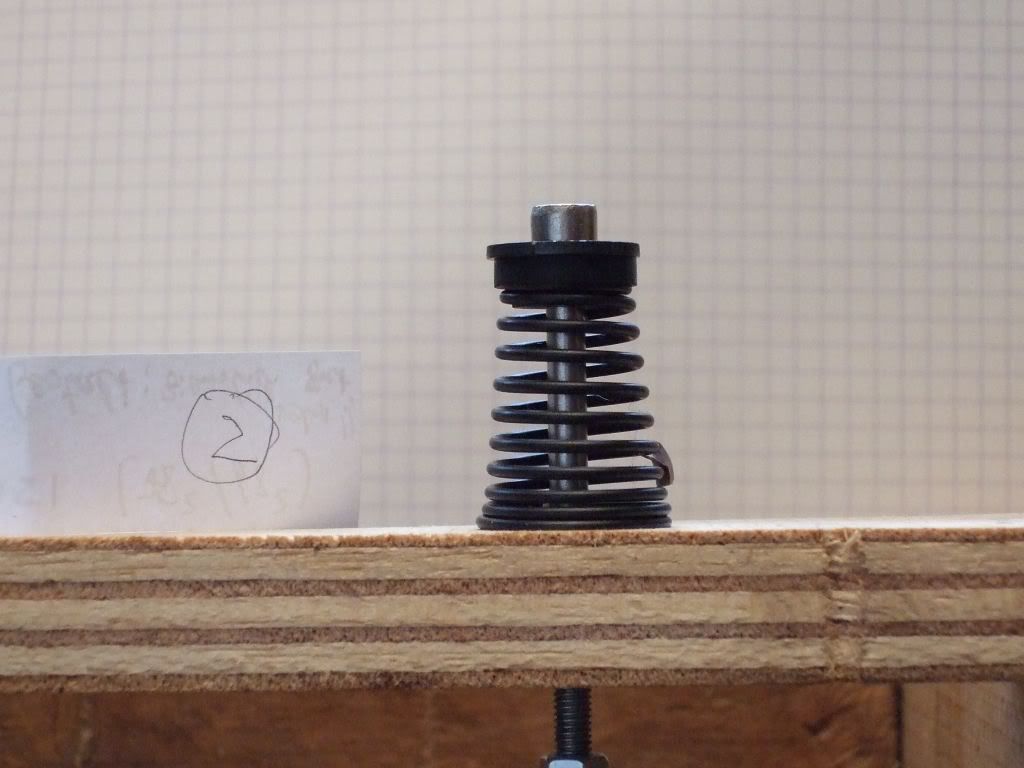
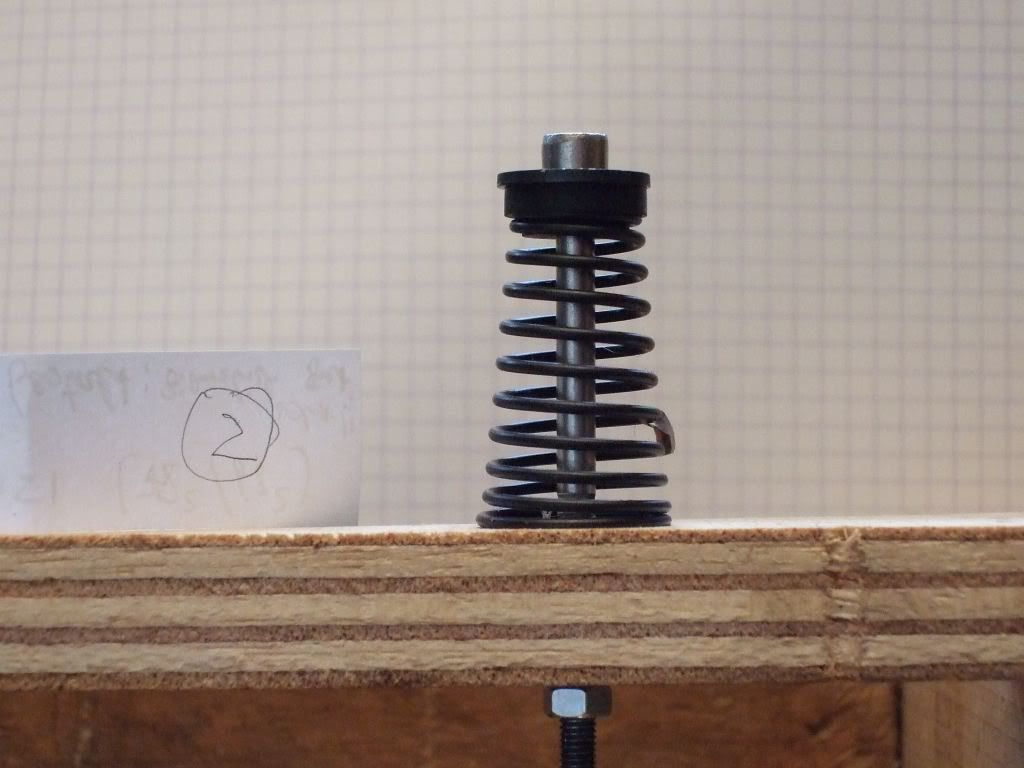
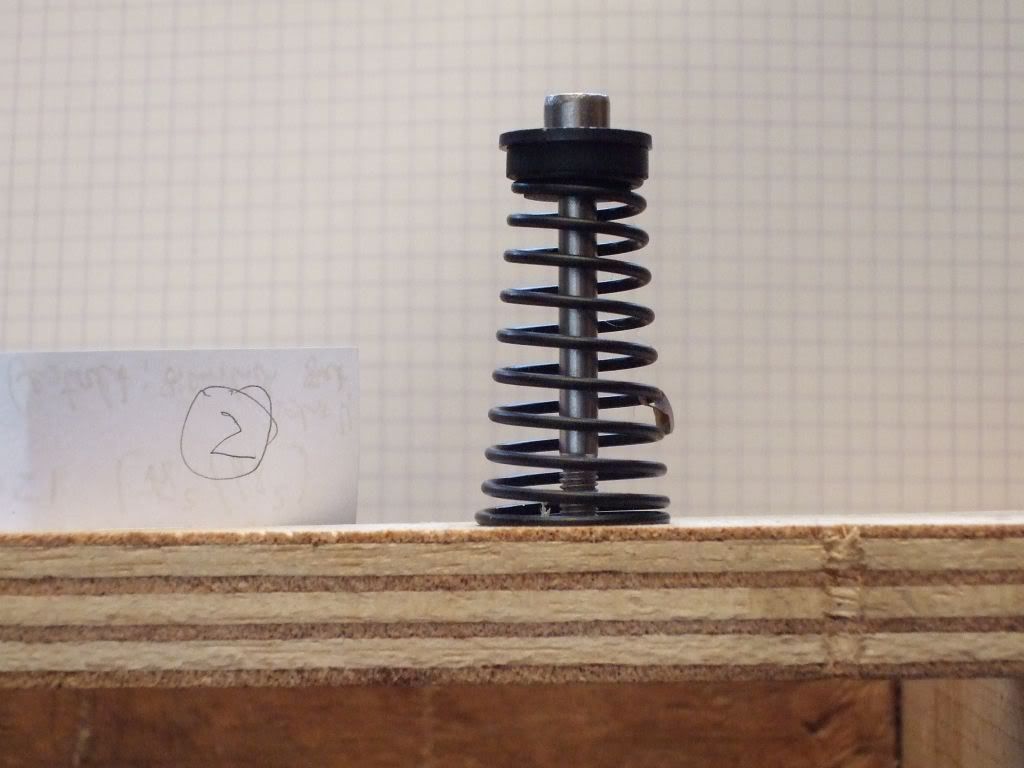
As can be seen, this is spring nr. 2.
load of 1500 g only..... They share with the others the imho desastrous
property that the bolt wanders laterally as the load varies. This means
that the oscillation line is simply not plumb when the bolts are.
Look how the bolt wanders from left to right with a load of 1500g, 500g, and zero:
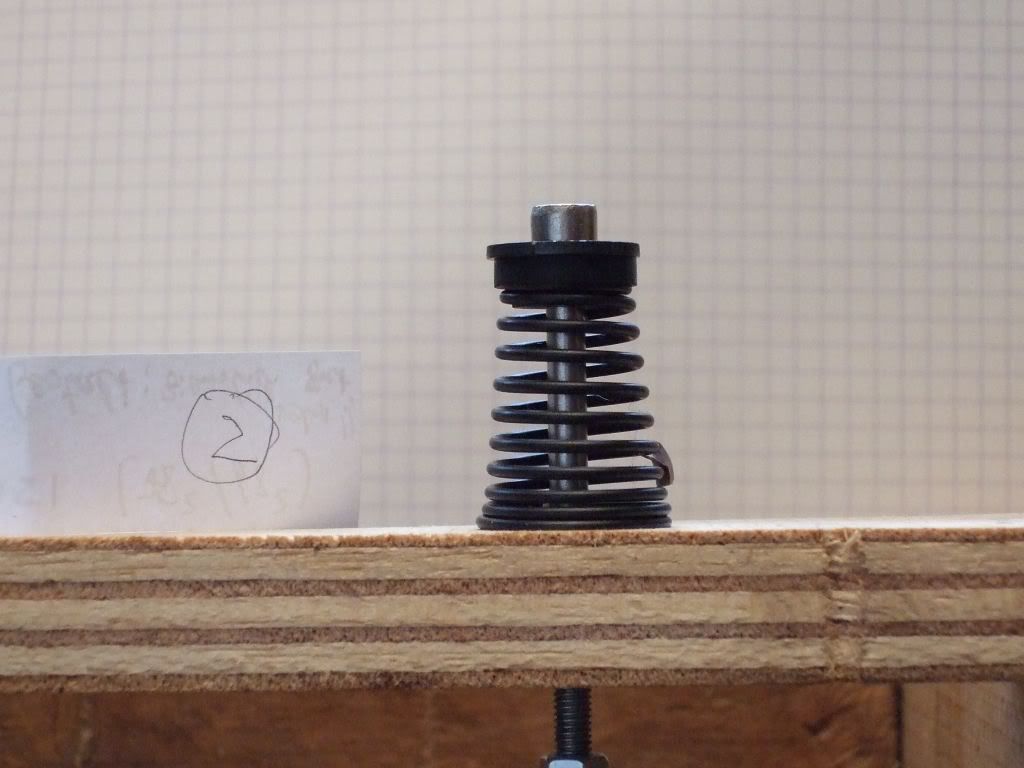
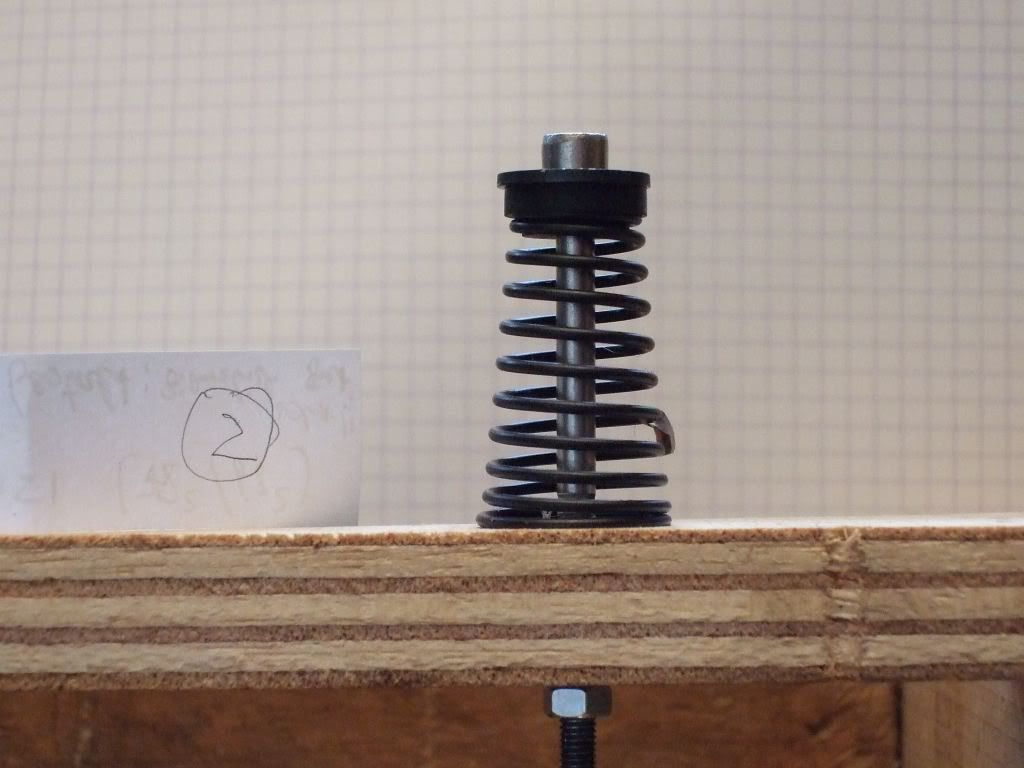
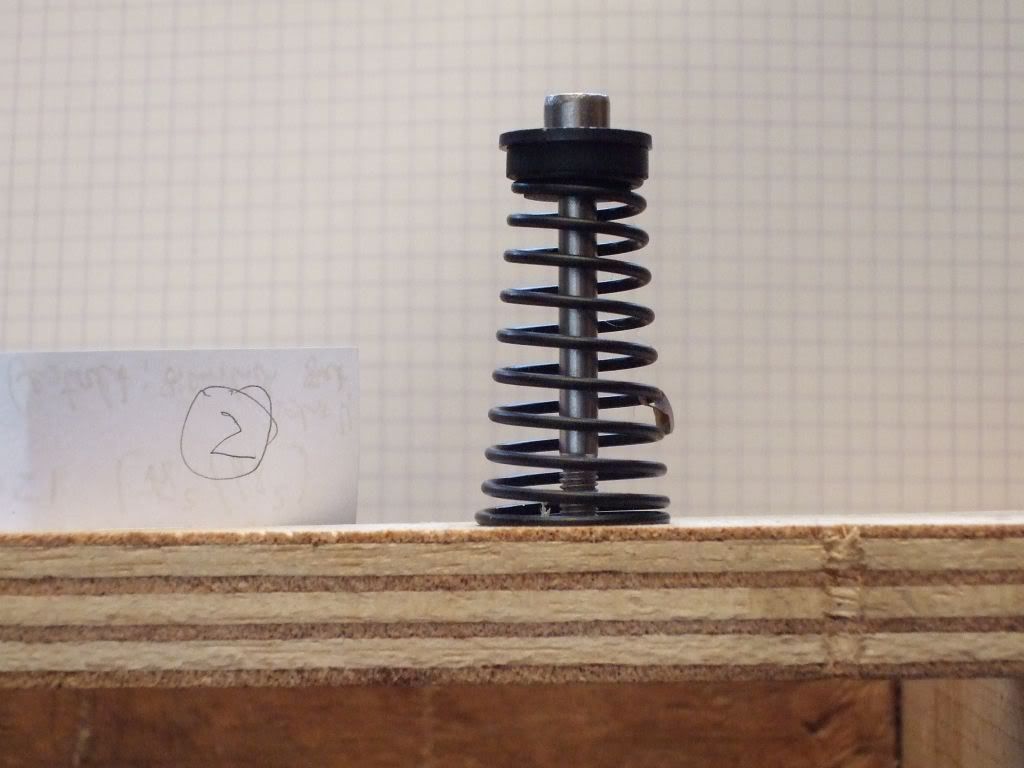
As can be seen, this is spring nr. 2.
- Tony Tune-age
- Very active member
- Posts: 1589
- Joined: 2009-12-19 19:07
- Location: United States
Don't want to spoil the flow, but another question in addition to Tony's - the bounce on my deck is great, so what can be gained from this investigation? Do you suspect the bounce could be improved upon even when it looks fine to the naked eye? Or maybe something else I'm missing... :?
FYI, Peter showed me a few new springs when servicing my deck and said that he gets through quite a lot when searching for good ones and the others just go straight in the bin. I guess that's common practice with any good dealer.
FYI, Peter showed me a few new springs when servicing my deck and said that he gets through quite a lot when searching for good ones and the others just go straight in the bin. I guess that's common practice with any good dealer.
- Tony Tune-age
- Very active member
- Posts: 1589
- Joined: 2009-12-19 19:07
- Location: United States
Depending on the cost for new springs, isn't it kind of expensive throwing them away :?: And why is it so difficult making Sondek springs that don't have to be thrown away :?:Charlie1 wrote:Don't want to spoil the flow, but another question in addition to Tony's - the bounce on my deck is great, so what can be gained from this investigation? Do you suspect the bounce could be improved upon even when it looks fine to the naked eye? Or maybe something else I'm missing... :?
FYI, Peter showed me a few new springs when servicing my deck and said that he gets through quite a lot when searching for good ones and the others just go straight in the bin. I guess that's common practice with any good dealer.
Tony Tune-age
Hi k numigl,
I have been following your research with the springs with great interest (initially on the Linn forum, and now here). Many thanks for sharing your findings and I hope that you don't mind my asking some questions.
Does any one know the total load experienced by the springs in a typical LP12 set up (assuming Ittok/Ekos arm)?
I just wonder whether subjecting each individual spring to a 1.5kg load is within the normal working tolerance.
I would also be interested in your views on testing the springs using your compression experiment pre and post cryogenic treatment.
Before any one decides to shoot me down in flames on this one (it has been misinterpreted on other forums!), I dont expect some magical improvement in sound quality as a result of the treatment.
My brother in law was a very successful cart (musn't say "go-cart"
) driver, and is now involved in racing car engineering. He has told me in the past that performance springs are cryogenically treated, as the process relieves stresses introduced in to the structure during manufacture, and results in greater consistancy in performance and longevity, due to changes in the type of crystal structure in the steel.
I have a spare set of springs, and will test them using your methods before and after treatment if you are interested, although it may take a little time (pressure of work and all that).
best wishes, Guy
I have been following your research with the springs with great interest (initially on the Linn forum, and now here). Many thanks for sharing your findings and I hope that you don't mind my asking some questions.
Does any one know the total load experienced by the springs in a typical LP12 set up (assuming Ittok/Ekos arm)?
I just wonder whether subjecting each individual spring to a 1.5kg load is within the normal working tolerance.
I would also be interested in your views on testing the springs using your compression experiment pre and post cryogenic treatment.
Before any one decides to shoot me down in flames on this one (it has been misinterpreted on other forums!), I dont expect some magical improvement in sound quality as a result of the treatment.
My brother in law was a very successful cart (musn't say "go-cart"
I have a spare set of springs, and will test them using your methods before and after treatment if you are interested, although it may take a little time (pressure of work and all that).
best wishes, Guy
I dont expect some magical improvement in sound quality as a result of the treatment.
Well, the Ittok sounds great, too :-), unless …..the bounce on my deck is great, so what can be gained from this investigation?
To remain serious: I frankly admit that I tried many things, but not to
deteriorate the spring settings deliberately. I can’t judge reliably the
effect of their good alignment on the sound. However, with all the efforts
reported to get the bolts truly plumb and to get a pistonic bounce, I expect
that those who have tried to compromise/improve a spring set up can tell
whether it is of great or of minor importance.
I discussed the spring shape with a few spring manufacturer technicians. All
confirm that excentricity under load is not a parameter which is normally
checked (or specified). As it is awkward to measure excentricity,
especially under load, it is regarded as too expensive and would require
both a definition and a realization of the procedure.
It was pointed out by some that a constant inclination angle of the turns results in an
inhomogeneous stiffness of the spring, with a weaker part at the big diameter side.
'Progressive' inclination (= steeper at big diameter end, less
steep at small diameter end) can be used to avoid early blocking of the
turns at the large diameter side whilst the turns at the small diameter side
are still little compressed. Being myself an absolute beginner in spring
technology, there’s little I could suggest myself. On one hand, I can’t imagine
that there’s no way to produce more concentric springs, on the other hand,
Linn decided perhaps that it’s not worth the effort – who knows. It is
also possible that nobody checks and dealers are expected to do the job…
Personally I find it a waste of time and springs. And I _expect_ that when
putting on and off of the hinges makes an effect, or turning the felt
mat upside down, or tighten the top plate bolt a bit less or more,
the quality of the springs can’t be unimportant.
(There’s a suggestion I can make: You can get them pre-washed
from the factory!)
The range of forces is reasonable: The outer platter is about 2500 g, the
subchassis about 900 g, the tonearm 500 to 600 g (Ekos ca. 510, SE ca. 620 g).
It is easy to check exact forces at each spring by measuring their
length when they are built in and have been adjusted (will do so next time
I open my deck).
Is a cryo-treatment as simple as putting the springs in a freezer? What
temperature cycle is involved?
Depends on your freezer :lol:
But to be serious, here is a short explanation of some of the science (Austenite and Martensite are two different crystal structures):
Cryogenics, or deep freezing is done to make sure there is no retained Austenite during quenching. When steel is at the hardening temperature, there is a solid solution of Carbon and Iron, known as Austenite. The amount of Martensite formed at quenching is a function of the lowest temperature encountered. At any given temperature of quenching there is a certain amount of Martensite and the balance is untransformed Austenite. This untransformed austenite is very brittle and can cause loss of strength or hardness, dimensional instability, or cracking.
In Cryogenic treatment the material is subject to deep freeze temperatures of as low as -185°C (-301°F), but usually -75°C (-103°F) is sufficient. The Austenite is unstable at this temperature, and the whole structures becomes Martensite.
I know of a company (fairly local to me), which treats metal components. Over the next few months I will endevour to try out the experiment - I have a feeling that some of the eccentricity in the spring may be due to stresses introduced during manufacture, and who knows, perhaps cryogenic treatment may relieve some of these stresses (no magic involved
). Worth a bash anyway.
best wishes, Guy
But to be serious, here is a short explanation of some of the science (Austenite and Martensite are two different crystal structures):
Cryogenics, or deep freezing is done to make sure there is no retained Austenite during quenching. When steel is at the hardening temperature, there is a solid solution of Carbon and Iron, known as Austenite. The amount of Martensite formed at quenching is a function of the lowest temperature encountered. At any given temperature of quenching there is a certain amount of Martensite and the balance is untransformed Austenite. This untransformed austenite is very brittle and can cause loss of strength or hardness, dimensional instability, or cracking.
In Cryogenic treatment the material is subject to deep freeze temperatures of as low as -185°C (-301°F), but usually -75°C (-103°F) is sufficient. The Austenite is unstable at this temperature, and the whole structures becomes Martensite.
I know of a company (fairly local to me), which treats metal components. Over the next few months I will endevour to try out the experiment - I have a feeling that some of the eccentricity in the spring may be due to stresses introduced during manufacture, and who knows, perhaps cryogenic treatment may relieve some of these stresses (no magic involved
best wishes, Guy
Very interesting following the information on springs - especially as it is someone else doing the work! :D
Personally you can skip number 7, I'll just go with 2, 4 and 21.
However, as Klaus points out, there are more variables than one in the springs and just having these three will still not guarantee that you can just fit them and have a magic pistonic bounce without any twiddling. From the photos i would say that 1500 g is within the range of normal spring compression. While it is a bit hard to tell without grommets in place my guess would be that the compression is less than typical on the back spring by the tonearm base but more than the one by the front of the armboard.
I do think the cryogenic treatment could certainly be a partial solution. Evening out the stresses in their manufacture can only help with consistency.
Basically, the current system is based on the dealer's skill and their dedication to getting your LP12 right. While the newer springs are better they are still not uniform, either statically or under tension, as Klaus has shown. Not only are they not mostly concentric but the tops and bottoms are not always level with each other. The good thing is that, at least as LP12 parts go, the springs are relatively cheap. So it is not too costly to throw them away. But also getting the bounce right is really about balancing the various non-linear forces to get them operating together in a basically linear fashion - not only balancing out the effects of eccentricity on the action of the spring but also of the different compression of each spring. So it really is about trial and error. I can tell you from experience that some LP12s seem to just fight you and require a few parts swaps and a fair bit of fiddling before they bounce well and others are fairly simple. I just finished doing an LP12 belonging to a friend who used to work for Linn and I fought for quite some time to get a really good bounce out of it. I straightened the bolts, swapped all three springs, one of them twice, and a couple upper grommets and did a fair bit of twiddling before I was happy with the suspension. When I mentioned this to the owner he allowed that he had never been able to get it to bounce well despite having swapped springs two different times! Other LP12s I really don't have to do that much to.
The good news is that it has been getting better. My experience is that the Keel is much more intolerant of the bolts not being perfectly straight but once they are it seems to also be easier to get a good bounce than with the steel subchassis. I believe this is because the upper grommet is a more precise fit in the Keel than the steel subchassis. So a Keel with really straight bolts and newer springs tends to be less work. But improved springs would certainly make things easier for us - as would perfectly straight bolts and perfectly cut locknuts but I'm not holding my breath. Making these items to the tolerances we would like is likely to be very expensive if Linn could even find a company to make them. And as Klaus points out the proper parameters haven't even been specified by the industry. Face it, bolts, springs, grommets and nuts were not designed with the usage we put them to in mind. Think how much more it costs to make a truly high precision subchassis compared to a standard one: Keel $3250, steel subchassis/armboard about $180. What would the LP12 sell for it all the springs, bolts and nuts were 18 times as expensive? What if they were 50 or 100 times as expensive (after all the standard subchassis and armbaord are still custom made parts while the nuts and bolts are likely stock off the shelf items)?
In the end I'm just glad the LP12 works as well as it does as it still outperforms anything else I've heard. And as one who will soon be celebrating my 33 1/3rd anniversary setting up LP12s, I have to say: "You should have tried to set them up 30 years ago!"
Personally you can skip number 7, I'll just go with 2, 4 and 21.
I do think the cryogenic treatment could certainly be a partial solution. Evening out the stresses in their manufacture can only help with consistency.
Basically, the current system is based on the dealer's skill and their dedication to getting your LP12 right. While the newer springs are better they are still not uniform, either statically or under tension, as Klaus has shown. Not only are they not mostly concentric but the tops and bottoms are not always level with each other. The good thing is that, at least as LP12 parts go, the springs are relatively cheap. So it is not too costly to throw them away. But also getting the bounce right is really about balancing the various non-linear forces to get them operating together in a basically linear fashion - not only balancing out the effects of eccentricity on the action of the spring but also of the different compression of each spring. So it really is about trial and error. I can tell you from experience that some LP12s seem to just fight you and require a few parts swaps and a fair bit of fiddling before they bounce well and others are fairly simple. I just finished doing an LP12 belonging to a friend who used to work for Linn and I fought for quite some time to get a really good bounce out of it. I straightened the bolts, swapped all three springs, one of them twice, and a couple upper grommets and did a fair bit of twiddling before I was happy with the suspension. When I mentioned this to the owner he allowed that he had never been able to get it to bounce well despite having swapped springs two different times! Other LP12s I really don't have to do that much to.
The good news is that it has been getting better. My experience is that the Keel is much more intolerant of the bolts not being perfectly straight but once they are it seems to also be easier to get a good bounce than with the steel subchassis. I believe this is because the upper grommet is a more precise fit in the Keel than the steel subchassis. So a Keel with really straight bolts and newer springs tends to be less work. But improved springs would certainly make things easier for us - as would perfectly straight bolts and perfectly cut locknuts but I'm not holding my breath. Making these items to the tolerances we would like is likely to be very expensive if Linn could even find a company to make them. And as Klaus points out the proper parameters haven't even been specified by the industry. Face it, bolts, springs, grommets and nuts were not designed with the usage we put them to in mind. Think how much more it costs to make a truly high precision subchassis compared to a standard one: Keel $3250, steel subchassis/armboard about $180. What would the LP12 sell for it all the springs, bolts and nuts were 18 times as expensive? What if they were 50 or 100 times as expensive (after all the standard subchassis and armbaord are still custom made parts while the nuts and bolts are likely stock off the shelf items)?
In the end I'm just glad the LP12 works as well as it does as it still outperforms anything else I've heard. And as one who will soon be celebrating my 33 1/3rd anniversary setting up LP12s, I have to say: "You should have tried to set them up 30 years ago!"